The principles of an induction furnace revolve around the use of electromagnetic induction to generate heat within a conductive material. The furnace consists of key components such as a power supply, induction coil, crucible, and control system. When an alternating current passes through the induction coil, it creates a fluctuating magnetic field. This magnetic field induces eddy currents within the conductive material placed inside the crucible, causing it to heat up due to resistance. The result is efficient, uniform heating or melting of the material, making induction furnaces ideal for applications requiring precise temperature control and consistent material properties.
Key Points Explained:
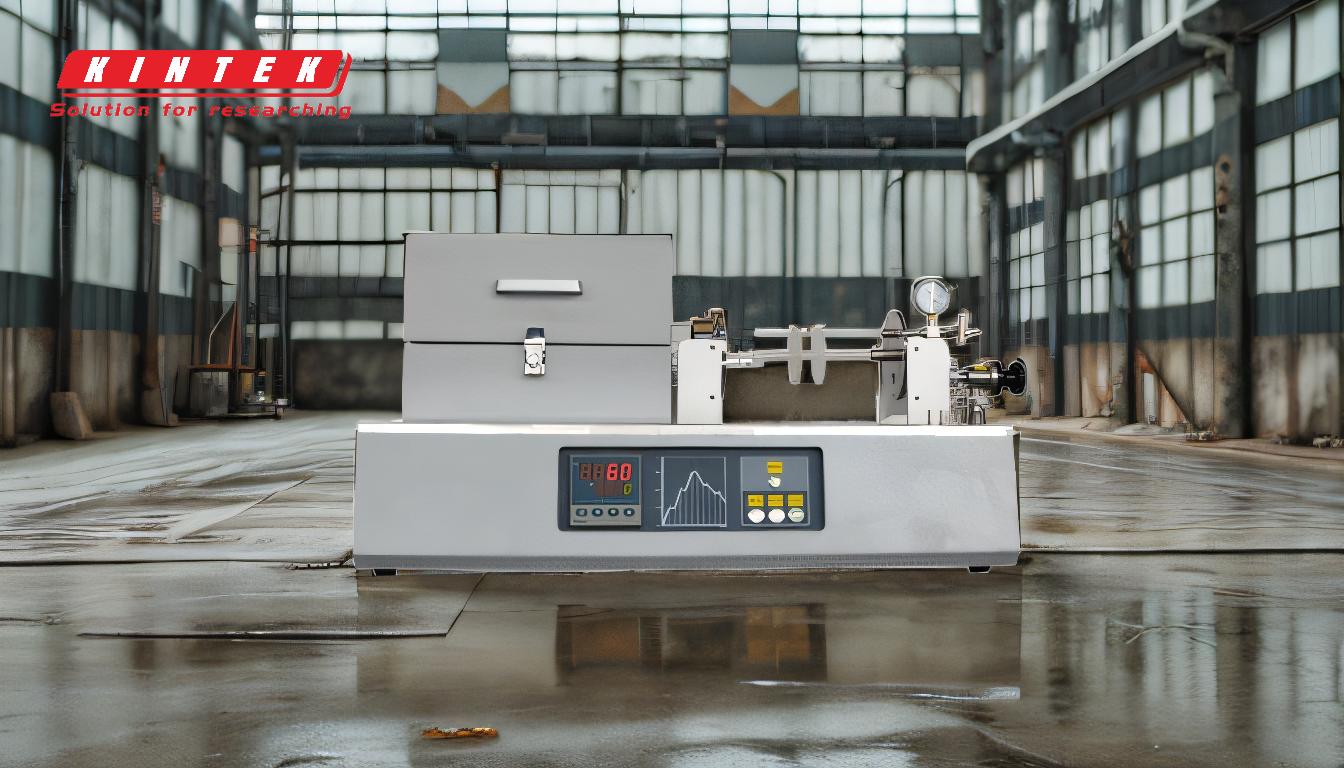
-
Electromagnetic Induction:
- The core principle of an induction furnace is electromagnetic induction. When an alternating current flows through the induction coil, it generates a rapidly changing magnetic field. This magnetic field penetrates the conductive material (e.g., metal) placed inside the crucible, inducing eddy currents within the material. These eddy currents generate heat due to the material's electrical resistance, leading to efficient heating or melting.
-
Key Components of an Induction Furnace:
- Power Supply: Provides the alternating current required to generate the magnetic field. Modern induction furnaces often use advanced power supplies like IGBT induction furnaces, which offer precise control and energy efficiency.
- Induction Coil: A copper coil that carries the alternating current and creates the magnetic field. The coil is typically water-cooled to prevent overheating.
- Crucible: Made of refractory materials, the crucible holds the material to be heated or melted. It must withstand high temperatures and chemical reactions.
- Capacitor: Used to tune the circuit to the desired frequency, ensuring efficient energy transfer.
- Control System: Monitors and regulates the furnace's operation, including temperature, power input, and cooling systems.
-
Uniform Heating and Melting:
- Induction furnaces provide uniform heating because the eddy currents are distributed throughout the material. This uniformity ensures consistent composition and temperature, which is critical for applications like metal casting and alloy production. Unlike traditional furnaces, induction heating avoids direct contact between the heat source and the material, reducing contamination.
-
Advantages of Induction Furnaces:
- Energy Efficiency: Induction furnaces convert electrical energy directly into heat with minimal losses.
- Precision Control: Advanced control systems allow for precise temperature regulation, making them suitable for sensitive processes.
- Clean Operation: Since there is no combustion, induction furnaces produce fewer emissions and contaminants.
- Compact Design: The absence of a combustion chamber makes induction furnaces more compact and easier to integrate into production lines.
-
Applications of Induction Furnaces:
- Induction furnaces are widely used in industries such as metallurgy, foundries, and manufacturing. They are ideal for melting metals like steel, iron, aluminum, and copper, as well as for heat treatment processes like annealing, hardening, and tempering.
By leveraging the principles of electromagnetic induction, induction furnaces offer a highly efficient and controllable method for heating and melting materials. The integration of advanced technologies like IGBT-based power supplies further enhances their performance, making them indispensable in modern industrial processes.
Summary Table:
Key Aspect | Description |
---|---|
Electromagnetic Induction | Alternating current in the coil creates a magnetic field, inducing eddy currents in the material for heating. |
Key Components | Power supply, induction coil, crucible, capacitor, and control system. |
Uniform Heating | Eddy currents ensure consistent heating, ideal for metal casting and alloys. |
Advantages | Energy-efficient, precise temperature control, clean operation, compact design. |
Applications | Used in metallurgy, foundries, and manufacturing for melting and heat treatment. |
Discover how an induction furnace can optimize your industrial processes—contact our experts today!