A hydraulic press, especially a hydraulic hot press machine, is a robust piece of equipment designed to handle high-pressure tasks. However, several factors can lead to its destruction or significant damage. These include improper maintenance, overloading, contamination of hydraulic fluid, overheating, and mechanical failures. Understanding these risks and taking preventive measures can extend the lifespan of the equipment and ensure its efficient operation.
Key Points Explained:
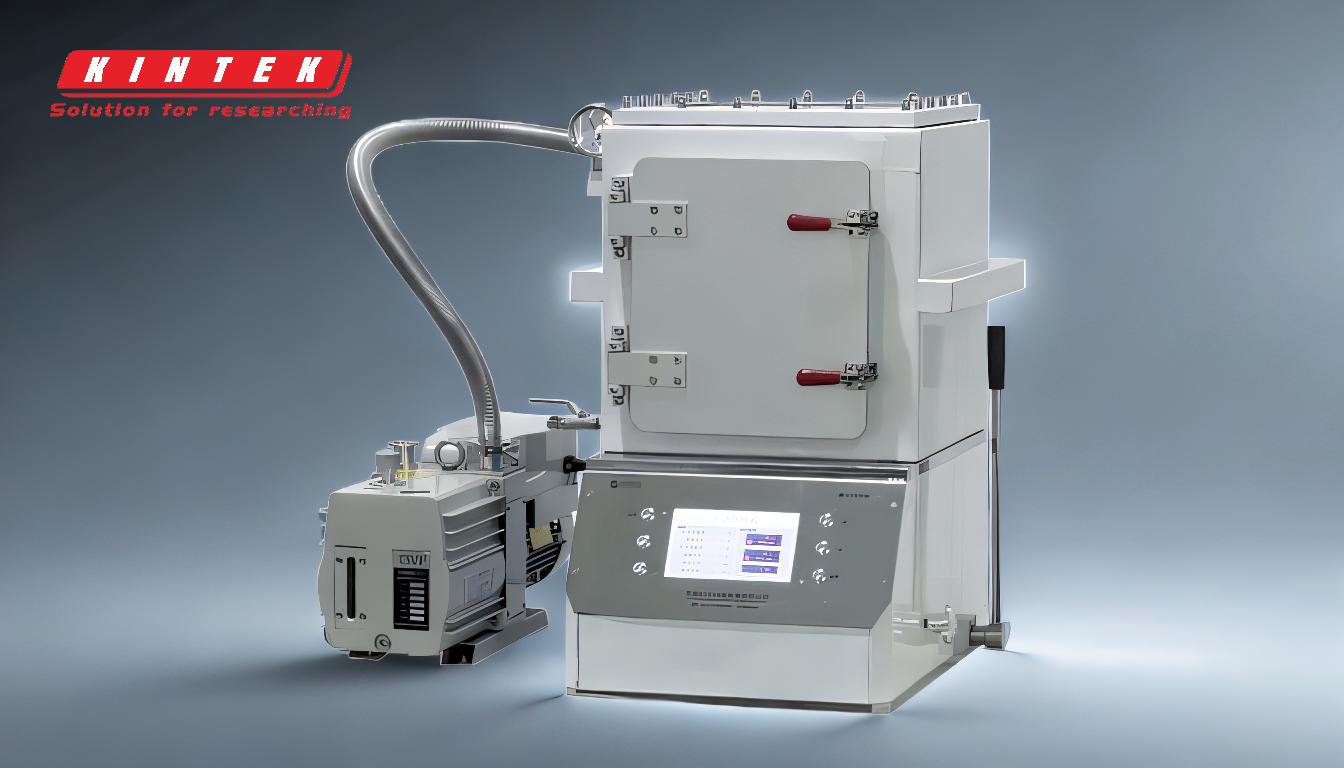
-
Improper Maintenance
- Lack of Regular Inspections: Failing to conduct regular inspections can lead to undetected issues such as leaks, worn-out seals, or damaged components. Over time, these small problems can escalate, causing significant damage to the hydraulic press.
- Neglecting Lubrication: Proper lubrication is essential for the smooth operation of moving parts. Without it, friction increases, leading to wear and tear, and eventually, mechanical failure.
- Ignoring Manufacturer Guidelines: Not adhering to the manufacturer's maintenance schedule and recommendations can result in premature wear and potential breakdowns.
-
Overloading
- Exceeding Capacity: Operating the hydraulic press beyond its rated capacity can cause excessive stress on the system. This can lead to structural failures, such as bending or breaking of the frame, and damage to the hydraulic cylinders and pumps.
- Sudden Loads: Applying sudden or shock loads can also be detrimental. The hydraulic system is designed to handle gradual increases in pressure, and abrupt changes can cause immediate damage.
-
Contamination of Hydraulic Fluid
- Dirt and Debris: Contaminants in the hydraulic fluid can clog valves, damage seals, and erode internal components. This not only reduces the efficiency of the press but can also lead to catastrophic failures.
- Water Contamination: Water in the hydraulic fluid can cause corrosion of metal parts and degrade the fluid's lubricating properties, leading to increased wear and potential system failure.
- Chemical Contamination: Exposure to chemicals that are incompatible with the hydraulic fluid can cause it to break down, reducing its effectiveness and potentially causing damage to the system.
-
Overheating
- Excessive Use: Continuous operation without adequate cooling can cause the hydraulic fluid to overheat. This can lead to a breakdown of the fluid, reduced lubrication, and increased wear on components.
- Insufficient Cooling Systems: If the cooling systems (such as radiators or fans) are not functioning properly, the hydraulic system can overheat, leading to potential damage.
- High Ambient Temperatures: Operating in environments with high ambient temperatures without proper cooling measures can exacerbate overheating issues.
-
Mechanical Failures
- Component Wear: Over time, components such as seals, hoses, and pistons can wear out. If not replaced promptly, this can lead to leaks, reduced performance, and eventual failure.
- Misalignment: Misalignment of the press components can cause uneven stress distribution, leading to premature wear and potential failure.
- Fatigue: Repeated stress cycles can cause metal fatigue in critical components, leading to cracks and eventual failure.
-
Electrical Issues
- Power Surges: Electrical surges can damage the control systems of the hydraulic press, leading to malfunctions or complete failure.
- Faulty Wiring: Poor wiring or connections can cause intermittent operation, overheating, or even fires, posing a significant risk to the equipment and operators.
-
Operational Errors
- Improper Use: Using the hydraulic press for tasks it is not designed for can cause undue stress and damage.
- Lack of Training: Operators who are not properly trained may misuse the equipment, leading to accidents and damage.
- Ignoring Warning Signs: Failing to address warning signs such as unusual noises, leaks, or performance issues can lead to more severe problems.
By understanding these potential risks and implementing a comprehensive maintenance and operational strategy, the lifespan of a hydraulic hot press machine can be significantly extended, ensuring reliable and efficient performance.
Summary Table:
Factor | Impact | Preventive Measures |
---|---|---|
Improper Maintenance | Undetected issues, wear, and breakdowns | Regular inspections, proper lubrication, follow manufacturer guidelines |
Overloading | Structural failures, damage to cylinders and pumps | Operate within rated capacity, avoid sudden or shock loads |
Contamination | Clogged valves, damaged seals, corrosion | Use clean hydraulic fluid, prevent water and chemical contamination |
Overheating | Fluid breakdown, reduced lubrication, component wear | Ensure proper cooling systems, avoid excessive use, monitor ambient temperatures |
Mechanical Failures | Leaks, misalignment, fatigue, cracks | Replace worn components promptly, ensure proper alignment, monitor stress cycles |
Electrical Issues | Control system damage, overheating, fires | Protect against power surges, ensure proper wiring and connections |
Operational Errors | Undue stress, accidents, severe damage | Train operators properly, use equipment as intended, address warning signs immediately |
Protect your hydraulic press from damage—contact our experts today for maintenance tips and solutions!