Physical Vapor Deposition (PVD) is a vacuum coating process used to produce thin films and coatings. It involves the physical transfer of material from a source to a substrate, typically through vaporization, transportation, and condensation. The process is widely used in industries such as electronics, optics, and tool manufacturing due to its ability to produce durable, high-quality coatings. Below, we break down the steps of PVD in detail, focusing on the key stages and their significance.
Key Points Explained:
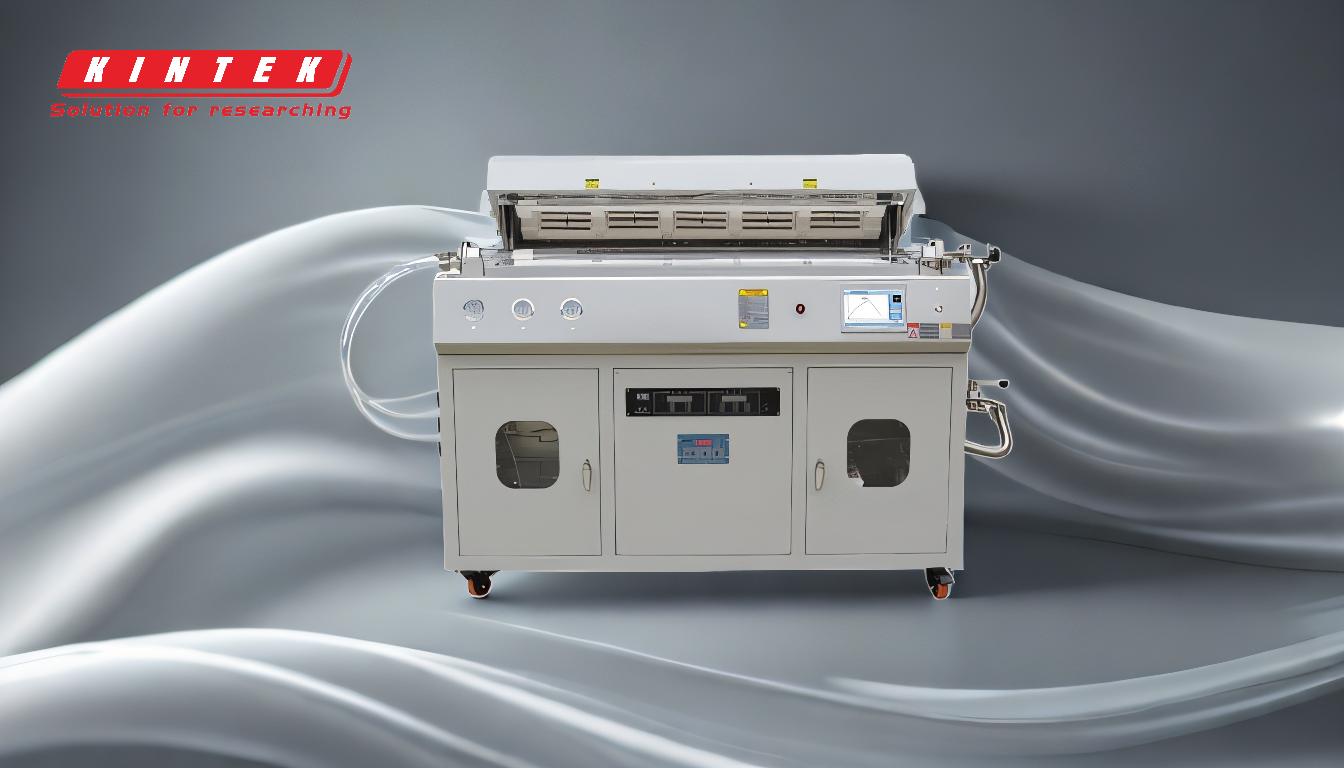
-
Material Vaporization
- The first step in PVD involves converting the material to be deposited into a vapor. This is typically achieved through methods such as sputtering, evaporation, or arc vaporization.
- In sputtering, high-energy ions bombard the target material, dislodging atoms and creating a vapor. In evaporation, the material is heated until it vaporizes.
- This step is critical because it determines the composition and quality of the vapor, which directly impacts the final coating.
-
Transportation of Vapor
- The vaporized material is transported from the source to the substrate in a vacuum or low-pressure environment.
- The vacuum ensures minimal interference from other gases, allowing the vapor to travel unimpeded and maintain its purity.
- This step is essential for achieving uniform deposition and controlling the thickness of the coating.
-
Reaction with Reactive Gases (Optional)
- In some PVD processes, a reactive gas (e.g., nitrogen or oxygen) is introduced into the chamber.
- The reactive gas interacts with the vaporized material to form a compound, such as a nitride or oxide, which is then deposited onto the substrate.
- This step is particularly important for creating hard, wear-resistant coatings like titanium nitride (TiN).
-
Condensation and Film Formation
- The vapor or compound condenses onto the substrate, forming a thin, adherent film.
- The substrate is often pre-treated (e.g., cleaned or heated) to enhance adhesion and film quality.
- This step determines the final properties of the coating, such as its hardness, durability, and optical characteristics.
-
Post-Deposition Treatments (Optional)
- After deposition, the coated substrate may undergo additional treatments, such as annealing or polishing, to improve the film's properties.
- These treatments can enhance adhesion, reduce stress, or modify the surface finish, depending on the application.
By following these steps, PVD enables the creation of high-performance coatings with precise control over thickness, composition, and properties. The process is versatile and can be tailored to meet specific application requirements, making it a cornerstone of modern surface engineering.
Summary Table:
Step | Description | Significance |
---|---|---|
1. Material Vaporization | Converts material into vapor via sputtering, evaporation, or arc vaporization. | Determines vapor composition and quality, impacting the final coating. |
2. Transportation of Vapor | Vapor travels to the substrate in a vacuum or low-pressure environment. | Ensures uniform deposition and precise control over coating thickness. |
3. Reaction with Reactive Gases (Optional) | Reactive gases (e.g., nitrogen) interact with vapor to form compounds. | Creates hard, wear-resistant coatings like titanium nitride (TiN). |
4. Condensation and Film Formation | Vapor condenses onto the substrate, forming a thin, adherent film. | Determines coating properties like hardness, durability, and optical traits. |
5. Post-Deposition Treatments (Optional) | Additional treatments (e.g., annealing) improve film properties. | Enhances adhesion, reduces stress, or modifies surface finish for applications. |
Discover how PVD can elevate your coating process—contact our experts today for tailored solutions!