Plasma Enhanced Chemical Vapor Deposition (PECVD) is a versatile and widely used technique in the semiconductor and materials science industries. It leverages plasma to enhance chemical reactions, enabling the deposition of thin films at lower temperatures compared to traditional methods. This makes PECVD particularly valuable for applications requiring precise control over film properties, such as in the fabrication of microelectronics, photovoltaics, and advanced materials like graphene. The process involves ionizing gas to create a plasma, which then facilitates the deposition of materials like silicon oxides, silicon nitride, and amorphous silicon onto substrates. PECVD's ability to operate at lower temperatures while maintaining high deposition rates and film quality makes it indispensable in modern manufacturing processes.
Key Points Explained:
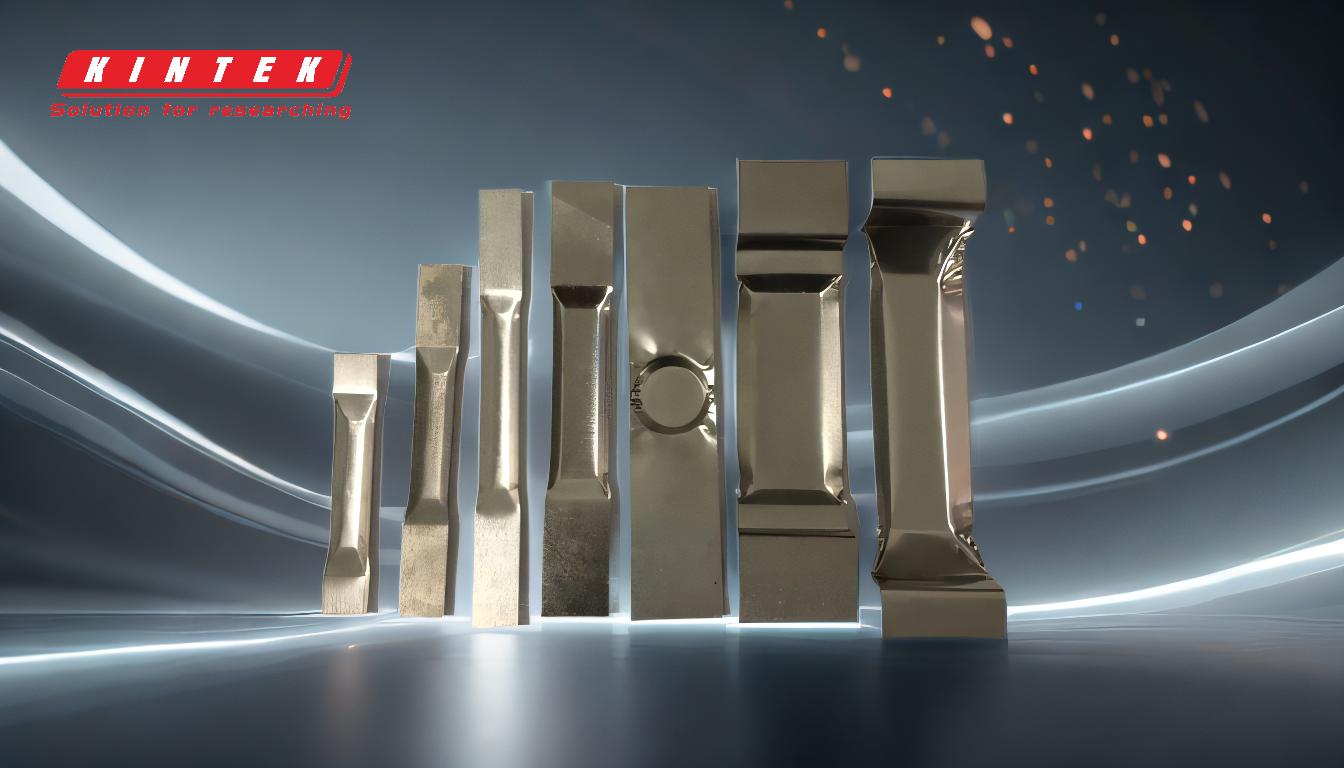
-
Low-Temperature Deposition:
- PECVD operates at significantly lower temperatures (100°C – 400°C) compared to other chemical vapor deposition (CVD) methods, such as Low-Pressure CVD (LPCVD), which requires temperatures between 425°C and 900°C. This is achieved by using plasma to provide the energy needed for the chemical reactions, rather than relying solely on thermal energy.
- The lower processing temperatures are crucial for applications involving temperature-sensitive substrates or materials, such as polymers or certain semiconductor devices, where high temperatures could degrade material properties or alter electrical characteristics.
-
Enhanced Chemical Activity:
- The plasma in PECVD excites the gas molecules, creating highly reactive species such as ions, radicals, and electrons. These excited species have higher chemical activity, enabling faster and more efficient deposition reactions at lower temperatures.
- This enhanced chemical activity allows for the deposition of high-quality films with excellent adhesion and uniformity, even on complex or delicate substrates.
-
Versatility in Film Deposition:
- PECVD is used to deposit a wide range of materials, including silicon oxides (SiO₂), silicon nitride (Si₃N₄), amorphous silicon (a-Si), and silicon oxynitrides (SiON). These materials are essential for various applications in microelectronics, such as insulating layers, passivation layers, and gate dielectrics.
- The ability to precisely control the composition and properties of the deposited films makes PECVD suitable for advanced applications, such as the fabrication of photovoltaic cells, MEMS devices, and optical coatings.
-
Precision in Material Morphology:
- PECVD, particularly Radio Frequency PECVD (RF-PECVD), is highly effective in controlling the morphology of deposited materials. For example, it is used to grow regular vertical graphene structures, which have unique properties for applications in energy storage, sensors, and electronics.
- The precise control over film thickness, density, and conformality is critical for modern semiconductor devices, where shrinking geometries require exacting standards.
-
High Deposition Rates:
- Despite operating at lower temperatures, PECVD maintains high deposition rates, making it a time-efficient process. This is particularly important in industrial settings where throughput and productivity are key considerations.
- The combination of low temperature and high deposition rates also helps preserve the integrity of the substrate and the deposited material, reducing the risk of thermal damage or stress-induced defects.
-
Applications in Advanced Technologies:
- PECVD is integral to the fabrication of advanced materials and devices, such as graphene-based electronics, thin-film transistors, and photovoltaic cells. Its ability to deposit high-quality films at low temperatures makes it ideal for next-generation technologies.
- In the field of photovoltaics, PECVD is used to deposit anti-reflective coatings and passivation layers, which improve the efficiency and durability of solar cells.
-
Integration with Semiconductor Manufacturing:
- PECVD is a key process in semiconductor manufacturing, where it is used to deposit dielectric layers, passivation layers, and other critical components. Its compatibility with temperature-sensitive materials and processes makes it a preferred choice for advanced nodes in semiconductor fabrication.
- The technique's ability to deposit conformal films over complex geometries is particularly valuable for 3D structures in modern integrated circuits.
In summary, PECVD is a highly versatile and efficient deposition technique that plays a critical role in modern manufacturing and research. Its ability to deposit high-quality films at low temperatures, combined with precise control over material properties, makes it indispensable for a wide range of applications in electronics, photovoltaics, and advanced materials.
Summary Table:
Feature | Description |
---|---|
Low-Temperature Deposition | Operates at 100°C – 400°C, ideal for temperature-sensitive substrates. |
Enhanced Chemical Activity | Plasma excites gas molecules for faster, efficient reactions. |
Versatility in Film Deposition | Deposits SiO₂, Si₃N₄, a-Si, and SiON for microelectronics and photovoltaics. |
Precision in Morphology | Controls film thickness, density, and conformality for advanced applications. |
High Deposition Rates | Maintains high rates at low temperatures, boosting productivity. |
Applications | Used in graphene electronics, solar cells, MEMS, and semiconductor manufacturing. |
Learn how PECVD can revolutionize your manufacturing process—contact our experts today!