Sintering is a critical thermal process used to densify powdered materials into solid components without melting them. It involves heating the material below its melting point, allowing particles to bond through diffusion, resulting in improved mechanical properties such as strength, durability, and density. Key factors influencing sintering include temperature, atmosphere, pressure, particle size, and composition. The process is highly customizable, with parameters like sintering temperature, cooling rate, and applied pressure tailored to achieve specific material properties. Sintering also impacts the microstructure of materials, affecting grain size, pore size, and grain boundary distribution. Understanding these properties is essential for optimizing the sintering process to meet desired performance requirements.
Key Points Explained:
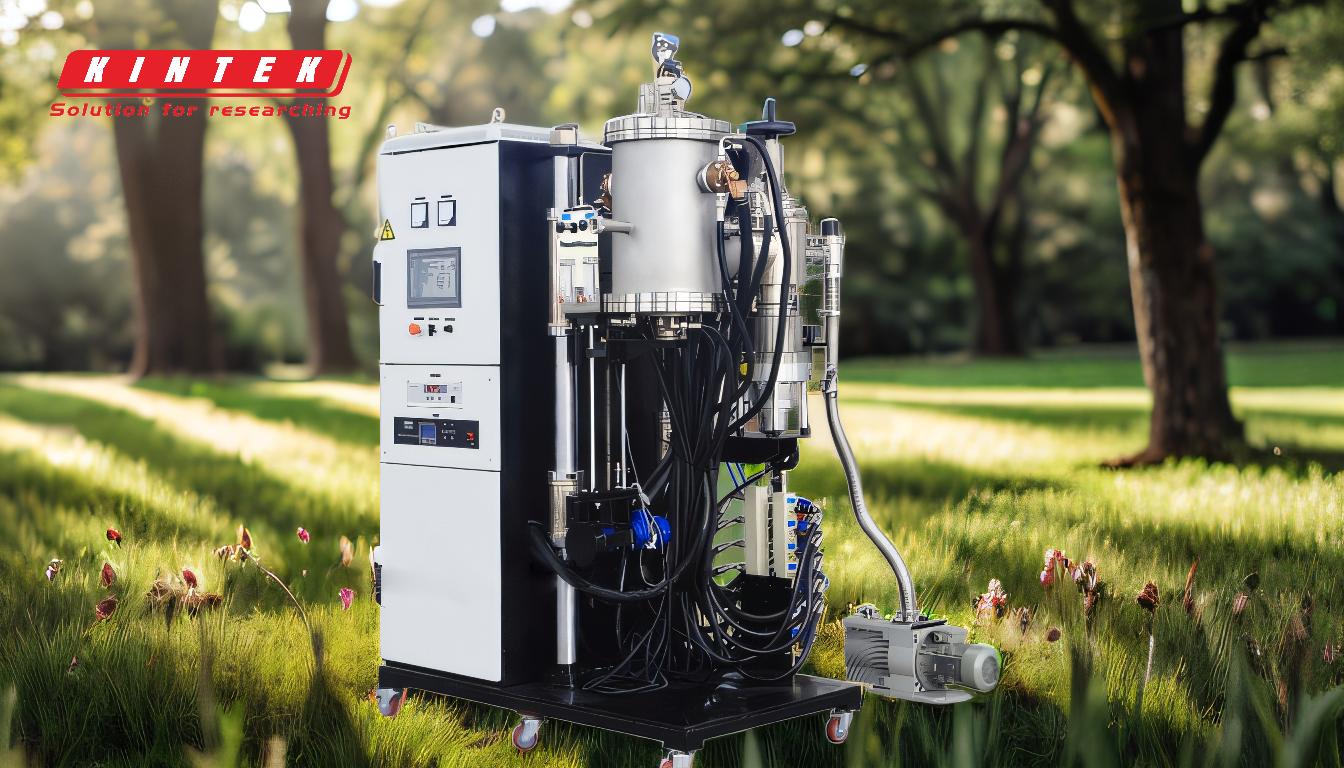
-
Definition and Purpose of Sintering:
- Sintering is a thermal process that bonds powdered materials into a solid structure without melting.
- It is used to create dense, durable components with improved mechanical properties, such as strength and durability.
- The process is essential for achieving the desired material properties in ceramics, metals, and alloys.
-
Temperature Control:
- Sintering occurs below the melting point of the material to avoid liquefaction.
- Higher sintering temperatures can enhance properties like tensile strength, bending fatigue strength, and impact energy.
- The temperature must be carefully controlled to optimize densification and avoid defects.
-
Atmosphere and Environment:
- The sintering atmosphere (e.g., air, vacuum, argon, or nitrogen) significantly impacts the process.
- Vacuum or inert gas environments prevent oxidation and contamination, ensuring higher-quality results.
- The choice of atmosphere depends on the material and desired properties.
-
Pressure and Compaction:
- Applied pressure during sintering enhances particle rearrangement and reduces porosity.
- Higher pressures improve densification, leading to stronger and more durable materials.
- Pressure is often combined with temperature to achieve optimal results.
-
Particle Size and Composition:
- Smaller particle sizes promote better densification due to increased surface area and faster diffusion.
- Homogeneous compositions ensure uniform sintering behavior and consistent material properties.
- The choice of powder size and composition is critical for achieving the desired microstructure and performance.
-
Microstructural Changes:
- Sintering directly influences grain size, pore size, and grain boundary distribution.
- These microstructural changes determine the material's mechanical properties, such as strength, toughness, and durability.
- Controlling sintering parameters ensures the desired microstructure is achieved.
-
Process Parameters:
- Key parameters include sintering temperature, heating rate, cooling rate, pressure, and atmosphere.
- These parameters are tailored based on the material and the intended application.
- Optimal parameter selection is crucial for achieving the desired product properties.
-
Applications and Importance:
- Sintering is widely used in industries such as automotive, aerospace, and electronics to produce high-performance components.
- It enables the production of complex shapes and near-net-shape parts with minimal material waste.
- The process is essential for manufacturing materials with specific mechanical, thermal, or electrical properties.
-
Challenges and Considerations:
- Controlling the amount of liquid phase during sintering is critical to avoid defects.
- Factors like air volume, vacuum level, layer thickness, and machine speed must be carefully managed.
- Achieving a consistent sintering endpoint ensures uniform material properties.
By understanding these key points, equipment and consumable purchasers can make informed decisions about sintering processes, materials, and parameters to achieve the desired outcomes for their specific applications.
Summary Table:
Key Aspect | Description |
---|---|
Definition | Thermal process bonding powdered materials into solid structures without melting. |
Purpose | Creates dense, durable components with improved mechanical properties. |
Key Factors | Temperature, atmosphere, pressure, particle size, and composition. |
Microstructural Impact | Influences grain size, pore size, and grain boundary distribution. |
Applications | Widely used in automotive, aerospace, and electronics industries. |
Optimize your sintering process for superior results—contact our experts today!