Electric arc furnaces (EAFs) are widely used in steel production due to their flexibility, efficiency, and ability to recycle scrap metal. However, they come with several challenges, including high energy consumption, strain on electrical systems, and the need for careful energy management. While they offer significant advantages, such as the ability to produce a wide range of steel grades and low capital costs, these benefits are often offset by operational difficulties. Below, we explore the key problems associated with electric arc furnaces in detail.
Key Points Explained:
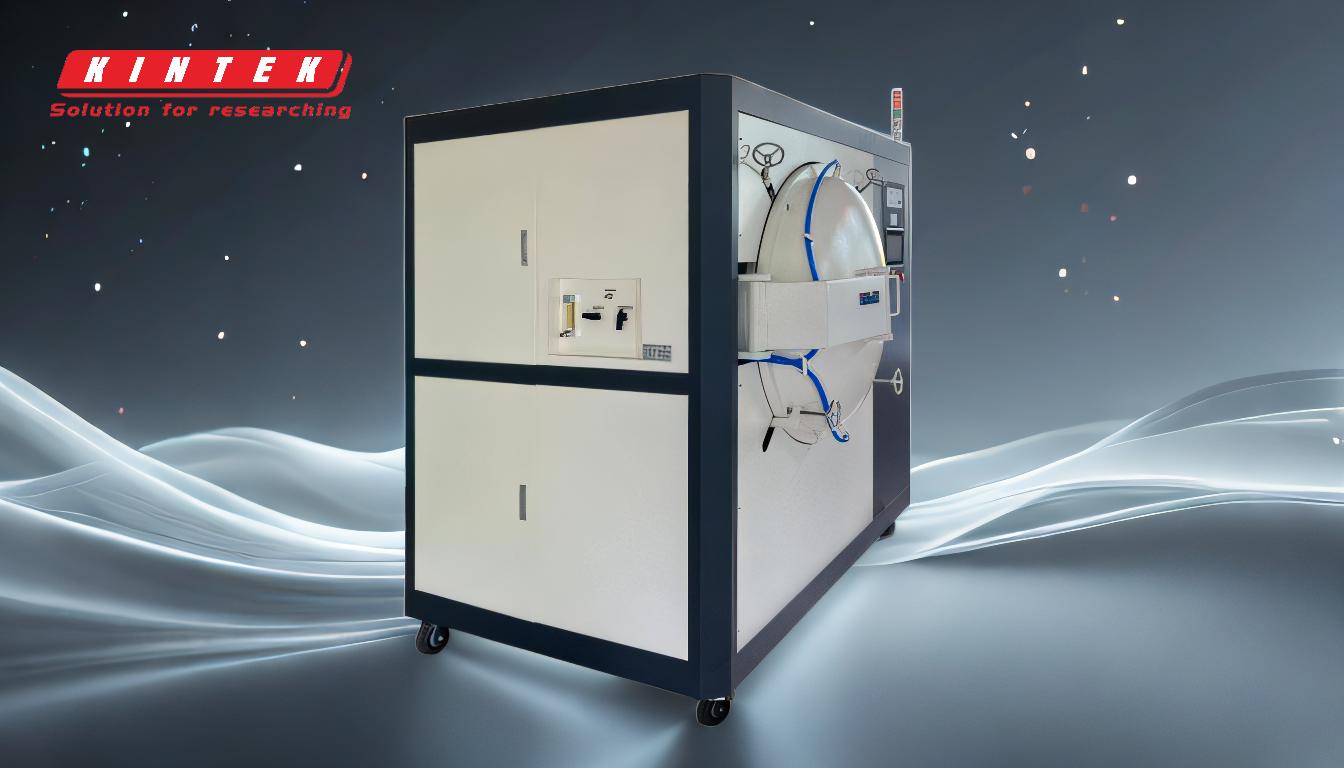
-
High Energy Consumption:
- Electric arc furnaces are energy-intensive, requiring large amounts of electricity to generate the high temperatures needed for melting metal. This high energy demand can strain local electrical grids, especially in areas with limited power infrastructure.
- The reliance on electricity also makes EAFs susceptible to fluctuations in energy prices, which can significantly impact operational costs.
-
Strain on Electrical Systems:
- The substantial power requirements of EAFs can lead to voltage instability and power quality issues in the surrounding electrical network. This can affect not only the furnace operation but also other equipment and facilities connected to the same grid.
- Utilities may need to invest in infrastructure upgrades to support the high power demands of EAFs, which can be costly and time-consuming.
-
Energy Management Challenges:
- Efficient operation of an electric arc furnace requires precise control of energy input to maintain optimal melting conditions. Poor energy management can lead to inefficiencies, increased energy consumption, and higher operating costs.
- Operators must carefully monitor and adjust parameters such as arc length, electrode position, and power input to ensure consistent performance and energy efficiency.
-
Environmental Concerns:
- While EAFs are often touted for their ability to recycle scrap metal, the production process can still generate significant emissions, including dust, fumes, and greenhouse gases. Proper filtration and emission control systems are essential to mitigate these environmental impacts.
- The high energy consumption of EAFs also contributes to their carbon footprint, especially if the electricity is generated from non-renewable sources.
-
Operational Flexibility vs. Stability:
- Although EAFs offer flexibility in terms of starting and stopping operations as needed, this can lead to inconsistent production rates and challenges in maintaining a stable supply of steel.
- Frequent starts and stops can also increase wear and tear on the furnace components, leading to higher maintenance costs and potential downtime.
-
Dependence on Scrap Quality:
- The quality of the scrap metal used in EAFs can significantly affect the quality of the final steel product. Contaminants or impurities in the scrap can lead to defects in the steel, requiring additional processing steps to achieve the desired quality.
- Ensuring a consistent supply of high-quality scrap metal can be challenging, particularly in regions with limited recycling infrastructure.
-
Noise and Vibrations:
- The operation of electric arc furnaces generates significant noise and vibrations, which can be disruptive to surrounding communities and require additional measures to mitigate.
In summary, while electric arc furnaces offer numerous advantages, including flexibility, efficiency, and the ability to recycle scrap metal, they also present several challenges. These include high energy consumption, strain on electrical systems, environmental concerns, and operational difficulties related to energy management and scrap quality. Addressing these issues requires careful planning, investment in infrastructure, and ongoing monitoring to ensure efficient and sustainable operation.
Summary Table:
Problem | Description |
---|---|
High Energy Consumption | Requires large electricity amounts, strains grids, and is costly. |
Strain on Electrical Systems | Causes voltage instability and requires costly infrastructure upgrades. |
Energy Management Challenges | Poor energy control leads to inefficiencies and higher operating costs. |
Environmental Concerns | Generates emissions and has a high carbon footprint. |
Operational Flexibility | Frequent starts/stops lead to inconsistent production and maintenance issues. |
Dependence on Scrap Quality | Low-quality scrap affects steel quality and requires additional processing. |
Noise and Vibrations | Disrupts surrounding communities and requires mitigation measures. |
Struggling with electric arc furnace challenges? Contact our experts today for tailored solutions!