Laser sintering, particularly selective laser sintering (SLS), is a versatile additive manufacturing technique that offers unique advantages and disadvantages. It is capable of producing highly complex and functional shapes, which are challenging to achieve with traditional sintering methods. However, it comes with significant costs, both in terms of equipment and materials, and requires skilled operators. On the other hand, alternative methods like powder metallurgy are more cost-effective for large-scale production but may result in non-uniform components. High-speed sintering has shown promise in improving density and strength but is not universally endorsed, indicating potential limitations.
Key Points Explained:
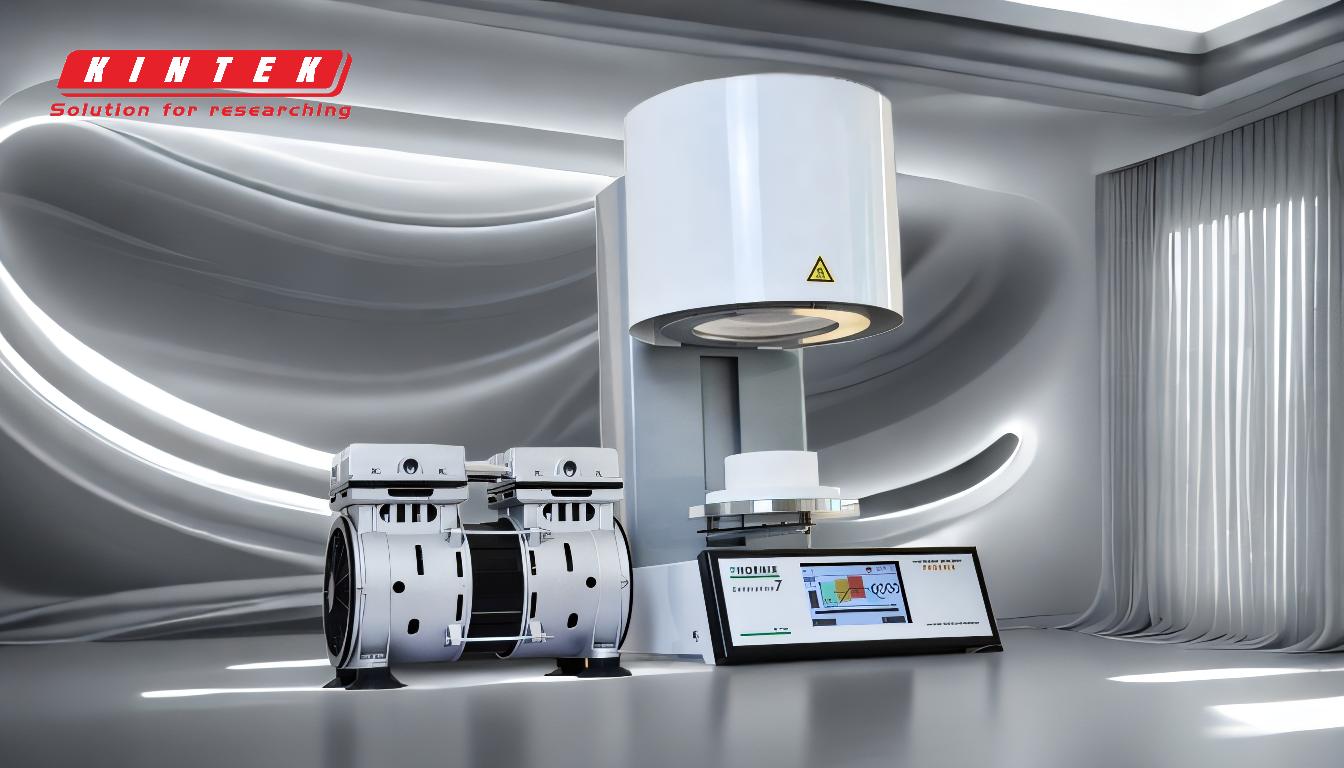
-
Advantages of Laser Sintering:
- Complex and Functional Shapes: Laser sintering, especially SLS, excels in creating intricate and functional geometries that are difficult or impossible to achieve with traditional sintering methods. This makes it ideal for applications requiring high precision and complexity, such as aerospace or medical devices.
- Material Versatility: SLS can work with a wide range of materials, including polymers, metals, and ceramics, allowing for diverse applications across industries.
- Minimal Post-Processing: Parts produced through SLS often require less post-processing compared to other additive manufacturing methods, as the process inherently produces near-net-shape components.
-
Disadvantages of Laser Sintering:
- High Costs: The initial investment for SLS machines is substantial, often exceeding $250,000. Additionally, the materials used in SLS are expensive, further increasing the overall cost.
- Skilled Operator Requirement: SLS requires operators with specialized skills and training, adding to the operational costs and complexity.
- Limited Scalability: While SLS is excellent for prototyping and small-scale production, it is less efficient for large-scale manufacturing compared to methods like powder metallurgy.
-
Comparison with Powder Metallurgy:
- Cost-Effectiveness: Powder metallurgy is generally more affordable, both in terms of equipment and materials, making it more suitable for large-scale production.
- Ease of Operation: Unlike SLS, powder metallurgy does not require highly skilled operators, reducing labor costs and training requirements.
- Uniformity Issues: One drawback of powder metallurgy is the potential for non-uniform components due to friction between the powder and tooling, which can affect the quality and consistency of the final product.
-
High-Speed Sintering:
- Improved Density and Strength: Some studies suggest that high-speed sintering can produce parts with slightly higher density and strength compared to traditional sintering methods.
- Limited Endorsement: Despite these benefits, not all material suppliers, particularly those dealing with zirconia, endorse high-speed sintering. This could be due to concerns about material compatibility, process stability, or other technical limitations.
-
Considerations for Equipment and Consumable Purchasers:
- Application Requirements: When deciding between SLS and other sintering methods, purchasers should consider the specific requirements of their application, such as the need for complex geometries, material properties, and production volume.
- Budget Constraints: The high costs associated with SLS may be a limiting factor for some organizations, especially those with limited budgets or those requiring large-scale production.
- Operator Expertise: The need for skilled operators should be factored into the decision-making process, as it can impact both the initial setup and ongoing operational costs.
- Material Compatibility: For those considering high-speed sintering, it is essential to verify material compatibility and consult with suppliers to ensure the method is suitable for the intended application.
In summary, laser sintering, particularly SLS, offers significant advantages in terms of design flexibility and material versatility but comes with high costs and operational complexities. Alternative methods like powder metallurgy are more cost-effective for large-scale production but may compromise on component uniformity. High-speed sintering shows potential for improved material properties but is not universally accepted, indicating the need for careful consideration of its limitations. Purchasers should weigh these factors against their specific needs and constraints to make an informed decision.
Summary Table:
Aspect | Laser Sintering (SLS) | Powder Metallurgy | High-Speed Sintering |
---|---|---|---|
Complex Shapes | Excels in creating intricate and functional geometries | Limited ability to produce complex shapes | Limited data available |
Material Versatility | Works with polymers, metals, and ceramics | Limited material options | Potential compatibility issues with materials like zirconia |
Cost | High initial investment (>$250,000) and expensive materials | More cost-effective for large-scale production | Costs vary; not universally endorsed |
Operator Skill | Requires highly skilled operators | Easier to operate; less skilled labor required | Requires specialized knowledge |
Scalability | Best for prototyping and small-scale production | Suitable for large-scale production | Limited scalability due to technical limitations |
Post-Processing | Minimal post-processing required | May require more post-processing | Minimal post-processing |
Component Uniformity | High precision and consistency | Potential for non-uniform components | Improved density and strength, but limited endorsement |
Need help choosing the right sintering method for your application? Contact our experts today for personalized advice!