Chemical vapor deposition (CVD) is a sophisticated process used to deposit thin films of material onto a substrate through chemical reactions in a controlled environment. The process involves several sequential steps, each critical to ensuring the successful formation of the desired material. These steps include the introduction of reactant gases, their transport and activation, surface reactions, and the removal of byproducts. The CVD process is highly dependent on factors such as temperature, pressure, and the type of reactants used. Below, the key steps of the CVD reaction are explained in detail, providing a comprehensive understanding of how the process works.
Key Points Explained:
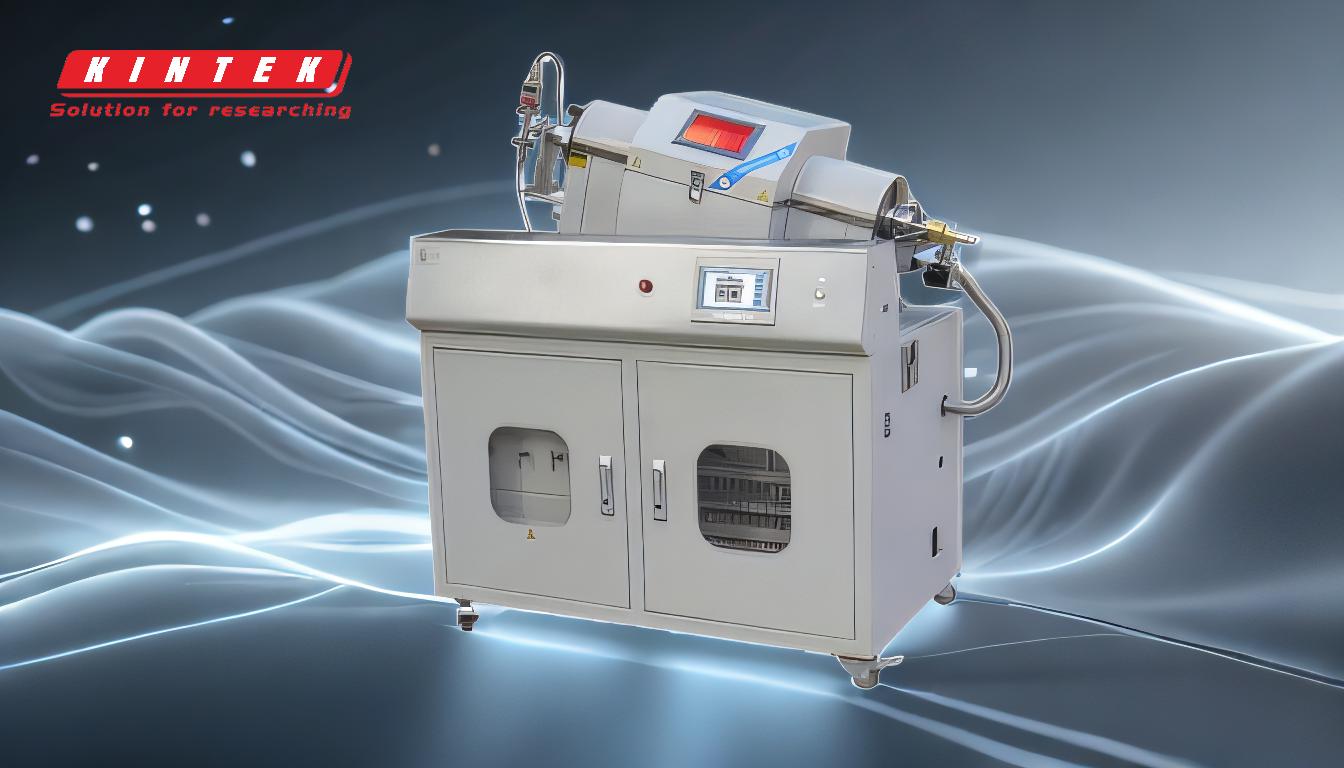
-
Introduction of Reactant Gases:
- The CVD process begins with the introduction of reactant gases into the reaction chamber. These gases typically include precursor chemicals that will undergo chemical reactions to form the desired material. Inert gases may also be introduced as diluents to control the reaction rate and ensure uniform deposition.
- The reactant gases are carefully selected based on the material to be deposited and the desired properties of the final film. For example, in the deposition of silicon dioxide, silane (SiH₄) and oxygen (O₂) are commonly used as precursors.
-
Transport of Reactant Gases to the Substrate:
- Once the reactant gases are introduced into the chamber, they must be transported to the substrate surface. This transport occurs through a combination of fluid dynamics and diffusion. The gases flow over the substrate, and the concentration gradient drives the diffusion of precursor molecules toward the surface.
- The efficiency of this step is influenced by factors such as the flow rate of the gases, the geometry of the reaction chamber, and the temperature and pressure conditions within the chamber.
-
Adsorption of Reactants on the Substrate Surface:
- As the precursor molecules reach the substrate surface, they are adsorbed onto it. Adsorption is the process by which molecules adhere to the surface, forming a thin layer that is ready to undergo chemical reactions.
- The adsorption process is influenced by the surface energy of the substrate, the temperature, and the chemical properties of the precursor molecules. Proper adsorption is crucial for ensuring uniform and high-quality film deposition.
-
Surface Reactions and Film Formation:
- Once adsorbed, the precursor molecules undergo chemical reactions on the substrate surface. These reactions can include decomposition, oxidation, reduction, or hydrolysis, depending on the specific precursors and desired material. For example, in the deposition of silicon nitride (Si₃N₄), ammonia (NH₃) and silane (SiH₄) react to form the nitride film.
- The surface reactions are typically facilitated by heat, plasma, or catalysts. The reaction conditions must be carefully controlled to ensure the formation of a high-quality film with the desired properties.
-
Desorption and Removal of Byproducts:
- After the surface reactions occur, gaseous byproducts are formed. These byproducts must be desorbed from the substrate surface and removed from the reaction chamber to prevent contamination and make room for more precursor molecules.
- Desorption is the process by which the byproduct molecules detach from the surface and are carried away by the gas flow. Efficient removal of byproducts is essential for maintaining the purity and integrity of the deposited film.
-
Evacuation of Byproducts from the Chamber:
- The final step in the CVD process involves evacuating the byproducts from the reaction chamber. This is typically achieved using vacuum pumps, which maintain the low-pressure environment necessary for the CVD process.
- The evacuation process ensures that the reaction chamber remains clean and ready for subsequent deposition cycles. It also prevents the accumulation of byproducts that could interfere with the quality of the deposited film.
Summary of the CVD Reaction Steps:
- Step 1: Introduce reactant gases into the reaction chamber.
- Step 2: Transport the gases to the substrate surface via fluid dynamics and diffusion.
- Step 3: Adsorb the precursor molecules onto the substrate surface.
- Step 4: Facilitate surface reactions to form the desired material.
- Step 5: Desorb and remove gaseous byproducts from the surface.
- Step 6: Evacuate the byproducts from the reaction chamber.
Each of these steps is critical to the success of the CVD process, and careful control of parameters such as temperature, pressure, and gas flow rates is essential to achieve high-quality film deposition. The CVD process is widely used in industries such as semiconductor manufacturing, where precise and uniform thin films are required for the production of electronic devices.
Summary Table:
Step | Description |
---|---|
Step 1 | Introduce reactant gases into the reaction chamber. |
Step 2 | Transport gases to the substrate via fluid dynamics and diffusion. |
Step 3 | Adsorb precursor molecules onto the substrate surface. |
Step 4 | Facilitate surface reactions to form the desired material. |
Step 5 | Desorb and remove gaseous byproducts from the surface. |
Step 6 | Evacuate byproducts from the reaction chamber. |
Need help optimizing your CVD process? Contact our experts today for tailored solutions!