Brazing is a widely used joining process that involves heating a filler metal above its melting point and distributing it between two or more close-fitting parts by capillary action. While brazing is generally considered a safe process when proper precautions are taken, it does involve high temperatures, potentially hazardous materials, and specific equipment that can pose risks if not handled correctly. To ensure safety during brazing, it is essential to follow a set of precautions that address personal protection, equipment handling, environmental safety, and proper material usage. These precautions help prevent accidents, injuries, and long-term health risks.
Key Points Explained:
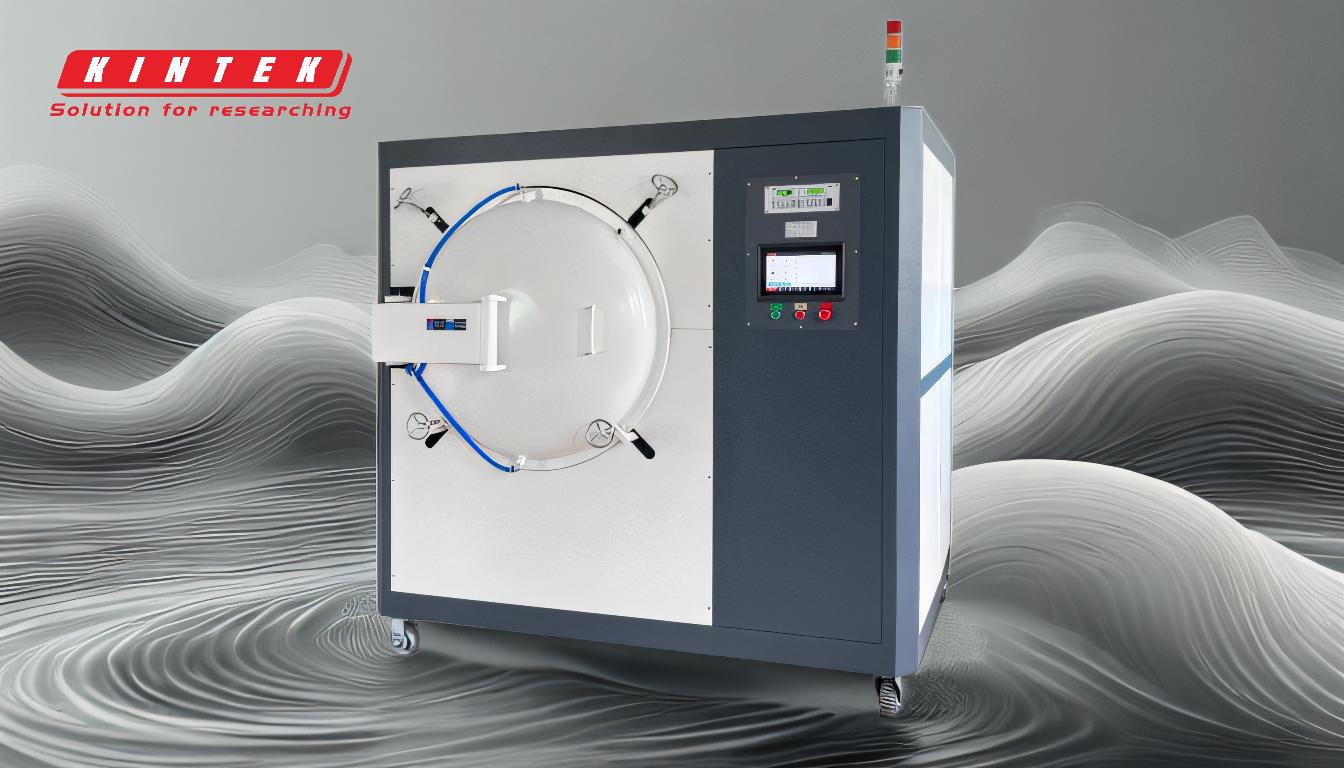
-
Personal Protective Equipment (PPE):
- Eye Protection: Always wear safety goggles or a face shield to protect your eyes from sparks, splashes of molten metal, and harmful UV radiation emitted during the brazing process. Specialized welding helmets with appropriate filters may also be necessary depending on the intensity of the heat source.
- Heat-Resistant Gloves: Use gloves made from materials like leather or Kevlar to protect your hands from burns caused by hot metal or accidental contact with the heat source.
- Protective Clothing: Wear flame-resistant clothing, such as a welding jacket or apron, to shield your skin from sparks and molten metal. Avoid synthetic materials that can melt and stick to the skin.
- Respiratory Protection: In environments where fumes or gases are generated, use a respirator or mask designed to filter out harmful particles. This is especially important when brazing materials that release toxic fumes, such as cadmium or zinc.
-
Proper Ventilation:
- Ensure that the workspace is well-ventilated to prevent the accumulation of harmful fumes and gases. Use local exhaust ventilation systems, such as fume extractors, to capture and remove contaminants at the source.
- If working in an enclosed area, consider using a forced-air ventilation system to maintain a constant flow of fresh air.
-
Handling of Brazing Materials:
- Filler Metals: Choose filler metals that are appropriate for the base materials being joined. Avoid using filler metals that contain toxic elements like cadmium unless absolutely necessary, and ensure proper handling and disposal.
- Fluxes: Fluxes are used to clean the metal surfaces and promote the flow of the filler metal. However, some fluxes can release harmful fumes when heated. Use fluxes in well-ventilated areas and follow the manufacturer’s safety guidelines.
- Base Materials: Be aware of the properties of the base materials being brazed. Some metals, such as galvanized steel, can release toxic fumes when heated. Take extra precautions when working with such materials.
-
Equipment Safety:
- Heat Sources: Whether using a torch, furnace, or induction heater, ensure that the heat source is in good working condition. Regularly inspect hoses, regulators, and connections for leaks or damage.
- Fire Safety: Keep a fire extinguisher rated for Class D fires (metal fires) nearby, as brazing involves high temperatures that can ignite flammable materials. Remove any combustible materials from the work area.
- Electrical Safety: If using electrically powered equipment, ensure that all electrical connections are secure and that the equipment is properly grounded to prevent electrical shocks.
-
Work Area Preparation:
- Cleanliness: Keep the work area clean and free of clutter to minimize the risk of accidents. Remove any oil, grease, or other contaminants that could ignite when exposed to high temperatures.
- Barriers and Signage: Use barriers or screens to protect bystanders from sparks and UV radiation. Clearly mark the work area with warning signs to alert others of the hazards present.
-
Training and Awareness:
- Ensure that all personnel involved in brazing operations are properly trained in the safe use of equipment and materials. Familiarize yourself with the Material Safety Data Sheets (MSDS) for all chemicals and materials used in the process.
- Stay informed about the specific hazards associated with the materials and equipment you are using, and follow all safety protocols and guidelines.
-
Emergency Preparedness:
- Have a first aid kit readily available in case of minor burns or injuries. Know the location of emergency exits and fire extinguishers.
- In case of exposure to harmful fumes or gases, move to a well-ventilated area immediately and seek medical attention if necessary.
By adhering to these safety precautions, you can significantly reduce the risks associated with brazing and create a safer working environment for yourself and others. Always prioritize safety and remain vigilant throughout the brazing process.
Summary Table:
Category | Key Precautions |
---|---|
Personal Protection | Wear safety goggles, heat-resistant gloves, flame-resistant clothing, and respirators. |
Ventilation | Ensure proper airflow with fume extractors or forced-air systems to remove harmful fumes. |
Material Handling | Use appropriate filler metals and fluxes; avoid toxic materials like cadmium. |
Equipment Safety | Inspect heat sources, keep fire extinguishers nearby, and ensure electrical safety. |
Work Area Preparation | Maintain cleanliness, use barriers, and mark hazards with warning signs. |
Training | Train personnel on equipment use and safety protocols; review MSDS for materials. |
Emergency Preparedness | Keep a first aid kit, know emergency exits, and seek medical help for fume exposure. |
Ensure your brazing process is safe and efficient—contact our experts today for personalized advice!