After completing the sintering stage, several post-sintering processes are necessary to ensure the final product meets the desired specifications in terms of mechanical properties, dimensional accuracy, and surface finish. These processes include cooling, finishing, inspection, and sometimes additional treatments like heat treatment or surface coating. Each step is critical to achieving a high-quality, functional product.
Key Points Explained:
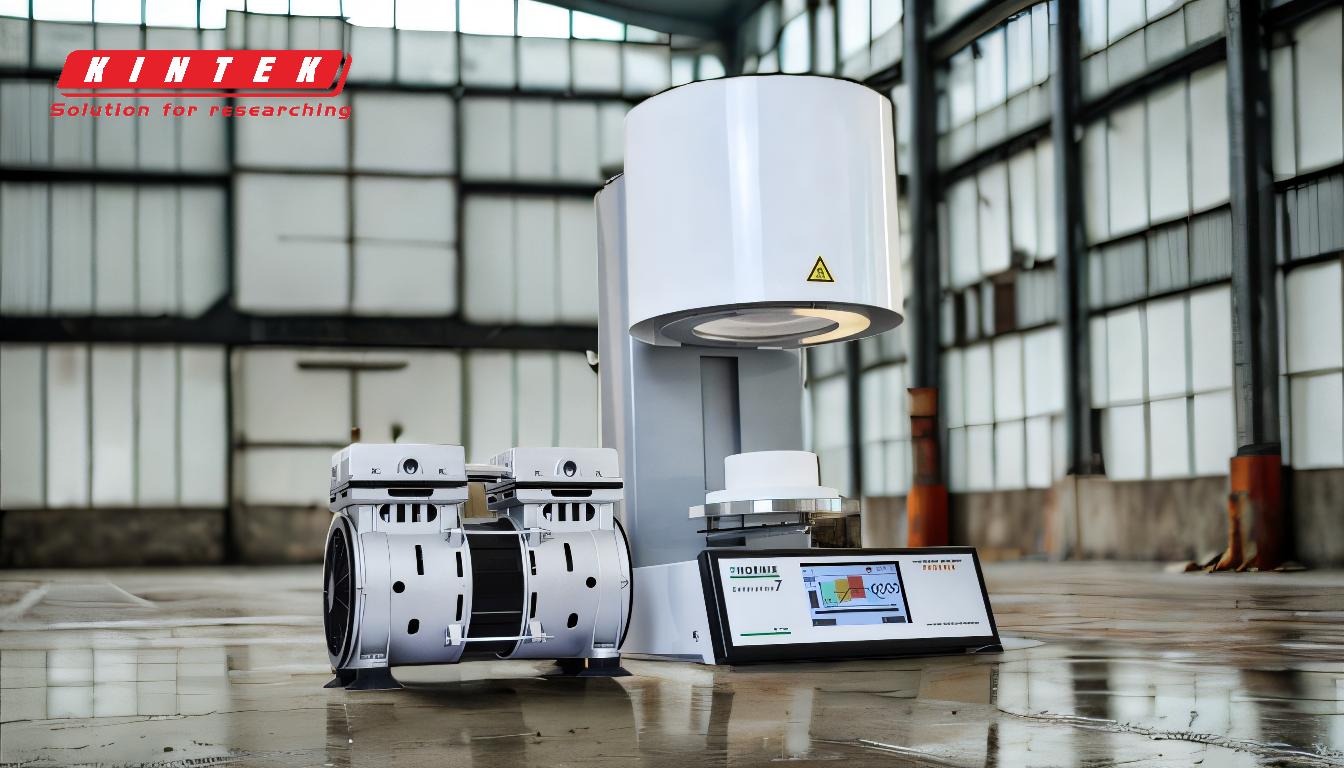
-
Cooling:
- Purpose: After sintering, the material is cooled to solidify it into a rigid and cohesive structure. Controlled cooling prevents thermal stresses and ensures uniform properties.
- Process: Cooling can be done in the sintering furnace itself or in a separate cooling chamber. The rate of cooling is carefully controlled to avoid cracking or warping.
- Importance: Proper cooling ensures the material retains its structural integrity and desired mechanical properties.
-
Finishing:
- Purpose: Finishing processes are used to achieve the desired surface finish and dimensional accuracy.
-
Processes:
- Machining: Post-sintering machining can be used to achieve tight tolerances and complex geometries.
- Grinding and Polishing: These processes improve surface finish and remove any surface imperfections.
- Deburring: Removing any sharp edges or burrs that may have formed during sintering.
- Importance: Finishing ensures the product meets the required specifications and is ready for use or further processing.
-
Inspection:
- Purpose: Inspection ensures the final product meets quality standards and specifications.
-
Processes:
- Dimensional Inspection: Checking the dimensions against the design specifications using tools like calipers, micrometers, or CMM (Coordinate Measuring Machine).
- Surface Inspection: Evaluating the surface finish and looking for defects like cracks, voids, or inclusions.
- Non-Destructive Testing (NDT): Techniques like ultrasonic testing, X-ray, or dye penetrant inspection to detect internal defects without damaging the part.
- Importance: Inspection is crucial for ensuring the reliability and performance of the final product.
-
Heat Treatment:
- Purpose: Heat treatment can be used to further enhance the mechanical properties of the sintered part.
-
Processes:
- Annealing: Used to relieve internal stresses and improve ductility.
- Quenching and Tempering: Used to increase hardness and strength.
- Importance: Heat treatment can significantly improve the performance of the sintered part, making it suitable for more demanding applications.
-
Surface Coating:
- Purpose: Surface coatings can be applied to improve wear resistance, corrosion resistance, or aesthetic appearance.
-
Processes:
- Plating: Electroplating or electroless plating to apply a thin layer of metal.
- Painting or Powder Coating: For aesthetic purposes or additional corrosion protection.
- Thermal Spraying: Applying a coating of another material using a high-temperature process.
- Importance: Surface coatings can extend the life of the product and improve its performance in harsh environments.
-
Final Assembly:
- Purpose: If the sintered part is a component of a larger assembly, it may need to be assembled with other parts.
-
Processes:
- Joining: Techniques like welding, brazing, or adhesive bonding may be used.
- Fastening: Using screws, bolts, or other fasteners to assemble parts.
- Importance: Final assembly ensures the part is ready for its intended application.
-
Packaging and Shipping:
- Purpose: Proper packaging and shipping ensure the product reaches its destination without damage.
-
Processes:
- Packaging: Using appropriate materials to protect the part during transit.
- Labeling: Ensuring the package is correctly labeled with part numbers, batch numbers, and handling instructions.
- Importance: Proper packaging and shipping are essential for customer satisfaction and the integrity of the final product.
In summary, the post-sintering processes are critical for transforming the sintered part into a finished product that meets all required specifications. Each step, from cooling to final assembly, plays a vital role in ensuring the quality, performance, and reliability of the final product.
Summary Table:
Process | Purpose | Key Steps | Importance |
---|---|---|---|
Cooling | Solidify material, prevent thermal stresses, and ensure uniform properties. | Controlled cooling in furnace or separate chamber. | Retains structural integrity and mechanical properties. |
Finishing | Achieve surface finish and dimensional accuracy. | Machining, grinding, polishing, deburring. | Ensures product meets specifications and is ready for use. |
Inspection | Verify quality standards and specifications. | Dimensional inspection, surface inspection, non-destructive testing (NDT). | Ensures reliability and performance of the final product. |
Heat Treatment | Enhance mechanical properties. | Annealing, quenching, tempering. | Improves performance for demanding applications. |
Surface Coating | Improve wear resistance, corrosion resistance, or aesthetics. | Plating, painting, powder coating, thermal spraying. | Extends product life and enhances performance in harsh environments. |
Final Assembly | Prepare part for its intended application. | Joining (welding, brazing), fastening (screws, bolts). | Ensures the part is ready for use in larger assemblies. |
Packaging | Protect product during transit. | Proper packaging materials, labeling. | Ensures customer satisfaction and product integrity. |
Optimize your post-sintering processes for superior results—contact our experts today!