Tube furnace tubes are typically made from materials that can withstand high temperatures and resist chemical reactions, ensuring the integrity of both the furnace and the samples being processed. Common materials include alumina, fused quartz, and Pyrex, which are chosen for their heat resistance and durability. For more corrosive environments, materials like tungsten or molybdenum are used due to their superior resistance to chemical attack. The choice of material depends on the specific application, temperature requirements, and the nature of the materials being processed.
Key Points Explained:
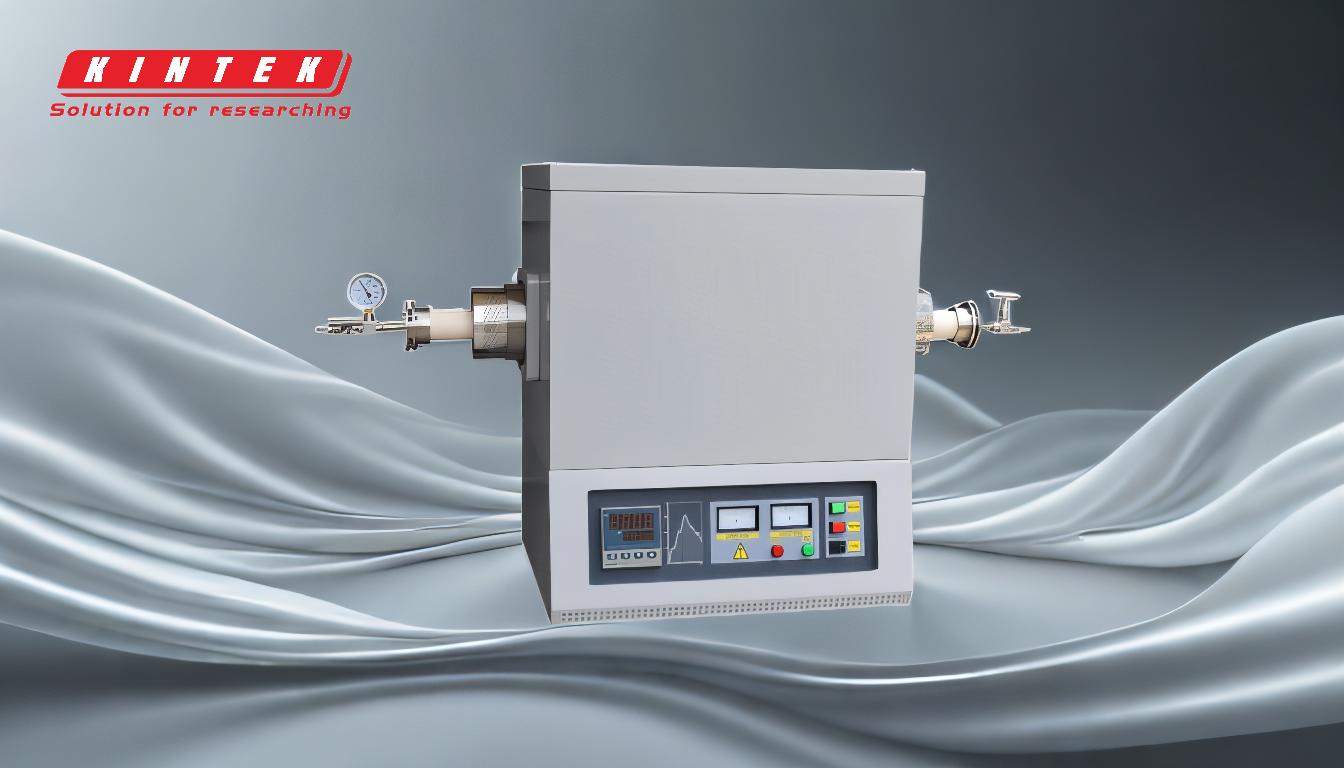
-
Alumina Tubes:
- Alumina (Al₂O₃) is one of the most commonly used materials for tube furnace tubes.
- It is highly resistant to high temperatures and chemical corrosion, making it suitable for a wide range of applications.
- Alumina tubes are often used in environments where temperatures can reach up to 1800°C.
- They are also known for their excellent thermal shock resistance, which is crucial in applications involving rapid temperature changes.
-
Fused Quartz Tubes:
- Fused quartz is another popular material for tube furnace tubes.
- It has a high melting point and excellent thermal stability, making it ideal for high-temperature applications.
- Fused quartz tubes are transparent to infrared radiation, which allows for efficient heat transfer.
- They are also chemically inert, making them suitable for use with a wide range of chemicals.
-
Pyrex Tubes:
- Pyrex, a type of borosilicate glass, is used in tube furnaces where lower temperatures are involved.
- It is known for its thermal shock resistance and chemical durability.
- Pyrex tubes are typically used in applications where temperatures do not exceed 500°C.
- They are also transparent, allowing for visual monitoring of the process inside the tube.
-
Tungsten and Molybdenum Tubes:
- Tungsten and molybdenum are used in tube furnaces when dealing with highly corrosive materials.
- Both materials have extremely high melting points and excellent resistance to chemical attack.
- Tungsten tubes are particularly useful in environments where temperatures exceed 2000°C.
- Molybdenum tubes are often used in reducing atmospheres where other materials might fail.
-
Ceramic Materials:
- Ceramic materials like mullite and recrystallized alumina (RCA) are also used for tube furnace tubes.
- These materials offer high thermal stability and resistance to chemical reactions.
- Mullite tubes are known for their excellent thermal shock resistance and are often used in high-temperature applications.
- RCA tubes are highly durable and can withstand extreme temperatures, making them suitable for demanding environments.
-
Metal Tubes:
- Metals such as stainless steel and Inconel are used in tube furnaces for specific applications.
- Stainless steel tubes are used in lower temperature applications and where corrosion resistance is required.
- Inconel tubes are used in high-temperature environments and offer excellent resistance to oxidation and corrosion.
-
Function of the Tube:
- The tube in a tube furnace serves to maintain the integrity of the furnace interior and the samples being processed.
- It prevents chemical reactions that could damage the furnace insulation or contaminate the sample.
- The tube also helps in maintaining a consistent operating temperature, which is crucial for the success of the process.
In summary, the choice of material for tube furnace tubes depends on the specific requirements of the application, including temperature, chemical environment, and the nature of the materials being processed. Each material offers unique properties that make it suitable for different scenarios, ensuring the efficient and safe operation of the tube furnace.
Summary Table:
Material | Key Properties | Temperature Range | Applications |
---|---|---|---|
Alumina | High temperature resistance, chemical corrosion resistance, thermal shock resistance | Up to 1800°C | Wide range of high-temperature applications |
Fused Quartz | High melting point, thermal stability, chemically inert, transparent to IR | High-temperature | Efficient heat transfer, chemically inert environments |
Pyrex | Thermal shock resistance, chemical durability, transparent | Up to 500°C | Lower temperature applications with visual monitoring |
Tungsten | Extremely high melting point, superior chemical resistance | Exceeds 2000°C | Highly corrosive and extreme temperature environments |
Molybdenum | High melting point, excellent chemical resistance | Reducing atmospheres | Corrosive and high-temperature environments |
Ceramic (Mullite) | Excellent thermal shock resistance, high thermal stability | High-temperature | High-temperature applications with thermal shock requirements |
Stainless Steel | Corrosion resistance, lower temperature applications | Lower temperature | Applications requiring corrosion resistance |
Inconel | Oxidation and corrosion resistance, high-temperature stability | High-temperature | High-temperature and corrosive environments |
Need help selecting the right tube furnace tube material for your application? Contact our experts today for personalized guidance!