Vapor phase deposition (VPD) encompasses two primary techniques: Chemical Vapor Deposition (CVD) and Physical Vapor Deposition (PVD). Both processes involve the deposition of thin films onto substrates but differ in their mechanisms and applications. CVD relies on chemical reactions to form coatings, while PVD uses physical processes like evaporation or sputtering. This explanation will break down the processes of both CVD and PVD, highlighting their key steps, methods, and applications.
Key Points Explained:
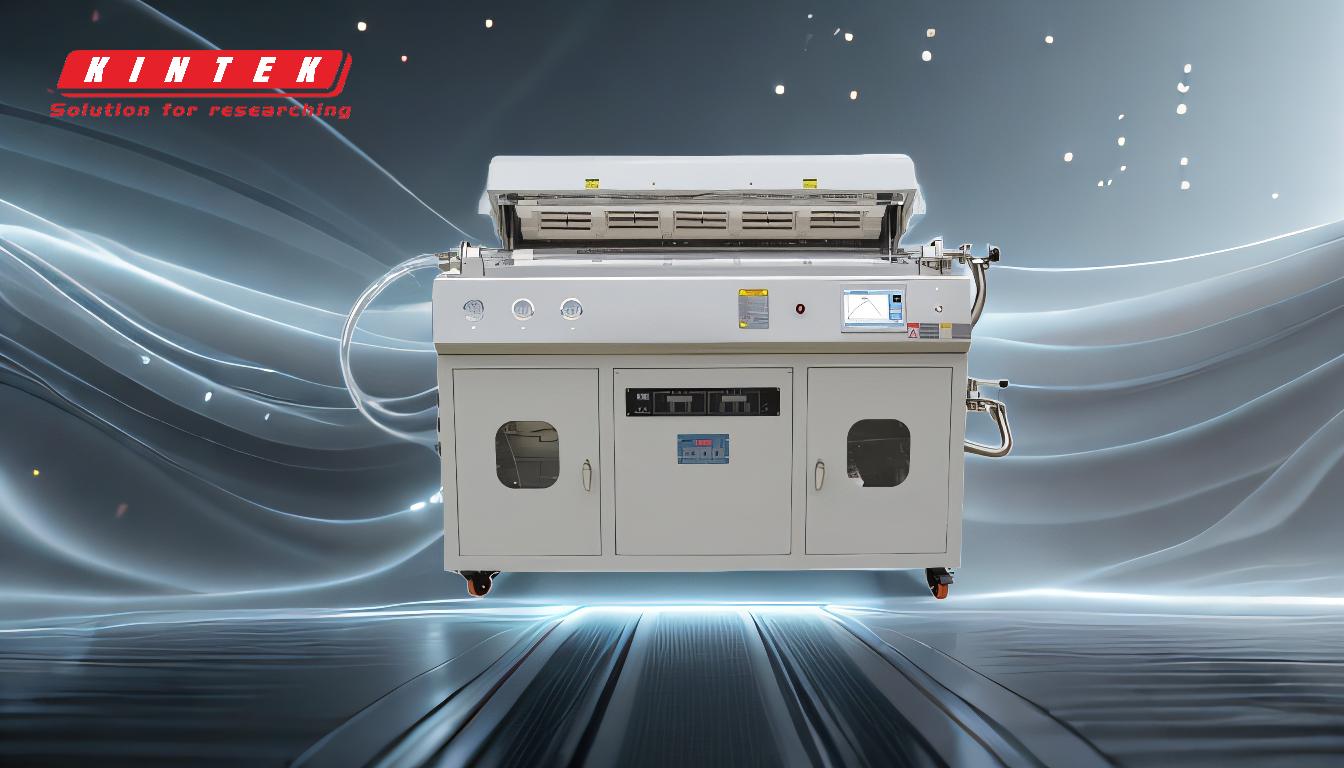
-
Chemical Vapor Deposition (CVD) Process
- Transport of Reacting Gaseous Species: In CVD, precursor gases are introduced into a reaction chamber and transported to the substrate surface. This step ensures that the reactive species reach the surface uniformly.
- Adsorption on the Surface: The gaseous species adsorb onto the substrate surface, forming a thin layer of reactive molecules.
- Surface-Catalyzed Reactions: Chemical reactions occur on the substrate surface, often catalyzed by heat or plasma, leading to the formation of the desired thin film.
- Surface Diffusion and Growth: The reactive species diffuse across the surface to growth sites, where nucleation and film growth occur.
- Desorption and Removal of Byproducts: Gaseous reaction products desorb from the surface and are transported away from the reaction chamber, ensuring a clean deposition process.
- Applications: CVD is widely used in semiconductor manufacturing, coatings for wear resistance, and creating high-purity films.
- Equipment: A chemical vapor deposition machine is essential for this process, providing controlled environments for precise film deposition.
-
Physical Vapor Deposition (PVD) Process
- Evaporation: In PVD, the material to be deposited is vaporized using high-energy sources like electron beams or plasma. This step dislodges atoms from the target material, creating a vapor.
- Transportation: The vaporized atoms are transported through a vacuum or low-pressure environment to the substrate.
- Reaction: In reactive PVD, the vaporized atoms react with introduced gases (e.g., oxygen or nitrogen) to form compounds like oxides, nitrides, or carbides.
- Deposition: The atoms or compounds condense on the substrate surface, forming a thin, uniform film.
- Methods: Common PVD methods include thermal vapor deposition, molecular beam epitaxy, and ion beam sputtering deposition. These techniques produce highly pure and adherent films.
- Applications: PVD is used for decorative coatings, optical films, and wear-resistant coatings in industries like aerospace and automotive.
-
Comparison of CVD and PVD
- Mechanism: CVD relies on chemical reactions, while PVD uses physical processes like evaporation or sputtering.
- Temperature Requirements: CVD typically requires higher temperatures compared to PVD.
- Film Quality: CVD produces films with excellent conformality and step coverage, while PVD films are highly pure and dense.
- Equipment Complexity: CVD systems are often more complex due to the need for precise gas delivery and reaction control, whereas PVD systems are simpler but require high vacuum conditions.
-
Choosing the Right Method
- For High-Purity Films: PVD is preferred due to its ability to produce extremely pure and uniform coatings.
- For Complex Geometries: CVD is ideal for coating complex shapes and achieving uniform thickness.
- For High-Temperature Applications: CVD is suitable for high-temperature processes, while PVD is better for lower-temperature applications.
By understanding the processes of vapor phase deposition, including the roles of chemical vapor deposition machines, manufacturers can select the appropriate method for their specific needs, ensuring high-quality thin films for various applications.
Summary Table:
Aspect | CVD | PVD |
---|---|---|
Mechanism | Chemical reactions | Physical processes (evaporation, sputtering) |
Temperature | High temperatures | Lower temperatures |
Film Quality | Excellent conformality and step coverage | Highly pure and dense films |
Equipment Complexity | Complex (precise gas delivery, reaction control) | Simpler (requires high vacuum conditions) |
Applications | Semiconductors, wear-resistant coatings, high-purity films | Decorative coatings, optical films, wear-resistant coatings |
Need help selecting the right vapor phase deposition method? Contact our experts today for personalized guidance!