The induction furnace is a crucial piece of equipment in metallurgical processes, primarily used for melting metals and alloys. The reactions occurring within an induction furnace are driven by electromagnetic induction, which generates heat within the metal itself. These reactions include the melting of metals, chemical reactions between the metal and impurities, and the formation of slag. The process is highly efficient due to the direct heating mechanism, which minimizes energy loss. The use of an IGBT induction furnace further enhances this efficiency by providing precise control over the heating process, making it ideal for applications requiring high purity and specific alloy compositions.
Key Points Explained:
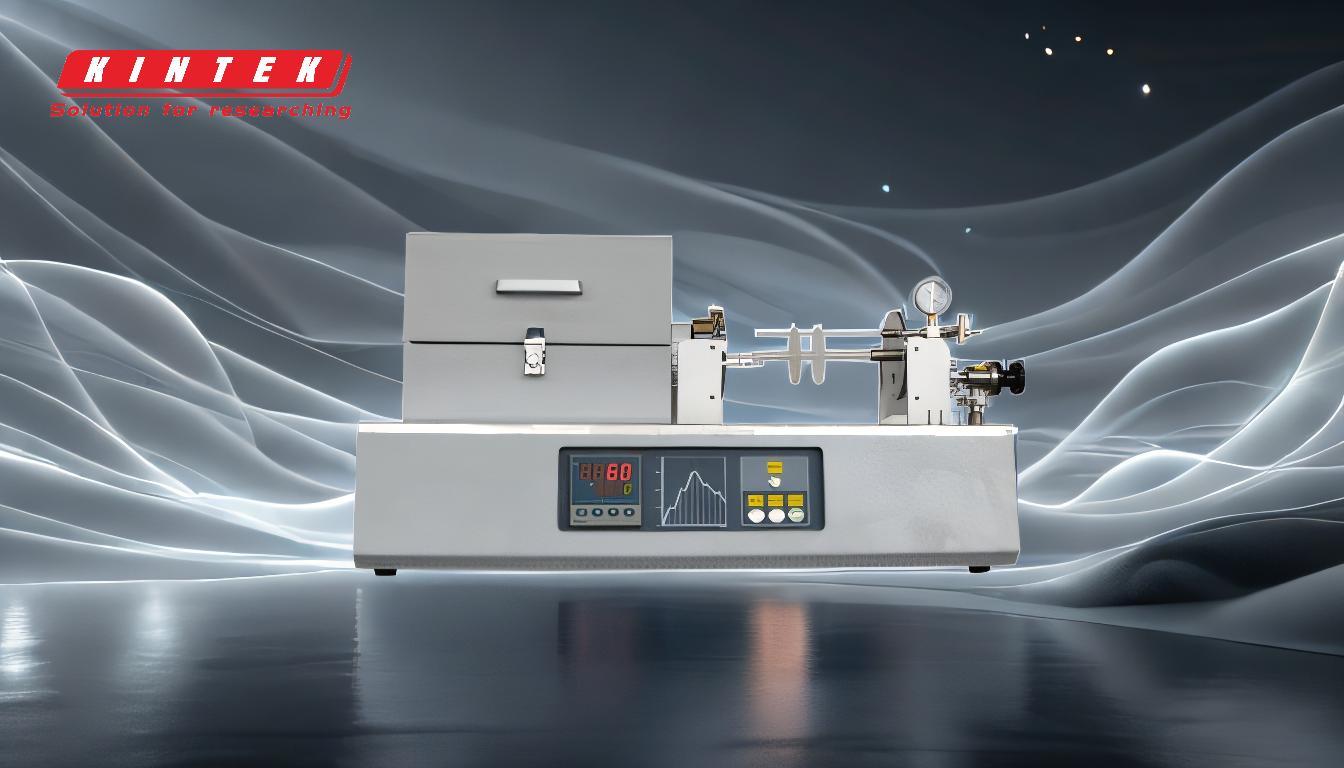
-
Electromagnetic Induction and Heating:
- The core principle behind an induction furnace is electromagnetic induction. An alternating current passes through a coil, creating a magnetic field. When a conductive metal is placed within this field, eddy currents are induced in the metal, generating heat due to electrical resistance.
- This method of heating is highly efficient as the heat is generated directly within the metal, reducing energy loss compared to traditional heating methods.
-
Melting of Metals:
- The primary reaction in an induction furnace is the melting of metals. The heat generated by the eddy currents raises the temperature of the metal above its melting point, causing it to transition from a solid to a liquid state.
- This process is particularly useful for melting metals like steel, iron, copper, and aluminum, as well as various alloys.
-
Chemical Reactions and Impurity Removal:
- During the melting process, chemical reactions occur between the metal and any impurities present. These reactions can include oxidation, where oxygen reacts with impurities to form oxides, which can then be removed as slag.
- The induction furnace environment can be controlled to promote specific chemical reactions, such as the reduction of oxides or the removal of sulfur and phosphorus.
-
Formation of Slag:
- Slag is a byproduct of the melting process, consisting of impurities that have been oxidized and separated from the metal. The slag floats on the surface of the molten metal and can be easily removed.
- The composition of the slag can be adjusted by adding fluxes, which help in the removal of specific impurities and improve the quality of the final metal product.
-
Role of the IGBT Induction Furnace:
- The IGBT induction furnace plays a critical role in modern induction heating due to its ability to provide precise control over the heating process. IGBT (Insulated Gate Bipolar Transistor) technology allows for efficient power conversion and control, enabling fine-tuning of the temperature and heating rate.
- This precision is essential for applications requiring high purity metals or specific alloy compositions, as it minimizes the risk of overheating or underheating, which can affect the final product's properties.
-
Advantages of Induction Furnaces:
- Induction furnaces offer several advantages, including high energy efficiency, precise temperature control, and the ability to melt metals quickly and uniformly.
- They are also environmentally friendly, as they produce fewer emissions compared to traditional furnaces, and the process can be easily automated, reducing labor costs.
-
Applications of Induction Furnaces:
- Induction furnaces are widely used in various industries, including steel production, foundries, and metal recycling. They are particularly valuable in applications where high-quality metals and alloys are required, such as in the aerospace and automotive industries.
- The ability to control the melting process precisely makes induction furnaces ideal for producing specialty alloys and high-performance materials.
In summary, the reactions in an induction furnace are driven by electromagnetic induction, leading to the melting of metals, chemical reactions for impurity removal, and the formation of slag. The use of an IGBT induction furnace enhances the efficiency and precision of these reactions, making it a vital tool in modern metallurgical processes.
Summary Table:
Key Reactions | Description |
---|---|
Electromagnetic Induction | Generates heat within the metal via eddy currents, ensuring efficient heating. |
Melting of Metals | Raises metal temperature above melting point, transitioning it to liquid state. |
Chemical Reactions | Removes impurities through oxidation and reduction processes. |
Formation of Slag | Byproduct of impurity removal, easily separated from molten metal. |
Role of IGBT Induction Furnace | Enhances precision and efficiency in heating for high-quality metal production. |
Learn how an induction furnace can optimize your metallurgical processes—contact our experts today!