Chemical vapor deposition (CVD) is a versatile and widely used process in various industries due to its ability to produce high-purity, uniform, and durable thin films or coatings on a wide range of materials. It is particularly valued for its non-line-of-sight nature, which allows for even coating of complex shapes, and its high deposition rates. CVD is used in electronics for semiconductor thin films, in cutting tools for wear and corrosion resistance, and in the production of thin-film solar cells. Additionally, it is employed to grow advanced materials like carbon nanotubes and GaN nanowires. The process is scalable, offers high manufacturing yield, and is suitable for creating ultra-thin layers, making it ideal for applications requiring precision and durability.
Key Points Explained:
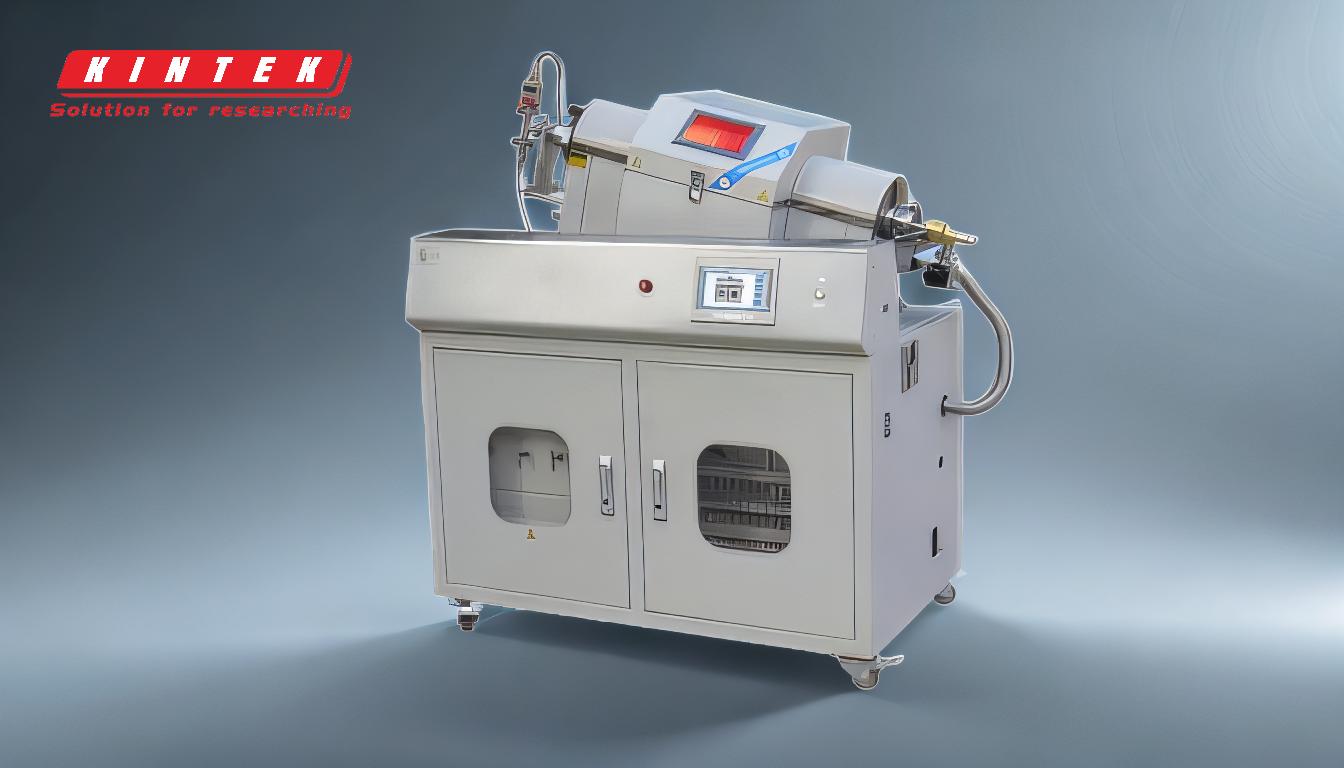
-
Versatility in Applications:
- CVD is used across multiple industries, including electronics, aerospace, and energy. It is particularly effective for depositing thin films on semiconductors, which are critical for electronic devices.
- In cutting tools, CVD is used to apply coatings that enhance wear and corrosion resistance, extending the lifespan of the tools.
- The process is also integral to the production of thin-film solar cells, where it deposits photovoltaic materials onto substrates.
-
Material Compatibility:
- CVD can be applied to a wide range of base materials, including glass, metals, and ceramics. This makes it a flexible solution for various industrial needs.
- The process can be tailored to optimize gases for specific properties, such as corrosion resistance, abrasion resistance, or high purity.
-
High-Quality Output:
- CVD produces high-purity and dense films or nanoparticles, which are essential for applications requiring precision and durability.
- The process allows for the creation of ultra-thin layers, which are crucial in the production of electrical circuits and other advanced technologies.
-
Non-Line-of-Sight Coating:
- One of the standout features of CVD is its non-line-of-sight nature, meaning it can evenly coat components with complex geometries. This is particularly useful in industries where intricate parts require uniform protection or functionality.
-
Scalability and Efficiency:
- CVD is known for its high deposition rates and scalability, making it suitable for both small-scale and large-scale manufacturing.
- The process offers a high manufacturing yield, ensuring that a significant proportion of the produced materials meet the required standards.
-
Durability in Extreme Conditions:
- Coatings produced by CVD are highly durable and can withstand high-stress environments, extreme temperatures, and temperature variations. This makes them ideal for use in harsh industrial conditions.
-
Advanced Material Growth:
- CVD is frequently used to grow advanced materials such as carbon nanotubes and GaN nanowires. These materials have unique properties that are valuable in nanotechnology and electronics.
In summary, chemical vapor deposition is a highly versatile and efficient process that plays a critical role in modern manufacturing and technology. Its ability to produce high-quality, durable, and precise coatings on a wide range of materials makes it indispensable in industries ranging from electronics to energy production.
Summary Table:
Key Applications | Description |
---|---|
Electronics | Deposits thin films on semiconductors for electronic devices. |
Cutting Tools | Enhances wear and corrosion resistance, extending tool lifespan. |
Thin-Film Solar Cells | Deposits photovoltaic materials for energy production. |
Advanced Materials | Grows carbon nanotubes and GaN nanowires for nanotechnology and electronics. |
Material Compatibility | Works with glass, metals, ceramics, and more. |
Non-Line-of-Sight Coating | Evenly coats complex geometries for uniform protection. |
Scalability | Suitable for both small-scale and large-scale manufacturing. |
Unlock the potential of chemical vapor deposition for your industry—contact us today to learn more!