The Chemical Vapor Deposition (CVD) process is a widely used technique for depositing thin films onto substrates through chemical reactions of gaseous precursors. It involves several critical steps, including the introduction of precursor gases into a reaction chamber, their decomposition or reaction on the substrate surface, and the subsequent formation of a solid film. Key factors such as temperature, pressure, and gas flow rates significantly influence the quality and characteristics of the deposited material. The process can be performed under various conditions, including atmospheric or low pressure, and is essential for applications like semiconductor manufacturing, protective coatings, and graphene synthesis.
Key Points Explained:
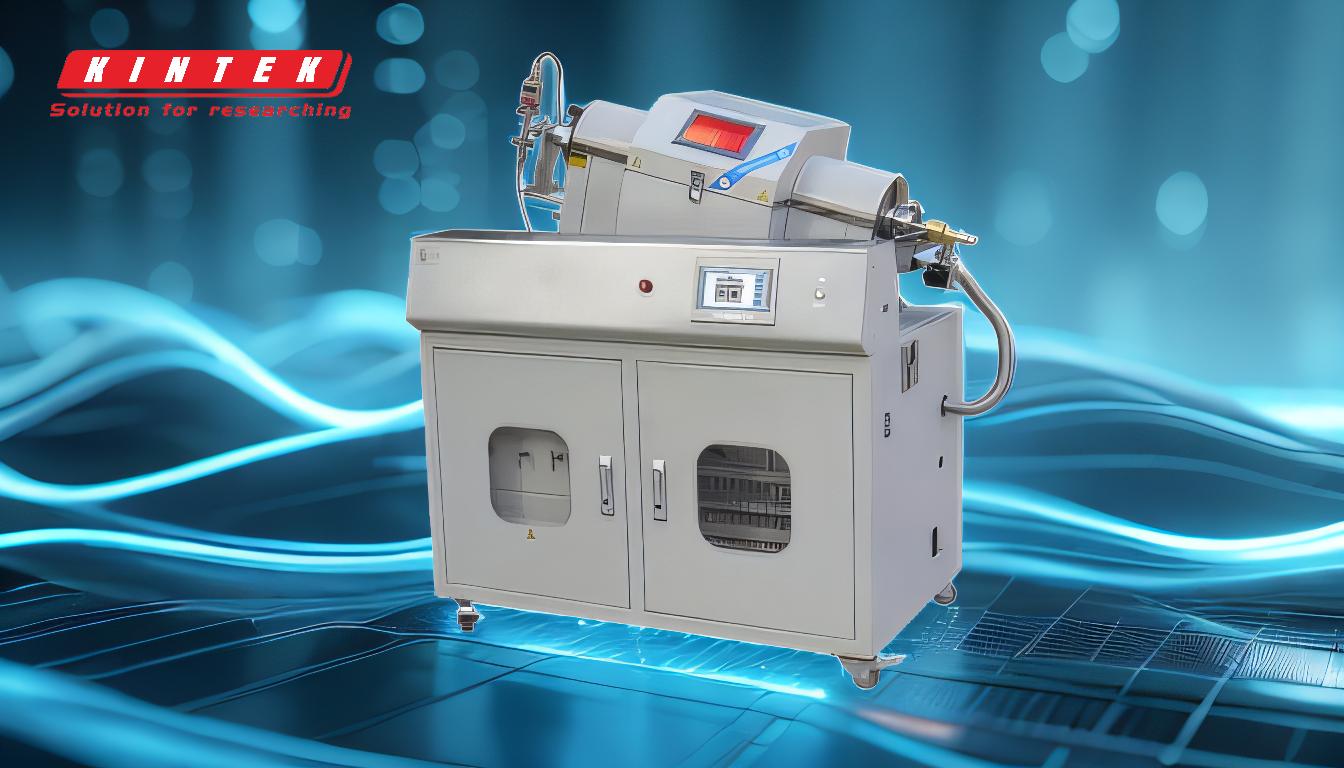
-
Introduction of Precursor Gases:
- The CVD process begins with the introduction of gaseous reactants into a reaction chamber. These precursors are typically volatile compounds that can be easily vaporized and transported to the substrate surface.
- The choice of precursor gases depends on the desired material to be deposited. For example, carbon-bearing gases like methane are used for graphene growth, while silicon-containing gases like silane are used for silicon-based thin films.
-
Transport of Reactants to the Substrate:
- Once inside the chamber, the precursor gases diffuse and flow toward the substrate. This step involves heat conduction and mass transfer, ensuring that the reactants reach the substrate uniformly.
- The flow rates of the gases and the pressure inside the chamber are carefully controlled to optimize the deposition process.
-
Chemical Reactions on the Substrate Surface:
- When the gases contact the heated substrate, chemical reactions occur, leading to the decomposition or reaction of the precursors. These reactions can be homogeneous (occurring in the gas phase) or heterogeneous (occurring on the substrate surface).
- For example, in graphene synthesis, carbon-bearing gases react at high temperatures in the presence of a metal catalyst, which facilitates the decomposition of the carbon species and the nucleation of the graphene lattice.
-
Deposition of Thin Film:
- The products of the chemical reactions form a solid thin film on the substrate surface. This deposition occurs through processes like chemisorption and surface diffusion.
- The structure and morphology of the deposited film are influenced by parameters such as temperature, pressure, and the nature of the substrate.
-
Surface Reactions and Film Growth:
- The CVD process involves three major surface reactions: kinetic, mass transfer, and desorption. These reactions determine the rate of film growth and the quality of the deposited material.
- Kinetic reactions involve the chemical transformation of reactants into products, while mass transfer ensures the continuous supply of reactants to the surface. Desorption removes any by-products or unreacted species from the surface.
-
Heat Transfer and By-Product Removal:
- After the deposition, heat is transferred away from the substrate, and any by-products or unreacted gases are removed from the reaction chamber through an exhausting system.
- This step ensures that the deposited film is free from contaminants and that the chamber is prepared for the next cycle.
-
Variations in CVD Processes:
- CVD can be performed under different conditions, such as atmospheric pressure CVD (APCVD) or low-pressure CVD (LPCVD). The choice of process depends on the specific application and the desired film properties.
- For instance, plasma-enhanced CVD (PECVD) allows for lower temperature operations and is suitable for depositing films on temperature-sensitive substrates.
-
Applications of CVD:
- CVD is used in various industries, including semiconductor manufacturing, where it is employed to deposit protective layers, wiring films, and insulating films on silicon wafers.
- It is also crucial for the synthesis of advanced materials like graphene, which is grown on metallic surfaces and then transferred to other substrates for applications in electronics and energy storage.
By understanding these steps and the factors influencing the CVD process, manufacturers can optimize the deposition of thin films for specific applications, ensuring high-quality and consistent results.
Summary Table:
Step | Description |
---|---|
1. Introduction of Precursor Gases | Volatile gases are introduced into the reaction chamber for vaporization. |
2. Transport of Reactants | Gases diffuse and flow toward the substrate under controlled conditions. |
3. Chemical Reactions | Precursors decompose or react on the heated substrate surface. |
4. Deposition of Thin Film | Solid film forms through chemisorption and surface diffusion. |
5. Surface Reactions & Growth | Kinetic, mass transfer, and desorption reactions determine film quality. |
6. Heat Transfer & By-Product Removal | Heat is removed, and by-products are exhausted from the chamber. |
7. Variations in CVD Processes | Includes APCVD, LPCVD, and PECVD for different applications. |
8. Applications of CVD | Used in semiconductor manufacturing, graphene synthesis, and protective coatings. |
Ready to optimize your CVD process? Contact our experts today for tailored solutions!