Induction melting furnaces are versatile and widely used in various industries for melting metals and alloys. They are primarily categorized based on their frequency, design, and operational characteristics. The main types include coreless, channel, and crucible induction furnaces, which differ in size, capacity, and frequency. Additionally, induction furnaces can be classified as main frequency or medium frequency based on their operating frequency. Vacuum induction melting furnaces, which operate under vacuum conditions, are further divided into batch-type and semi-continuous types, available in vertical or horizontal configurations. These furnaces are essential for applications like casting aircraft components, refining high-purity metals, and producing electrodes for remelting.
Key Points Explained:
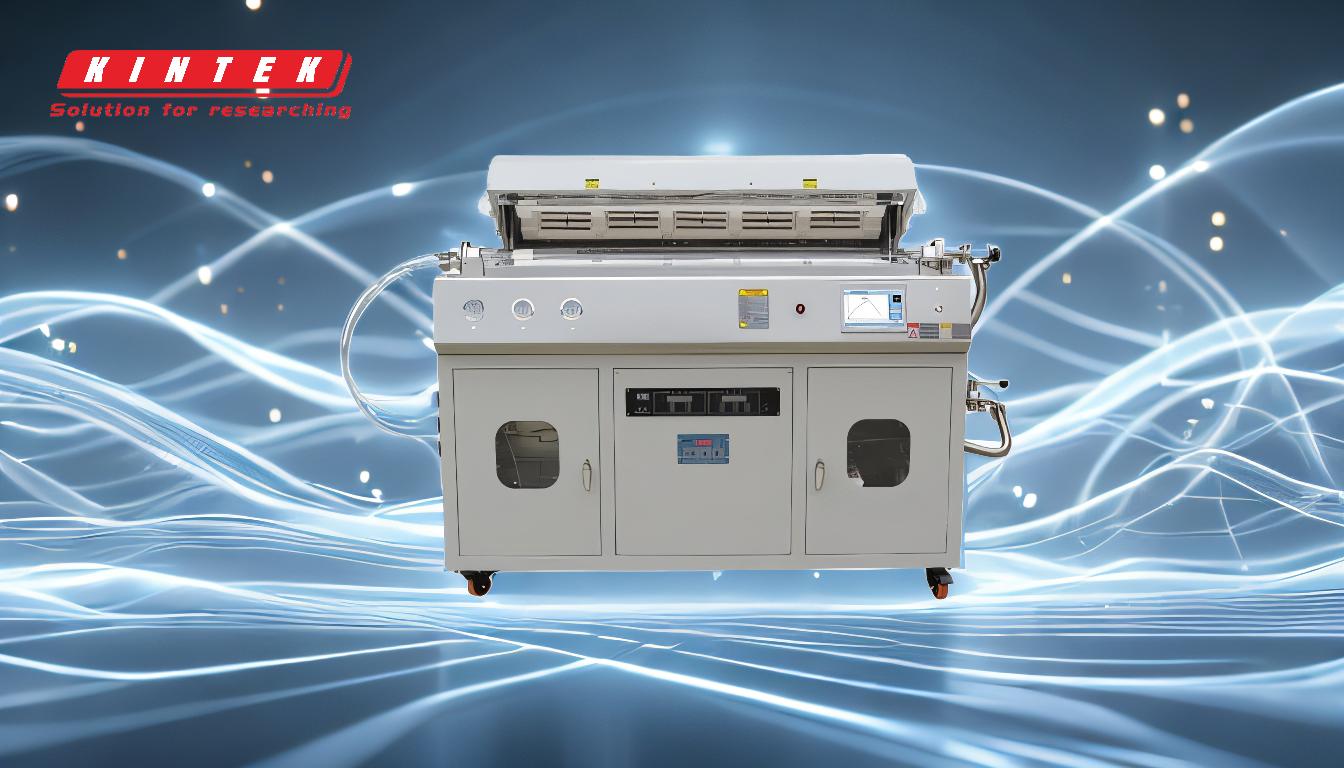
-
Coreless Induction Furnaces:
- These furnaces are characterized by the absence of a core, making them suitable for melting a wide range of metals.
- They are highly efficient for small to medium-scale operations and are commonly used in foundries.
- Coreless furnaces operate at higher frequencies, which allows for rapid heating and melting.
-
Channel Induction Furnaces:
- Channel furnaces have a core and are designed for continuous melting processes.
- They are ideal for large-scale operations and are often used in industries requiring consistent metal supply, such as automotive manufacturing.
- These furnaces operate at lower frequencies, making them energy-efficient for long-duration melting.
-
Crucible Induction Furnaces:
- Crucible furnaces use a refractory-lined crucible to hold the metal being melted.
- They are versatile and can handle a variety of metals, including precious metals like gold.
- These furnaces are available in different configurations, such as simple-type, cabinet-type, and footstep-type, to meet specific customer requirements.
-
Main Frequency vs. Medium Frequency Induction Furnaces:
- Main Frequency Induction Furnaces: Operate at the standard power grid frequency (50 Hz or 60 Hz). They are typically used for large-scale melting applications due to their high power capacity.
- Medium Frequency Induction Furnaces: Operate at higher frequencies (ranging from 100 Hz to 10 kHz). They are more efficient for smaller-scale operations and offer better control over the melting process.
-
Vacuum Induction Melting Furnaces:
- These furnaces operate under vacuum conditions, making them suitable for melting high-purity metals and alloys.
- They are available in two main types: batch-type and semi-continuous. Batch-type furnaces are used for single melting cycles, while semi-continuous furnaces allow for multiple melting cycles without breaking the vacuum.
- Vacuum induction melting furnaces can be configured as either vertical or horizontal, depending on the application and space constraints.
-
Applications of Induction Melting Furnaces:
- Aircraft Component Casting: Vacuum induction melting furnaces are used to produce high-strength, lightweight components for the aerospace industry.
- High-Purity Metal Refining: These furnaces are essential for refining metals like titanium, nickel, and cobalt to achieve the required purity levels.
- Electrode Production: Induction melting furnaces are used to produce electrodes for remelting processes, such as in the production of superalloys.
-
Other Types of Melting Furnaces:
- While induction furnaces are highly efficient, other types of melting furnaces, such as cupola furnaces, electric arc furnaces, and crucible furnaces, are also used in various industries. Each type has its unique advantages and is chosen based on the specific requirements of the application.
By understanding the different types of induction melting furnaces and their applications, purchasers can make informed decisions based on their specific needs, whether for small-scale precious metal melting or large-scale industrial applications.
Summary Table:
Type | Key Features | Applications |
---|---|---|
Coreless Induction | No core, high frequency, rapid heating, small to medium-scale operations | Foundries, small-scale metal melting |
Channel Induction | Core-based, low frequency, continuous melting, energy-efficient | Automotive manufacturing, large-scale metal supply |
Crucible Induction | Refractory-lined crucible, versatile, handles precious metals | Precious metal melting, customized configurations |
Main Frequency Induction | Standard power grid frequency (50/60 Hz), high power capacity | Large-scale melting applications |
Medium Frequency Induction | Higher frequency (100 Hz–10 kHz), efficient for smaller-scale operations | Smaller-scale melting, better process control |
Vacuum Induction Melting | Operates under vacuum, batch-type or semi-continuous, vertical/horizontal designs | Aerospace casting, high-purity metal refining, electrode production |
Ready to find the perfect induction melting furnace for your needs? Contact our experts today for personalized guidance!