Physical Vapor Deposition (PVD) is a sophisticated process used to deposit thin films of material onto a substrate. It involves converting a solid precursor material into a vapor phase, transporting the vapor to the substrate, and then condensing it to form a thin film. This process is carried out in a vacuum or low-pressure environment to prevent contamination and ensure precise control over film properties. The key steps include material vaporization, vapor transport, and film condensation, with additional steps like substrate preparation and post-deposition treatment to optimize the final product.
Key Points Explained:
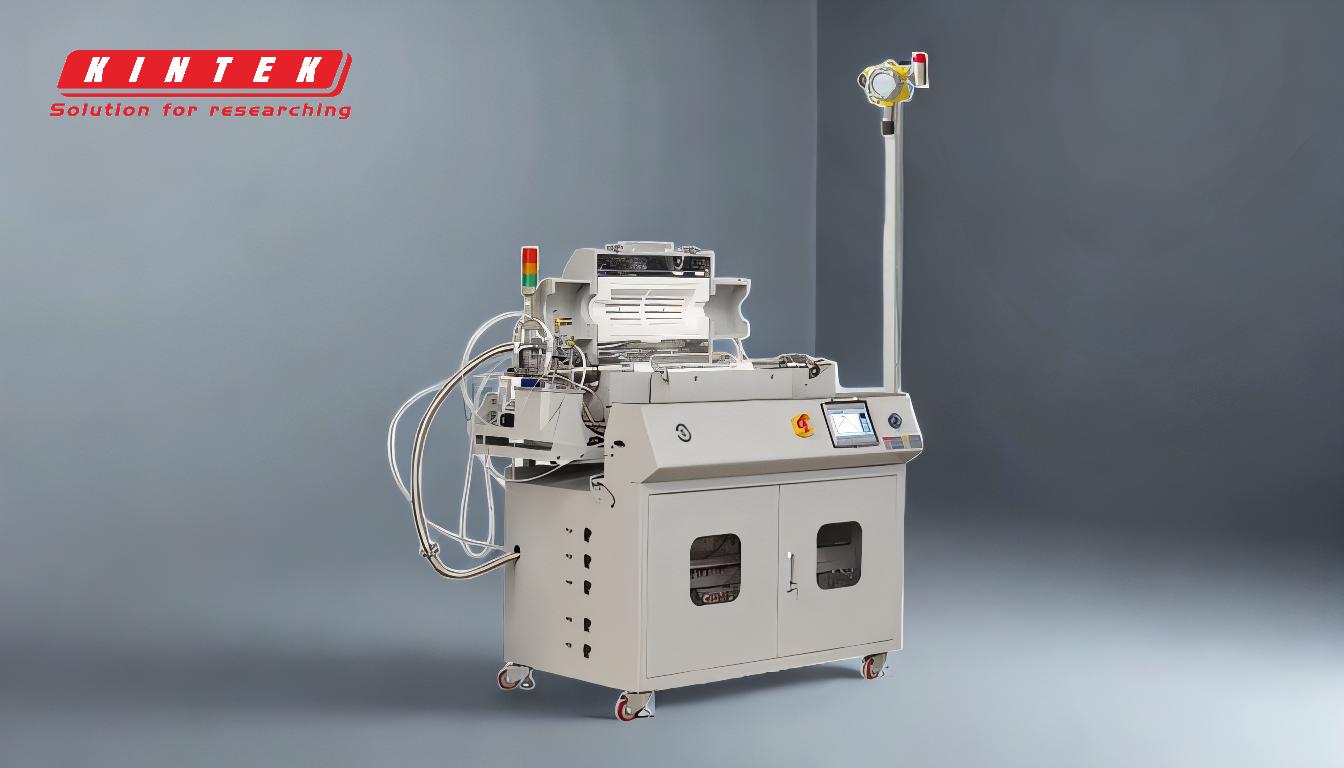
-
Material Vaporization:
- Process: The solid precursor material is converted into a vapor phase using physical means such as sputtering or evaporation. Sputtering involves bombarding the target material with high-energy ions, causing atoms to be ejected from the surface. Evaporation involves heating the material until it vaporizes.
- Purpose: This step is crucial for creating the vapor that will later condense on the substrate to form the thin film.
-
Vapor Transport:
- Process: The vaporized atoms or molecules are transported across a low-pressure region to the substrate. This is typically done in a vacuum chamber to minimize collisions with other particles and ensure a direct path to the substrate.
- Purpose: Ensures that the vaporized material reaches the substrate without contamination or loss, which is essential for achieving a uniform and high-quality film.
-
Film Condensation:
- Process: The vapor condenses on the substrate surface, forming a thin film. This occurs as the vaporized atoms lose energy and adhere to the substrate.
- Purpose: The condensation step is critical for the formation of the thin film, with the properties of the film (such as thickness and uniformity) being controlled by the rate of condensation and the conditions within the chamber.
-
Substrate Preparation:
- Process: Before deposition, the substrate must be cleaned and sometimes pre-treated to ensure proper adhesion of the film. This may involve chemical cleaning, ion bombardment, or heating.
- Purpose: Proper substrate preparation is essential for achieving strong adhesion and a high-quality film. Contaminants or improper surface conditions can lead to defects or poor film performance.
-
Post-Deposition Treatment:
- Process: After the film is deposited, it may undergo additional treatments such as annealing, oxidation, or nitridation to enhance its properties. These treatments can improve hardness, adhesion, or other functional characteristics.
- Purpose: Post-deposition treatments are used to optimize the film's properties for specific applications, ensuring that it meets the required performance standards.
-
Control and Monitoring:
- Process: Throughout the PVD process, various parameters such as temperature, pressure, and deposition rate are closely monitored and controlled. Tools like quartz crystal rate monitors are used to manage the thickness and rate of the film deposition.
- Purpose: Precise control and monitoring are essential for achieving the desired film properties and ensuring consistency in the deposition process.
-
Vacuum Environment:
- Process: The entire PVD process is carried out in a vacuum or low-pressure environment to minimize contamination and ensure a clean deposition process. The chamber is pumped down to lower levels to decrease background gases that could chemically react with the film.
- Purpose: A vacuum environment is critical for preventing contamination and ensuring that the vaporized material can travel directly to the substrate without interference.
By following these steps, the PVD process can produce high-quality thin films with precise control over their properties, making it a valuable technique in various industries, including electronics, optics, and coatings.
Summary Table:
Step | Process | Purpose |
---|---|---|
Material Vaporization | Solid precursor is converted into vapor via sputtering or evaporation. | Creates vapor for thin film formation. |
Vapor Transport | Vaporized atoms are transported in a vacuum to the substrate. | Ensures contamination-free, uniform deposition. |
Film Condensation | Vapor condenses on the substrate to form a thin film. | Controls film thickness and uniformity. |
Substrate Preparation | Substrate is cleaned and pre-treated for adhesion. | Ensures strong film adhesion and quality. |
Post-Deposition | Film undergoes treatments like annealing or oxidation. | Enhances film properties for specific applications. |
Control & Monitoring | Parameters like temperature and pressure are closely monitored. | Ensures precise control over film properties. |
Vacuum Environment | Process occurs in a vacuum to prevent contamination. | Maintains a clean, interference-free deposition environment. |
Discover how PVD can elevate your thin film applications—contact our experts today!