Induction heating is a process that uses electromagnetic induction and Joule heating to generate heat within a conductive material. The two main types of induction furnaces used for this purpose are coreless induction furnaces and channel induction furnaces. Coreless furnaces are characterized by a crucible surrounded by a water-cooled coil, making them versatile for melting a wide range of metals. Channel furnaces, on the other hand, utilize a loop of molten metal as a secondary winding around an iron core, making them more efficient for continuous melting processes. Both types are widely used in industrial applications due to their efficiency, precise temperature control, and minimal melt losses.
Key Points Explained:
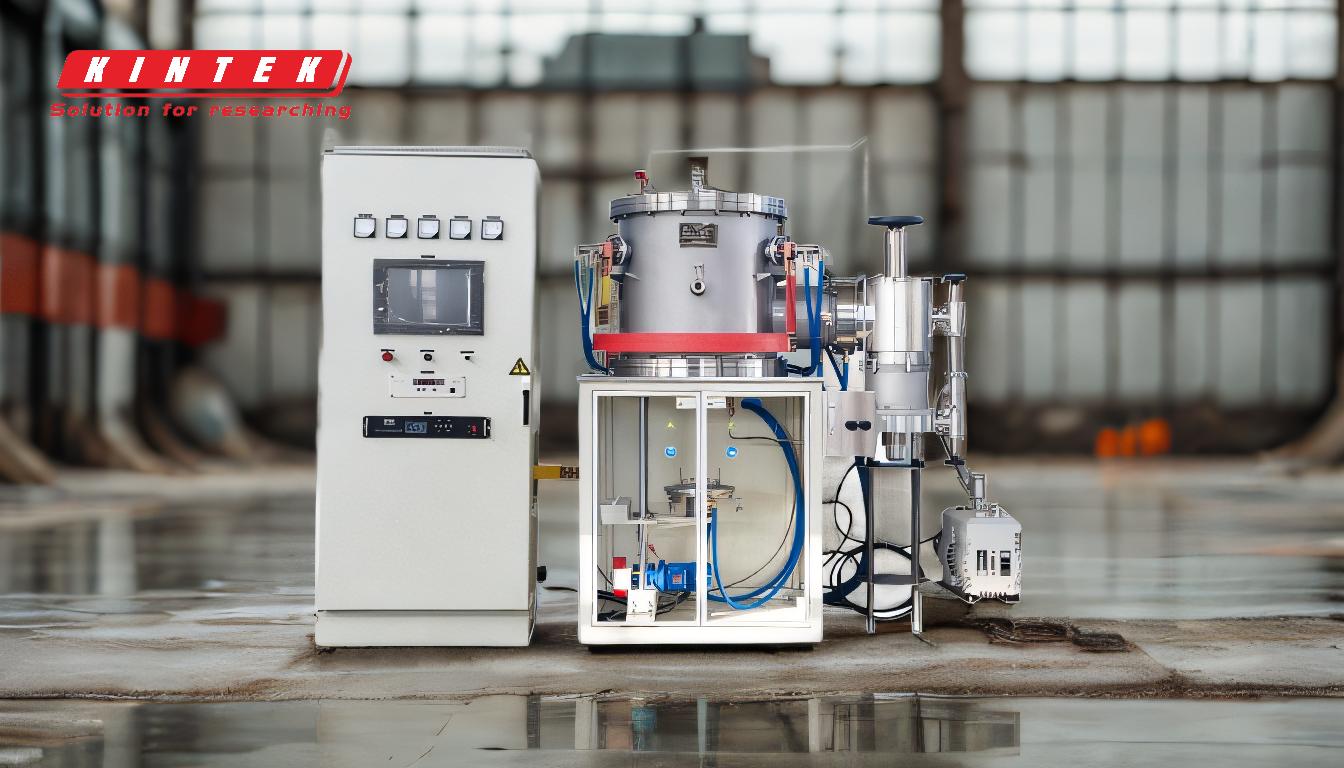
-
Coreless Induction Furnaces
-
Design and Operation:
- Coreless furnaces consist of a crucible (typically made of refractory material) surrounded by a water-cooled alternating current (AC) solenoid coil.
- When the coil is energized, it generates a magnetic field that induces eddy currents in the metal placed inside the crucible. These eddy currents produce heat through Joule heating, melting the metal.
-
Advantages:
- Versatile for melting a wide variety of metals, including ferrous and non-ferrous alloys.
- Suitable for batch melting and smaller-scale operations.
- Easy to clean and maintain due to the absence of a core.
-
Disadvantages:
- Less energy-efficient compared to channel furnaces for continuous operations.
- Limited refining capabilities, as the process primarily focuses on melting.
-
Design and Operation:
-
Channel Induction Furnaces
-
Design and Operation:
- Channel furnaces feature a loop of molten metal that acts as a single-turn secondary winding around an iron core.
- The primary coil, wrapped around the core, induces currents in the molten metal loop, generating heat through electromagnetic induction and Joule heating.
-
Advantages:
- Highly energy-efficient for continuous melting processes.
- Ideal for applications requiring consistent molten metal supply, such as in foundries.
- Lower operating costs due to reduced energy consumption.
-
Disadvantages:
- Limited flexibility in melting different types of metals compared to coreless furnaces.
- Requires a continuous supply of molten metal to maintain operation, making it less suitable for batch processes.
-
Design and Operation:
-
Comparison of Coreless and Channel Furnaces
-
Application Suitability:
- Coreless furnaces are better suited for batch operations and melting a variety of metals, while channel furnaces excel in continuous melting processes.
-
Energy Efficiency:
- Channel furnaces are more energy-efficient for continuous operations, whereas coreless furnaces may consume more energy for similar tasks.
-
Maintenance and Flexibility:
- Coreless furnaces are easier to clean and maintain, offering greater flexibility in metal types. Channel furnaces require more specialized maintenance due to their design but are more efficient for specific applications.
-
Application Suitability:
-
Industrial Applications
- Both coreless and channel induction furnaces are widely used in industries such as foundries, metal casting, and alloy production.
- Coreless furnaces are preferred for smaller-scale operations and when flexibility in metal types is required.
- Channel furnaces are commonly used in large-scale foundries and continuous casting processes.
-
Key Considerations for Purchasers
-
Production Requirements:
- Determine whether the operation requires batch or continuous melting to choose between coreless and channel furnaces.
-
Energy Efficiency:
- Evaluate energy consumption and operating costs, especially for long-term operations.
-
Metal Types:
- Consider the variety of metals to be melted, as coreless furnaces offer greater flexibility.
-
Maintenance and Operational Costs:
- Assess the ease of maintenance and potential downtime for each type of furnace.
-
Production Requirements:
In summary, the choice between coreless and channel induction furnaces depends on the specific industrial application, production scale, and operational requirements. Both types offer unique advantages and limitations, making them suitable for different scenarios in the metal melting and alloying industry.
Summary Table:
Feature | Coreless Induction Furnace | Channel Induction Furnace |
---|---|---|
Design | Crucible surrounded by a water-cooled coil | Loop of molten metal as a secondary winding around an iron core |
Operation | Batch melting, versatile for various metals | Continuous melting, ideal for consistent molten metal supply |
Advantages | Versatile, easy to clean, suitable for small-scale operations | Highly energy-efficient, lower operating costs, ideal for large-scale foundries |
Disadvantages | Less energy-efficient for continuous operations, limited refining capabilities | Limited flexibility in metal types, requires continuous molten metal supply |
Best For | Batch operations, melting a variety of metals | Continuous melting processes, large-scale industrial applications |
Need help choosing the right induction furnace for your needs? Contact our experts today!