Industrial furnaces are indispensable in various industries due to their ability to generate and maintain high temperatures for extended periods. They are utilized in a wide range of applications, including metal processing, material testing, and chemical synthesis. From annealing and tempering to sintering and melting, furnaces play a critical role in shaping, strengthening, and transforming materials. Their versatility extends to specialized processes like brazing, curing, and aging, making them essential for industries such as steel production, ceramics, and research laboratories. Below is a detailed breakdown of the key uses of furnaces in industrial settings.
Key Points Explained:
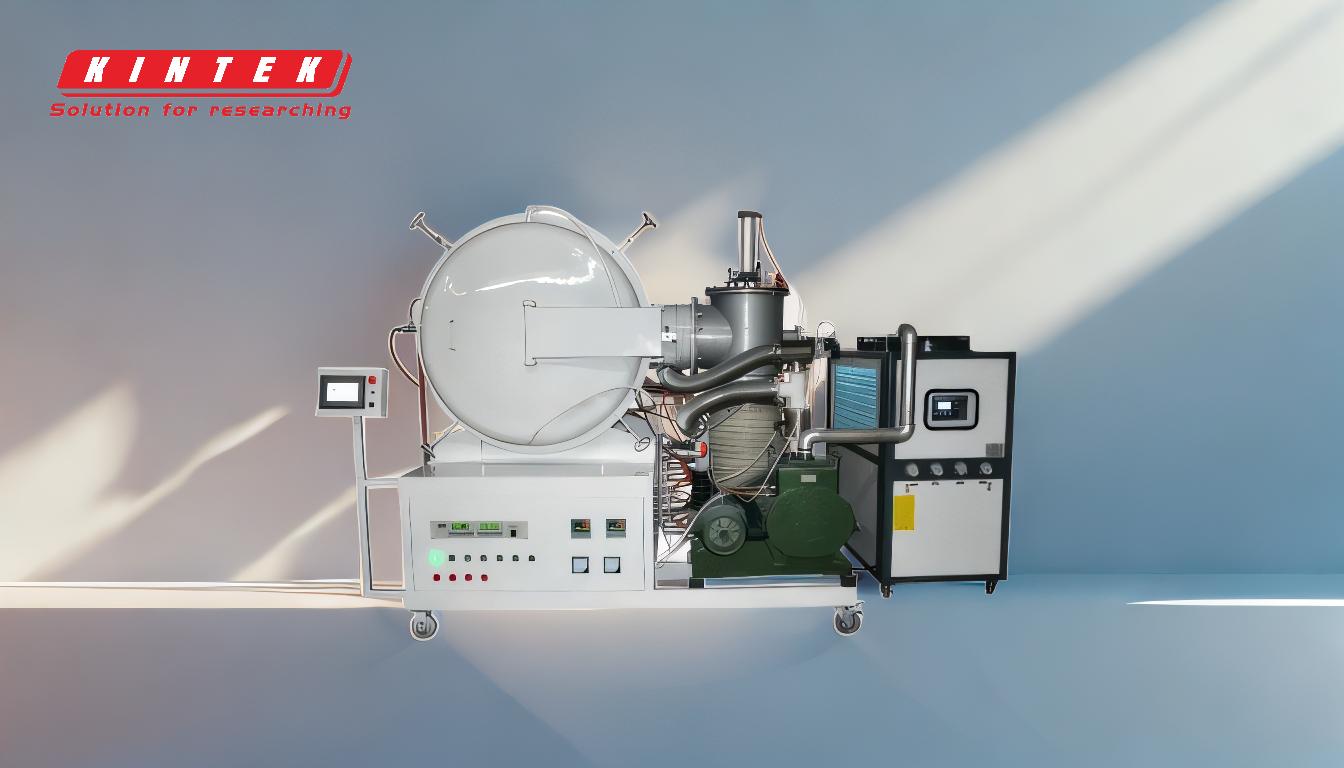
-
Annealing
- Purpose: Softening work-hardened materials to improve ductility and reduce internal stresses.
- Process: Heating metals to a specific temperature and then cooling them slowly.
- Applications: Used in steel, aluminum, and copper industries to prepare materials for further cold working or machining.
- Example: Annealing steel to make it more malleable for forming or stamping.
-
Smelting and Melting
- Purpose: Extracting metals from ores or melting metals for casting.
- Process: Heating raw materials to high temperatures to separate metal from impurities.
- Applications: Essential in steel production, aluminum smelting, and foundries for creating metal alloys or casting components.
- Example: Melting iron ore in a blast furnace to produce pig iron.
-
Tempering
- Purpose: Enhancing the toughness of hardened metals while reducing brittleness.
- Process: Heating quenched metals to a temperature below their critical point and then cooling them.
- Applications: Commonly used in tool manufacturing and automotive industries to improve the durability of steel components.
- Example: Tempering steel gears to balance hardness and toughness.
-
Heat Treatment
- Purpose: Altering the physical and mechanical properties of metals through controlled heating and cooling.
- Process: Includes processes like hardening, normalizing, and stress relieving.
- Applications: Widely used in aerospace, automotive, and machinery industries to enhance material performance.
- Example: Heat-treating aircraft components to improve strength and fatigue resistance.
-
Sintering
- Purpose: Bonding powdered materials into a solid mass without melting.
- Process: Heating powders below their melting point to fuse particle surfaces.
- Applications: Used in powder metallurgy, ceramics, and 3D printing industries.
- Example: Sintering ceramic tiles to create durable, heat-resistant surfaces.
-
Brazing and Soldering
- Purpose: Joining metal parts using a filler material.
- Process: Heating the assembly to melt the filler metal, which flows into the joint.
- Applications: Common in electronics, plumbing, and automotive industries.
- Example: Brazing copper pipes in HVAC systems.
-
Curing and Drying
- Purpose: Removing moisture or solidifying materials through heat.
- Process: Heating materials to drive off solvents or initiate chemical reactions.
- Applications: Used in coatings, adhesives, and composite manufacturing.
- Example: Curing epoxy coatings on industrial equipment.
-
Aging
- Purpose: Altering the properties of alloys over time at elevated temperatures.
- Process: Heating materials to specific temperatures to achieve desired mechanical properties.
- Applications: Common in aluminum and titanium industries.
- Example: Aging aluminum alloys to improve strength and corrosion resistance.
-
Quenching
- Purpose: Rapidly cooling metals to achieve specific material properties.
- Process: Heating metals to high temperatures and then immersing them in a cooling medium (e.g., water, oil).
- Applications: Used in tool and die manufacturing to harden steel.
- Example: Quenching steel cutting tools to increase hardness.
-
Burning Off and Degassing
- Purpose: Removing unwanted coatings or gases from materials.
- Process: Heating materials to high temperatures to burn off contaminants or release trapped gases.
- Applications: Used in metal refining and semiconductor manufacturing.
- Example: Degassing aluminum alloys to remove hydrogen bubbles.
-
Laboratory and Research Applications
- Purpose: Conducting thermal testing and material synthesis.
- Process: Precise temperature control for experiments and small-scale production.
- Applications: Used in universities, research labs, and dental labs for material analysis and development.
- Example: Testing ceramic materials for high-temperature stability.
-
Specialized Processes
- Purpose: Performing unique thermal treatments for specific industries.
- Process: Includes processes like calcination, pyrolysis, and thermocouple calibration.
- Applications: Used in chemical, pharmaceutical, and energy industries.
- Example: Pyrolysis of biomass to produce biofuels.
Furnaces are a cornerstone of industrial operations, enabling the transformation and refinement of materials across diverse sectors. Their ability to maintain precise and consistent high temperatures makes them invaluable for processes ranging from metalworking to advanced material synthesis. Whether in large-scale steel production or cutting-edge research labs, furnaces continue to drive innovation and efficiency in industrial applications.
Summary Table:
Process | Purpose | Applications | Example |
---|---|---|---|
Annealing | Soften materials, improve ductility, reduce internal stresses | Steel, aluminum, copper industries | Annealing steel for forming or stamping |
Smelting/Melting | Extract metals from ores or melt metals for casting | Steel production, aluminum smelting, foundries | Melting iron ore to produce pig iron |
Tempering | Enhance toughness, reduce brittleness in hardened metals | Tool manufacturing, automotive industries | Tempering steel gears for durability |
Heat Treatment | Alter physical and mechanical properties of metals | Aerospace, automotive, machinery industries | Heat-treating aircraft components for strength |
Sintering | Bond powdered materials without melting | Powder metallurgy, ceramics, 3D printing | Sintering ceramic tiles for heat-resistant surfaces |
Brazing/Soldering | Join metal parts using filler material | Electronics, plumbing, automotive industries | Brazing copper pipes in HVAC systems |
Curing/Drying | Remove moisture or solidify materials through heat | Coatings, adhesives, composite manufacturing | Curing epoxy coatings on industrial equipment |
Aging | Alter alloy properties over time at elevated temperatures | Aluminum, titanium industries | Aging aluminum alloys for improved strength |
Quenching | Rapidly cool metals to achieve specific properties | Tool and die manufacturing | Quenching steel cutting tools for hardness |
Burning Off/Degassing | Remove coatings or gases from materials | Metal refining, semiconductor manufacturing | Degassing aluminum alloys to remove hydrogen bubbles |
Lab/Research | Conduct thermal testing and material synthesis | Universities, research labs, dental labs | Testing ceramic materials for high-temperature stability |
Specialized Processes | Perform unique thermal treatments for specific industries | Chemical, pharmaceutical, energy industries | Pyrolysis of biomass to produce biofuels |
Ready to enhance your industrial processes with the right furnace? Contact our experts today for tailored solutions!