Filter presses are essential equipment in the chemical industry for separating solids from liquids. They come in various types, each designed for specific applications and operational requirements. The most common types include plate and frame filter presses, recessed chamber filter presses, membrane filter presses, and lab filter presses. These systems vary in design, filtration efficiency, and suitability for different chemical processes. Understanding the differences between these types helps in selecting the right filter press for specific industrial needs, ensuring optimal performance and cost-effectiveness.
Key Points Explained:
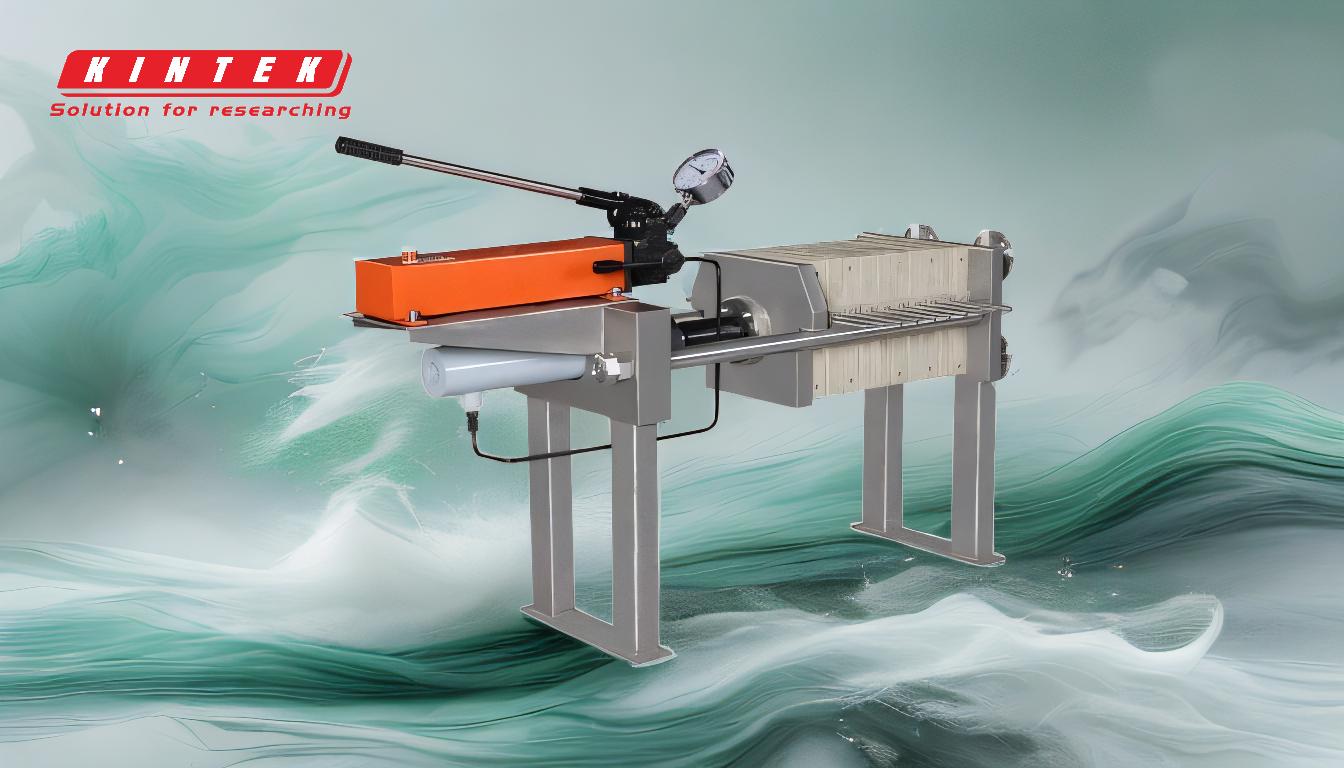
-
Plate and Frame Filter Press:
- This is one of the oldest and most widely used types of filter presses.
- It consists of alternating plates and frames, with filter cloths placed between them.
- The slurry is pumped into the press, and the solids are captured in the frames while the filtrate passes through the cloth.
- Ideal for applications requiring high filtration efficiency and easy maintenance.
- Commonly used in industries like pharmaceuticals, food processing, and wastewater treatment.
-
Recessed Chamber Filter Press:
- Similar to plate and frame presses but with recessed plates that form chambers.
- The chambers are filled with slurry, and the solids accumulate within the recessed areas.
- Offers higher capacity and better sealing compared to plate and frame designs.
- Suitable for handling slurries with high solid content.
- Often used in mining, chemical processing, and metallurgical industries.
-
Membrane Filter Press:
- A more advanced version of the recessed chamber press, featuring flexible membranes.
- After the initial filtration, the membranes are inflated to squeeze out additional liquid, reducing moisture content in the filter cake.
- Provides higher dewatering efficiency and shorter cycle times.
- Ideal for applications where dry filter cakes are required, such as in sludge dewatering and mineral processing.
-
Lab Filter Press:
- Designed for small-scale filtration tasks, typically in laboratory settings.
- Compact and easy to operate, making it suitable for research and development purposes.
- Often used for testing filtration processes before scaling up to industrial systems.
- Available in various configurations to mimic larger industrial filter presses.
- Essential for quality control and process optimization in the chemical industry. For more details, refer to lab filter press.
-
Selection Criteria for Filter Presses:
- Filtration Efficiency: The ability to separate solids from liquids effectively.
- Operational Costs: Includes energy consumption, maintenance, and labor requirements.
- Capacity: The volume of slurry the filter press can handle in a given time.
- Material Compatibility: Ensures the filter press materials are resistant to the chemicals being processed.
- Automation Level: Automated systems reduce manual intervention and improve consistency.
-
Applications in the Chemical Industry:
- Wastewater Treatment: Removing solids from industrial wastewater.
- Chemical Synthesis: Separating reaction byproducts from desired products.
- Pharmaceuticals: Purifying active pharmaceutical ingredients (APIs).
- Food and Beverage: Clarifying liquids and removing impurities.
By understanding the types and features of filter presses, chemical industry professionals can make informed decisions to enhance their filtration processes.
Summary Table:
Type of Filter Press | Key Features | Common Applications |
---|---|---|
Plate and Frame | Alternating plates and frames, high filtration efficiency, easy maintenance | Pharmaceuticals, food processing, wastewater treatment |
Recessed Chamber | Recessed plates form chambers, higher capacity, better sealing | Mining, chemical processing, metallurgical industries |
Membrane | Flexible membranes, higher dewatering efficiency, shorter cycle times | Sludge dewatering, mineral processing |
Lab Filter Press | Compact, easy to operate, ideal for R&D and small-scale filtration | Quality control, process optimization |
Need help selecting the right filter press for your chemical processes? Contact our experts today!