Surface treatment methods in tribology are essential for enhancing the performance, durability, and functionality of materials exposed to friction, wear, and lubrication. These methods aim to modify the surface properties of materials to improve their resistance to wear, reduce friction, and enhance load-bearing capacity. Common techniques include mechanical treatments like shot peening, thermal treatments such as carburizing, chemical treatments like nitriding, and advanced methods such as physical vapor deposition (PVD) and chemical vapor deposition (CVD). Each method has unique advantages and applications depending on the material, operating conditions, and desired outcomes. Understanding these techniques helps in selecting the most appropriate treatment for specific tribological challenges.
Key Points Explained:
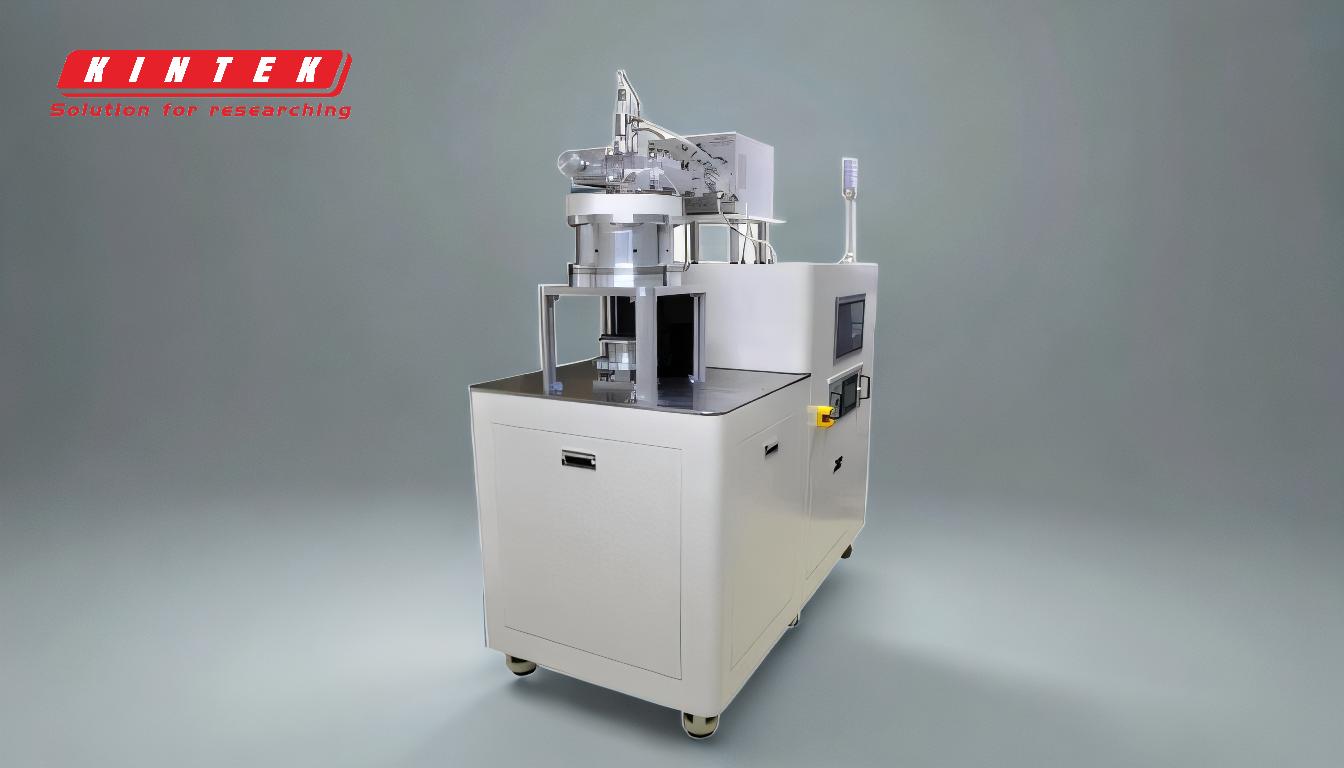
-
Mechanical Surface Treatments:
- Shot Peening: This process involves bombarding the surface with small spherical media to induce compressive residual stresses. It improves fatigue strength and resistance to stress corrosion cracking.
- Burnishing: A cold-working process where a hard tool is pressed against the surface to smooth and harden it, enhancing wear resistance.
- Grinding and Polishing: These techniques refine surface finish, reducing roughness and improving tribological performance by minimizing friction.
-
Thermal Surface Treatments:
- Carburizing: A heat treatment process that introduces carbon into the surface layer of low-carbon steel, creating a hard, wear-resistant surface while maintaining a tough core.
- Nitriding: Involves diffusing nitrogen into the surface of metals, typically steel, to form hard nitride compounds, improving hardness and wear resistance.
- Induction Hardening: A localized heat treatment that uses electromagnetic induction to heat the surface, followed by quenching to harden it.
-
Chemical Surface Treatments:
- Phosphating: Forms a phosphate coating on the surface, improving corrosion resistance and providing a good base for lubricants.
- Anodizing: Primarily used for aluminum, this electrochemical process creates a thick oxide layer, enhancing wear and corrosion resistance.
- Chromating: Applies a chromate conversion coating to improve corrosion resistance and adhesion for paints or primers.
-
Advanced Surface Coating Techniques:
- Physical Vapor Deposition (PVD): A vacuum-based process where materials are vaporized and deposited as thin films on the surface, providing excellent wear resistance and low friction.
- Chemical Vapor Deposition (CVD): Involves chemical reactions to deposit a solid material on the surface, offering high hardness and thermal stability.
- Thermal Spraying: A process where molten or semi-molten materials are sprayed onto the surface, forming a protective coating with enhanced wear and corrosion resistance.
-
Laser Surface Treatments:
- Laser Hardening: Uses a high-energy laser beam to heat the surface, followed by rapid cooling to create a hardened layer.
- Laser Cladding: Deposits a layer of material onto the surface using a laser, improving wear resistance and repairing damaged components.
-
Electrochemical and Electroless Plating:
- Electroplating: Deposits a metal coating on the surface through an electrochemical process, enhancing wear and corrosion resistance.
- Electroless Plating: A chemical process that deposits a uniform coating without external electrical power, often used for complex geometries.
-
Selection Criteria for Surface Treatments:
- Material Compatibility: The treatment must be compatible with the base material to avoid adverse effects.
- Operating Conditions: Factors like temperature, load, and environment dictate the choice of treatment.
- Cost and Feasibility: The treatment should be cost-effective and feasible for the application.
By understanding these surface treatment methods, engineers and material scientists can tailor solutions to specific tribological challenges, ensuring optimal performance and longevity of components.
Summary Table:
Category | Methods | Key Benefits |
---|---|---|
Mechanical Treatments | Shot Peening, Burnishing, Grinding & Polishing | Improves fatigue strength, wear resistance, and surface finish. |
Thermal Treatments | Carburizing, Nitriding, Induction Hardening | Enhances hardness, wear resistance, and load-bearing capacity. |
Chemical Treatments | Phosphating, Anodizing, Chromating | Improves corrosion resistance and adhesion for coatings. |
Advanced Coatings | PVD, CVD, Thermal Spraying | Provides excellent wear resistance, low friction, and thermal stability. |
Laser Treatments | Laser Hardening, Laser Cladding | Enhances wear resistance and repairs damaged components. |
Electrochemical Plating | Electroplating, Electroless Plating | Improves wear and corrosion resistance, suitable for complex geometries. |
Need help selecting the right surface treatment for your application? Contact our experts today!