Surface protection techniques are essential for enhancing the durability, performance, and appearance of materials, especially in industries like manufacturing, construction, and automotive. These techniques involve applying coatings, treatments, or modifications to surfaces to protect them from corrosion, wear, abrasion, and environmental damage. Common methods include painting, galvanizing, anodizing, and thermal spraying. Each technique has unique advantages and is chosen based on the material, application, and environmental conditions. Understanding these methods helps in selecting the most appropriate protection strategy for specific needs, ensuring longevity and cost-effectiveness.
Key Points Explained:
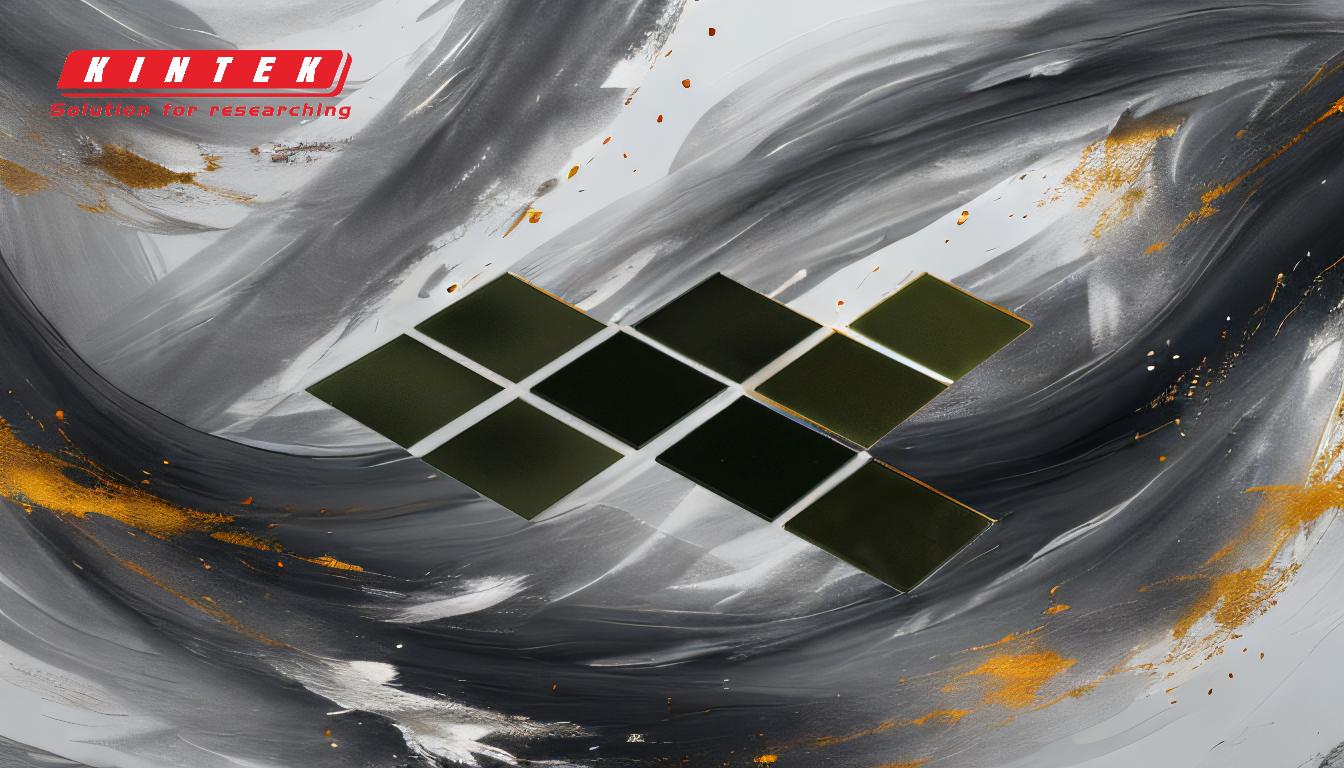
-
Painting and Coating
- Painting is one of the most common and cost-effective surface protection techniques. It involves applying a layer of paint or coating to the surface, which acts as a barrier against moisture, chemicals, and UV radiation.
- Types of coatings include:
- Epoxy coatings: Known for their chemical resistance and durability.
- Polyurethane coatings: Offer excellent UV resistance and flexibility.
- Powder coatings: Applied electrostatically and cured under heat, providing a durable and uniform finish.
- Applications: Used in automotive, construction, and marine industries to protect metals, wood, and concrete.
-
Galvanizing
- Galvanizing involves coating steel or iron with a layer of zinc to prevent rusting. This is typically done through hot-dip galvanizing, where the metal is submerged in molten zinc.
- Advantages:
- Provides long-lasting protection, even in harsh environments.
- Zinc acts as a sacrificial anode, corroding before the base metal.
- Applications: Widely used in construction (e.g., steel beams, pipelines) and outdoor structures.
-
Anodizing
- Anodizing is an electrochemical process used primarily for aluminum. It creates a thick oxide layer on the surface, enhancing corrosion resistance and allowing for dyeing to achieve colored finishes.
- Advantages:
- Improves hardness and wear resistance.
- Offers aesthetic customization through color options.
- Applications: Commonly used in aerospace, automotive, and consumer electronics.
-
Thermal Spraying
- Thermal spraying involves spraying molten or semi-molten materials onto a surface to form a protective coating. Techniques include flame spraying, arc spraying, and plasma spraying.
- Materials used: Metals, ceramics, and polymers.
- Advantages:
- Provides excellent wear and corrosion resistance.
- Can be applied to complex geometries.
- Applications: Used in industries like oil and gas, power generation, and automotive for components exposed to extreme conditions.
-
Chemical Conversion Coatings
- These coatings are formed by chemically reacting the surface of a metal to create a protective layer. Examples include phosphating and chromating.
- Advantages:
- Enhances adhesion for subsequent coatings (e.g., paint).
- Improves corrosion resistance.
- Applications: Used in automotive and aerospace industries for pre-treatment before painting.
-
Electroplating
- Electroplating involves depositing a thin layer of metal (e.g., chromium, nickel, or zinc) onto a surface using an electric current.
- Advantages:
- Improves corrosion resistance and aesthetic appeal.
- Enhances surface hardness and wear resistance.
- Applications: Commonly used in automotive, electronics, and jewelry industries.
-
Passivation
- Passivation is a chemical treatment used primarily for stainless steel to remove free iron from the surface and form a protective oxide layer.
- Advantages:
- Enhances corrosion resistance.
- Maintains the material's appearance.
- Applications: Used in medical devices, food processing equipment, and marine applications.
-
Laser Cladding
- Laser cladding involves using a laser to melt and fuse a protective material onto a substrate. This technique is used to repair or enhance surfaces.
- Advantages:
- Provides high precision and minimal heat-affected zones.
- Improves wear and corrosion resistance.
- Applications: Used in aerospace, energy, and heavy machinery industries.
-
Ceramic Coatings
- Ceramic coatings are applied to surfaces to provide high-temperature resistance, hardness, and chemical inertness.
- Advantages:
- Excellent thermal and electrical insulation properties.
- Resistant to wear and abrasion.
- Applications: Used in aerospace, automotive, and industrial machinery.
-
Organic Coatings
- Organic coatings, such as varnishes and lacquers, are applied to surfaces to provide protection and aesthetic appeal.
- Advantages:
- Easy to apply and cost-effective.
- Can be customized for specific properties (e.g., UV resistance, flexibility).
- Applications: Used in woodworking, automotive, and consumer goods industries.
By understanding these surface protection techniques, purchasers can make informed decisions based on the specific requirements of their projects, ensuring optimal performance and longevity of materials.
Summary Table:
Technique | Key Advantages | Common Applications |
---|---|---|
Painting & Coating | Cost-effective, UV/chemical resistance | Automotive, construction, marine |
Galvanizing | Long-lasting, sacrificial zinc protection | Construction, outdoor structures |
Anodizing | Corrosion resistance, aesthetic options | Aerospace, automotive, electronics |
Thermal Spraying | Wear/corrosion resistance, complex shapes | Oil & gas, power generation, automotive |
Chemical Coatings | Adhesion enhancement, corrosion resistance | Automotive, aerospace |
Electroplating | Aesthetic appeal, wear resistance | Automotive, electronics, jewelry |
Passivation | Corrosion resistance, maintains appearance | Medical, food processing, marine |
Laser Cladding | Precision, wear/corrosion resistance | Aerospace, energy, heavy machinery |
Ceramic Coatings | High-temperature resistance, hardness | Aerospace, automotive, industrial |
Organic Coatings | Easy application, customizable properties | Woodworking, automotive, consumer goods |
Discover the best surface protection solution for your needs—contact our experts today!