Precursor gases in Plasma-Enhanced Chemical Vapor Deposition (PECVD) are critical for achieving high-quality thin films with desired properties such as uniformity, electrical resistance, and surface roughness. These gases must be volatile, leave no impurities in the deposited films, and produce byproducts that are easily removable under vacuum conditions. Common precursor gases include silane (SiH4), ammonia (NH3), nitrous oxide (N2O), and nitrogen (N2), among others. The PECVD process relies on plasma to decompose these gases into reactive species, enabling chemical reactions at lower temperatures than traditional CVD methods. This makes PECVD a versatile and efficient technique for depositing thin films in applications like semiconductor manufacturing and solar cell production.
Key Points Explained:
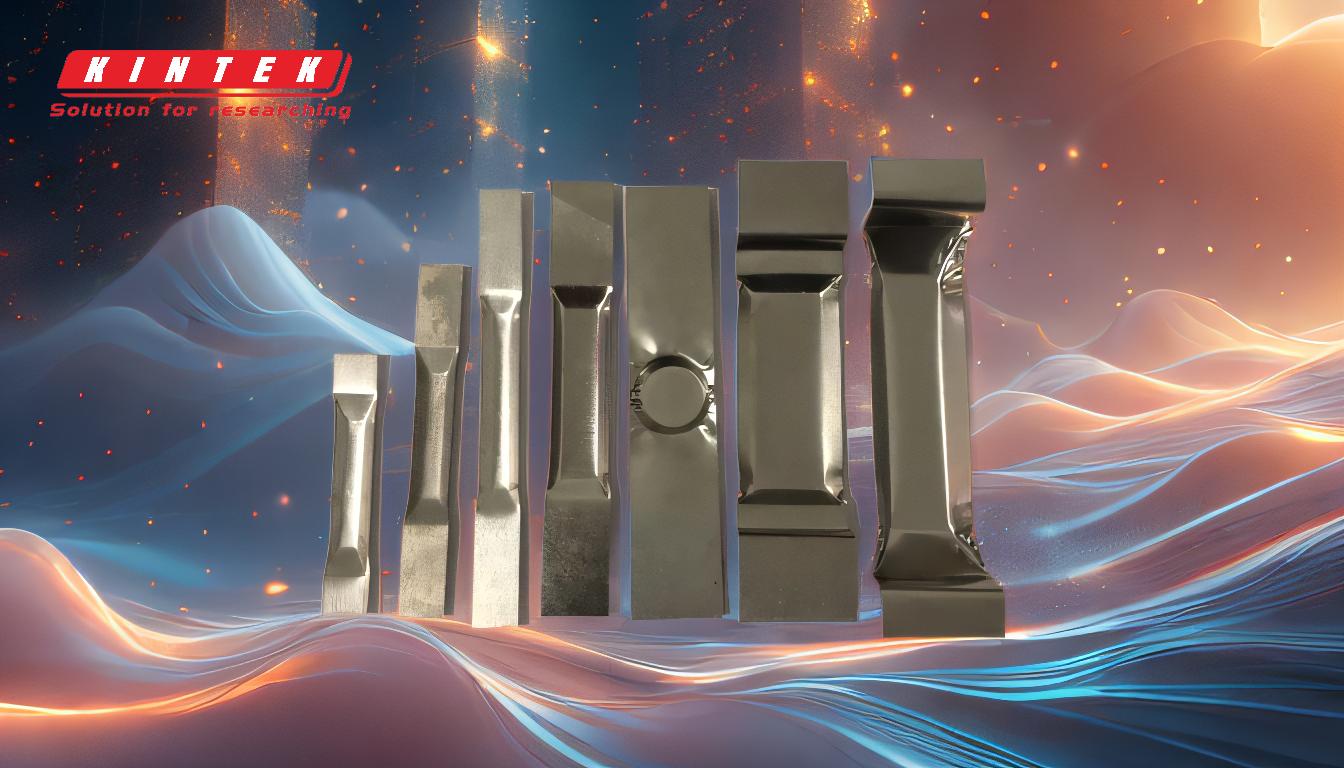
-
Volatility and Purity of Precursor Gases:
- Precursor gases in PECVD must be volatile to ensure they can be easily introduced into the reaction chamber and decomposed by the plasma. They should also leave no impurities in the deposited films, as contaminants can degrade the film's performance. For example, silane (SiH4) is a common precursor because it is highly volatile and produces high-purity silicon films.
-
Desired Film Properties:
- The choice of precursor gases directly influences the properties of the deposited films, such as uniformity, electrical resistance, and surface roughness. For instance, ammonia (NH3) is often used alongside silane to deposit silicon nitride films, which are known for their excellent electrical insulation and mechanical stability.
-
Byproducts and Vacuum Conditions:
- All byproducts generated during the PECVD process must be volatile and easily removable under vacuum conditions. This ensures that the reaction chamber remains clean and that the deposited films are free from contamination. For example, the use of nitrous oxide (N2O) in PECVD processes results in byproducts like nitrogen and water vapor, which are easily pumped out of the system.
-
Common Precursor Gases:
- Silane (SiH4): A widely used precursor for depositing silicon-based films. It is highly reactive in the presence of plasma and produces high-quality silicon films.
- Ammonia (NH3): Often used in combination with silane to deposit silicon nitride films, which are used for passivation and insulation layers.
- Nitrous Oxide (N2O): Used to deposit silicon dioxide films, which are essential for gate dielectrics in semiconductor devices.
- Nitrogen (N2): Used as a carrier gas or to dilute reactive gases, helping to control the deposition rate and film properties.
-
Plasma Activation:
- The plasma in PECVD decomposes the precursor gases into reactive species, enabling chemical reactions at lower temperatures. This is a key advantage of PECVD over traditional thermal CVD, as it allows for the deposition of high-quality films on temperature-sensitive substrates.
-
Applications of PECVD:
- PECVD is widely used in the semiconductor industry for depositing thin films on silicon wafers. It is also used in the production of solar cells, where it is employed to deposit anti-reflective coatings that improve the efficiency of the cells.
-
Microscopic Processes in PECVD:
- The PECVD process involves several microscopic steps, including the collision of gas molecules with plasma electrons, the diffusion of reactive species to the substrate, and the deposition of chemical groups on the substrate surface. These steps are carefully controlled to ensure the desired film properties are achieved.
-
Equipment and Process Parameters:
- PECVD equipment typically operates at reduced gas pressures (50 mtorr to 5 torr) and uses RF fields (100 kHz to 40 MHz) to sustain the plasma. The electron and positive ion densities in the plasma range from 10^9 to 10^11/cm^3, with average electron energies between 1 and 10 eV. These parameters are optimized to achieve efficient decomposition of the precursor gases and high-quality film deposition.
By carefully selecting precursor gases and controlling the PECVD process parameters, manufacturers can achieve thin films with the desired properties for a wide range of applications.
Summary Table:
Precursor Gas | Role in PECVD | Common Applications |
---|---|---|
Silane (SiH4) | Deposits silicon-based films | Semiconductors, solar cells |
Ammonia (NH3) | Forms silicon nitride films | Passivation, insulation layers |
Nitrous Oxide (N2O) | Deposits silicon dioxide films | Gate dielectrics |
Nitrogen (N2) | Carrier gas, dilutes reactive gases | Controls deposition rate |
Optimize your PECVD process with the right precursor gases—contact our experts today for tailored solutions!