The preparation of nano thin films involves advanced techniques that allow precise control over the thickness, composition, and properties of the films. The two primary techniques used for preparing nano thin films are Physical Vapor Deposition (PVD) and Chemical Vapor Deposition (CVD). PVD involves the physical transformation of a solid material into a vapor, which then condenses onto a substrate to form a thin film. CVD, on the other hand, relies on chemical reactions between gaseous precursors to deposit a solid film onto a substrate. Both methods are widely used in industries such as semiconductors, optics, and flexible electronics due to their ability to produce high-purity and high-performance films.
Key Points Explained:
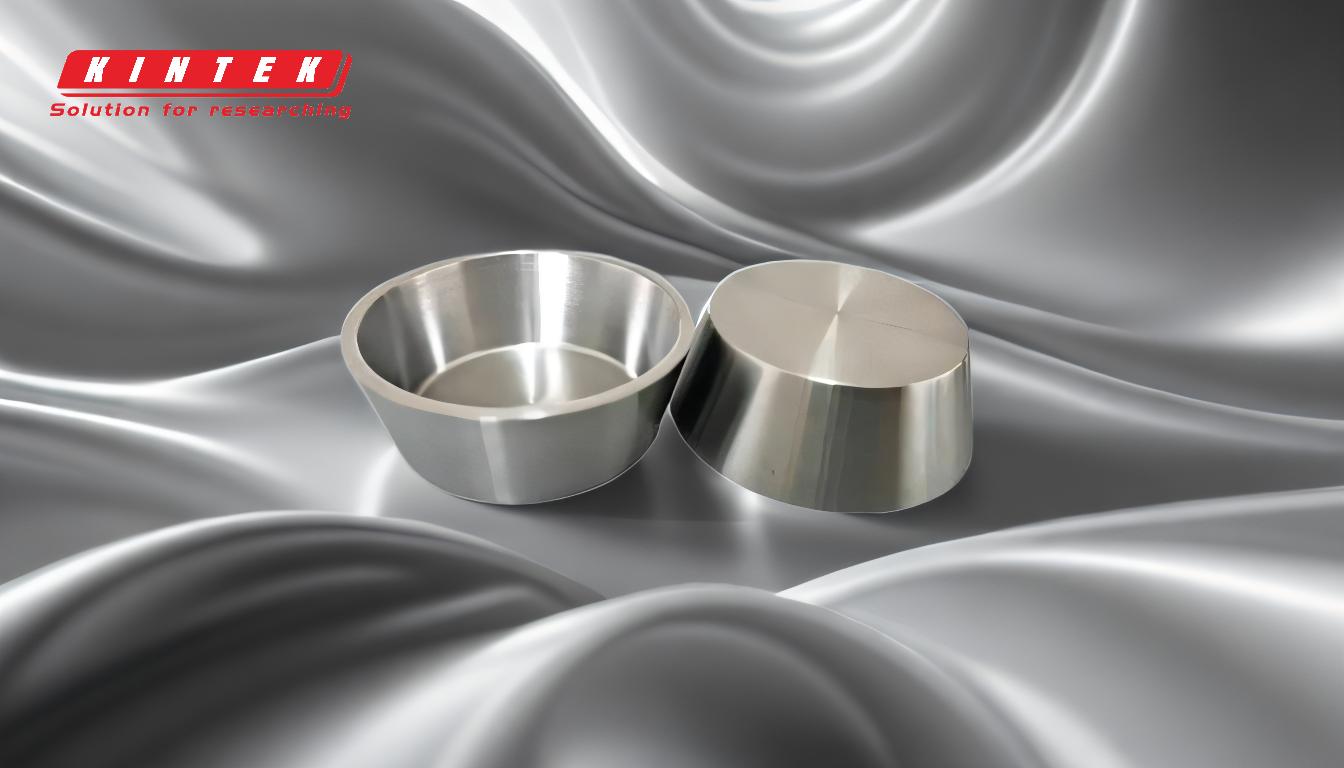
-
Physical Vapor Deposition (PVD):
- Definition: PVD is a process where a solid material is vaporized in a vacuum and then deposited onto a substrate to form a thin film. This method does not involve chemical reactions.
-
Process Steps:
- Vaporization: The source material (target) is vaporized using techniques such as sputtering, evaporation, or laser ablation.
- Transport: The vaporized atoms or molecules travel through the vacuum chamber.
- Deposition: The vapor condenses onto the substrate, forming a thin film.
-
Advantages:
- High purity of the deposited film.
- Excellent control over film thickness and uniformity.
- Suitable for a wide range of materials, including metals, alloys, and ceramics.
-
Applications:
- Semiconductor manufacturing (e.g., silicon wafers).
- Optical coatings (e.g., anti-reflective coatings).
- Wear-resistant coatings (e.g., tool coatings).
-
Chemical Vapor Deposition (CVD):
- Definition: CVD is a chemical process where volatile precursors react or decompose on a substrate surface to form a solid thin film.
-
Process Steps:
- Introduction of Precursors: Gaseous reactants (precursors) are introduced into a reaction chamber.
- Chemical Reaction: The precursors react or decompose on the substrate surface, forming a solid film.
- Byproduct Removal: Gaseous byproducts are removed from the chamber.
-
Advantages:
- High-quality, high-purity films with excellent conformality.
- Ability to deposit complex materials, including polymers and composites.
- Suitable for large-scale production.
-
Applications:
- Thin-film transistors in electronics.
- Protective coatings (e.g., diamond-like carbon coatings).
- Flexible electronics (e.g., OLEDs).
-
Comparison Between PVD and CVD:
-
Mechanism:
- PVD relies on physical processes (vaporization and condensation).
- CVD involves chemical reactions to form the film.
-
Environment:
- PVD requires a vacuum or ultrahigh vacuum environment.
- CVD can operate at atmospheric pressure or low vacuum, depending on the process.
-
Material Compatibility:
- PVD is ideal for metals, alloys, and ceramics.
- CVD is better suited for depositing complex materials, including polymers and composites.
-
Film Properties:
- PVD films tend to have higher density and better adhesion.
- CVD films offer superior conformality and uniformity, especially on complex geometries.
-
Mechanism:
-
Other Techniques for Thin Film Preparation:
- While PVD and CVD are the most common methods, other techniques include:
- Spin Coating: A liquid precursor is spread onto a substrate, which is then spun at high speed to create a uniform thin film.
- Electroplating: A substrate is immersed in an electrolyte solution, and an electric current is applied to deposit a metal film.
- Drop Casting: A solution containing the film material is dropped onto a substrate and allowed to dry, forming a thin film.
- Plasma Sputtering: A plasma is used to eject atoms from a target material, which then deposit onto a substrate.
- While PVD and CVD are the most common methods, other techniques include:
-
Choosing the Right Technique:
- The choice between PVD, CVD, or other methods depends on factors such as:
- The desired film material and properties.
- The substrate type and geometry.
- The required film thickness and uniformity.
- The production scale and cost considerations.
- The choice between PVD, CVD, or other methods depends on factors such as:
In summary, PVD and CVD are the two primary techniques for preparing nano thin films, each with its unique advantages and applications. PVD is ideal for high-purity, dense films, while CVD excels in producing uniform, conformal films for complex materials. Understanding these techniques helps in selecting the appropriate method for specific applications in industries such as electronics, optics, and coatings.
Summary Table:
Aspect | PVD | CVD |
---|---|---|
Mechanism | Physical transformation of solid to vapor, no chemical reactions | Chemical reactions between gaseous precursors |
Environment | Requires vacuum or ultrahigh vacuum | Operates at atmospheric pressure or low vacuum |
Material Compatibility | Metals, alloys, ceramics | Polymers, composites, complex materials |
Film Properties | High density, better adhesion | Superior conformality, uniformity on complex geometries |
Applications | Semiconductor manufacturing, optical coatings, wear-resistant coatings | Thin-film transistors, protective coatings, flexible electronics |
Need help selecting the right thin film preparation technique? Contact our experts today!