A muffle furnace is a critical piece of equipment used in laboratories and industrial settings for high-temperature applications such as ashing, sintering, and heat treatment. It is designed to provide uniform heating while protecting samples from direct exposure to heating elements. The furnace consists of several key components, including the heating elements, insulation materials, the muffle chamber, temperature control systems, and safety features. These parts work together to ensure precise temperature regulation, efficient heat distribution, and safe operation. Understanding the components of a muffle furnace is essential for proper usage, maintenance, and purchasing decisions.
Key Points Explained:
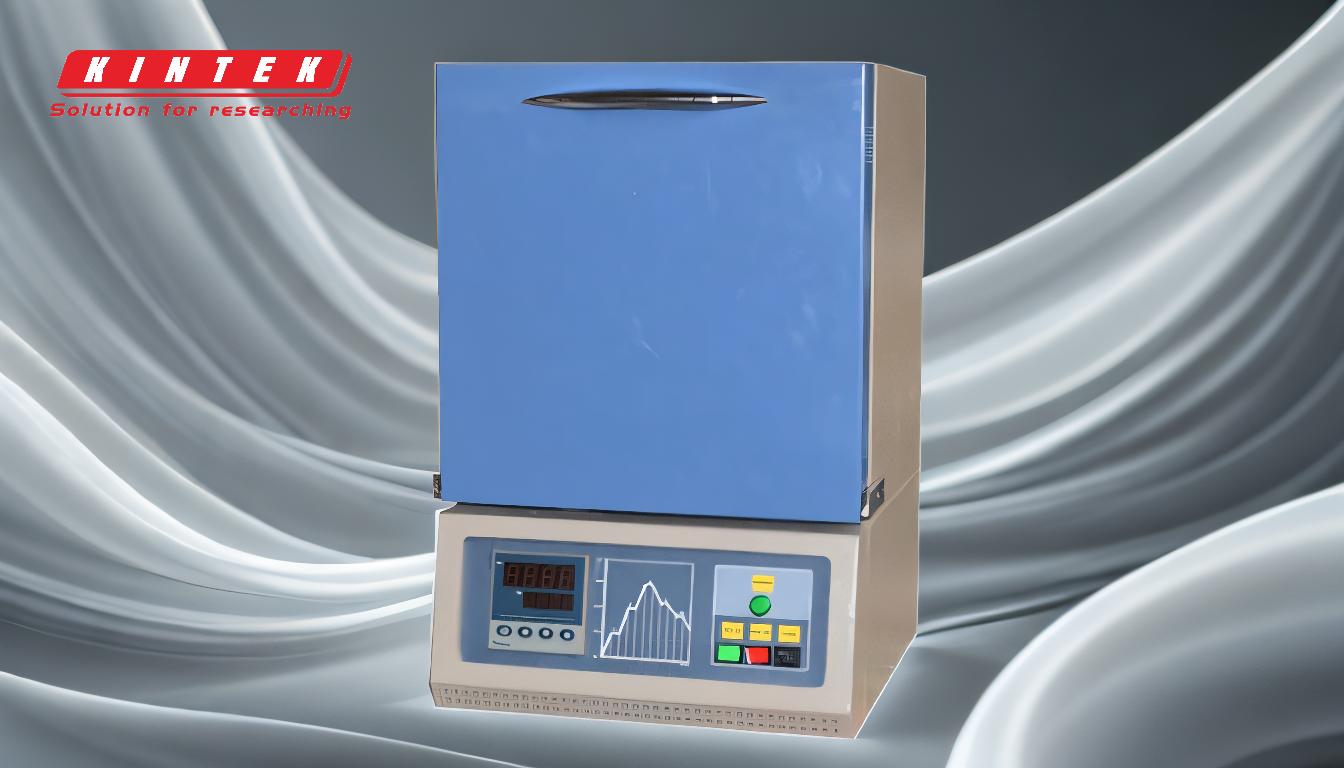
-
Heating Elements:
- Heating elements are the core components that generate heat within the furnace. They are typically made of resistance wire (such as nichrome or kanthal) or ceramic materials.
- These elements are strategically placed around the muffle chamber to ensure uniform heat distribution.
- The choice of material depends on the maximum operating temperature required for the application.
-
Muffle Chamber:
- The muffle chamber, or muffle, is a refractory-lined enclosure where samples are placed. It is constructed from materials like silica, alumina, or other high-temperature-resistant ceramics.
- The chamber acts as a barrier, preventing direct contact between the heating elements and the samples, which ensures uniform heating and protects the samples from contamination.
- The refractory lining provides excellent insulation, minimizing heat loss and improving energy efficiency.
-
Insulation Materials:
- Insulation is crucial for maintaining high temperatures within the furnace and protecting the external enclosure from excessive heat.
- Common insulation materials include ceramic fiber, refractory bricks, and other high-temperature-resistant materials.
- Proper insulation ensures energy efficiency and reduces the risk of heat-related damage to the surrounding environment.
-
Temperature Control Systems:
- The temperature control system includes a thermocouple, temperature controller, and control panel.
- The thermocouple measures the temperature inside the chamber and sends electrical signals to the control panel.
- The temperature controller regulates the heat output to maintain the desired temperature, while the control panel allows users to set and monitor temperature, timer, and other parameters.
-
Control Panel:
- The control panel is the interface for operating the furnace. It typically includes:
- A temperature controller for setting and maintaining the desired temperature.
- A timer for automating the heating process.
- A safety switch to cut off power in case of overheating or other malfunctions.
- Advanced models may include digital displays, programmable settings, and data logging capabilities.
- The control panel is the interface for operating the furnace. It typically includes:
-
External Enclosure:
- The external enclosure is the outer shell of the furnace, usually made of steel or other durable materials.
- It houses the internal components and provides additional insulation to protect users from high external temperatures.
- The enclosure also includes a release hole or exhaust system to vent gases or fumes generated during heating processes.
-
Safety Features:
- Safety is a critical aspect of muffle furnace design. Key safety features include:
- A safety switch to automatically cut off power in case of overheating or other issues.
- Insulated handles and doors to prevent burns during operation.
- Alarms or indicators to alert users of abnormal conditions.
- These features ensure safe operation and minimize the risk of accidents.
- Safety is a critical aspect of muffle furnace design. Key safety features include:
-
Optional Components:
- Some muffle furnaces may include additional features, such as:
- An exhaust system to vent harmful gases or fumes.
- Viewing windows to monitor samples without opening the chamber.
- Programmable controllers for complex heating cycles.
- These optional components enhance the functionality and versatility of the furnace.
- Some muffle furnaces may include additional features, such as:
By understanding these components, users can make informed decisions when purchasing, operating, and maintaining a muffle furnace. Each part plays a vital role in ensuring efficient, safe, and precise high-temperature processing.
Summary Table:
Component | Function |
---|---|
Heating Elements | Generate heat; made of nichrome, kanthal, or ceramics for uniform heating. |
Muffle Chamber | Protects samples from direct heat; made of high-temperature-resistant ceramics. |
Insulation Materials | Maintain high temperatures; includes ceramic fiber and refractory bricks. |
Control Panel | Interface for temperature control, timers, and safety features. |
Safety Features | Includes safety switches, insulated handles, and alarms for safe operation. |
Optional Components | Exhaust systems, viewing windows, and programmable controllers for versatility. |
Ready to enhance your lab's efficiency? Contact us today to find the perfect muffle furnace for your needs!