The deposition rate in thermal deposition processes is influenced by a variety of system variables, including the delivery rate of the precursor, the temperatures of the vaporizer and substrate, the size of the erosion zone, and the target-substrate distance. These factors collectively determine the efficiency and uniformity of the deposition process. Understanding and optimizing these variables is crucial for achieving the desired film characteristics and ensuring high-quality deposition.
Key Points Explained:
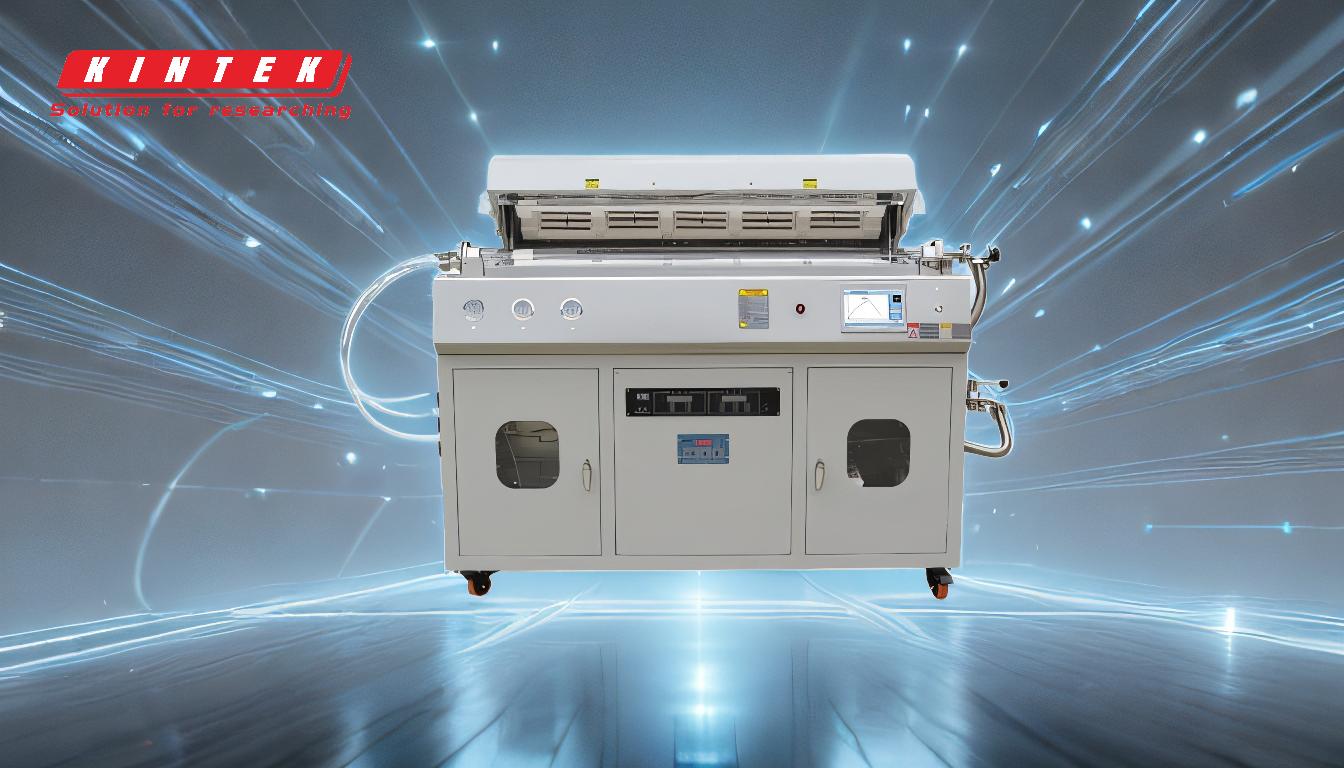
-
Delivery Rate of the Precursor:
- Explanation: The delivery rate of the precursor is a critical factor in thermal deposition. It determines the amount of material available for deposition at any given time. A higher delivery rate can lead to a higher deposition rate, but it must be carefully controlled to avoid issues such as incomplete reactions or uneven film thickness.
- Impact: Proper control of the precursor delivery rate ensures that the chemical reactions necessary for deposition occur at the desired rate, leading to consistent film quality.
-
Temperature of the Vaporizer and Substrate:
- Explanation: The temperatures of both the vaporizer and the substrate play a significant role in the deposition process. The vaporizer temperature affects the rate at which the precursor is vaporized, while the substrate temperature influences the rate of chemical reactions and the adhesion of the deposited material.
- Impact: Higher temperatures generally increase the deposition rate by enhancing the vaporization of the precursor and the reactivity of the substrate. However, excessively high temperatures can lead to unwanted side reactions or degradation of the substrate.
-
Size of the Erosion Zone:
- Explanation: The size of the erosion zone, which is the area on the target material that is being eroded by the deposition process, directly affects the deposition rate. A larger erosion zone typically results in a higher deposition rate.
- Impact: Increasing the size of the erosion zone can enhance the deposition rate, but it must be balanced with the need for uniform film thickness. A larger erosion zone can lead to non-uniform deposition if not properly managed.
-
Target-Substrate Distance:
- Explanation: The distance between the target material and the substrate is another critical variable. A shorter target-substrate distance generally increases the deposition rate by reducing the distance that the vaporized material must travel.
- Impact: Decreasing the target-substrate distance can lead to a higher deposition rate and improved thickness uniformity. However, it may also increase the risk of contamination or damage to the substrate if the distance is too small.
-
Power and Temperature:
- Explanation: The power applied to the deposition system and the overall temperature of the process also influence the deposition rate. Higher power levels and temperatures can increase the energy available for the deposition process, leading to a higher deposition rate.
- Impact: Increasing power and temperature can enhance the deposition rate, but it is important to monitor these parameters to avoid overheating or damaging the substrate or the deposition equipment.
-
Physical Properties of the Target Material:
- Explanation: The physical properties of the target material, such as its composition, density, and melting point, can affect the deposition rate. Different materials will have different rates of erosion and deposition.
- Impact: Understanding the physical properties of the target material is essential for optimizing the deposition process. Materials with lower melting points or higher densities may require different conditions to achieve the desired deposition rate.
-
Plasma Characteristics (if applicable):
- Explanation: In processes that involve plasma, the characteristics of the plasma, such as its temperature, composition, and density, can significantly influence the deposition rate. Monitoring these characteristics is crucial for maintaining the desired material composition and checking for contamination.
- Impact: Proper control of plasma characteristics ensures that the deposition process proceeds at the desired rate and that the resulting film has the correct composition and properties.
By carefully managing these system variables, it is possible to optimize the deposition rate and achieve high-quality films with the desired properties. Each variable must be considered in the context of the specific deposition process and the materials being used to ensure the best possible results.
Summary Table:
Variable | Impact on Deposition Rate |
---|---|
Precursor Delivery Rate | Higher rates increase deposition but require careful control to avoid uneven film thickness. |
Vaporizer Temperature | Higher temperatures enhance precursor vaporization and reactivity. |
Substrate Temperature | Influences reaction rates and material adhesion; excessive heat can degrade the substrate. |
Erosion Zone Size | Larger zones increase deposition but may lead to non-uniform films if not managed. |
Target-Substrate Distance | Shorter distances increase deposition rate and improve thickness uniformity. |
Power and Temperature | Higher levels increase energy for deposition but risk overheating the system. |
Target Material Properties | Materials with lower melting points or higher densities require specific conditions. |
Plasma Characteristics | Essential for maintaining material composition and avoiding contamination. |
Need help optimizing your thermal deposition process? Contact our experts today for tailored solutions!