PVD (Physical Vapor Deposition) coatings are versatile and can be applied to a wide range of substrates across various industries. These coatings are used to enhance properties such as hardness, wear resistance, corrosion resistance, and electrical conductivity. Common substrates include metals, alloys, plastics, glass, and ceramics. Applications span from aerospace and automotive components to medical devices, electronics, and consumer goods like jewelry, eyeglass frames, and kitchen fixtures. PVD coatings are also environmentally friendly, offering a greener alternative to traditional plating methods like chrome plating.
Key Points Explained:
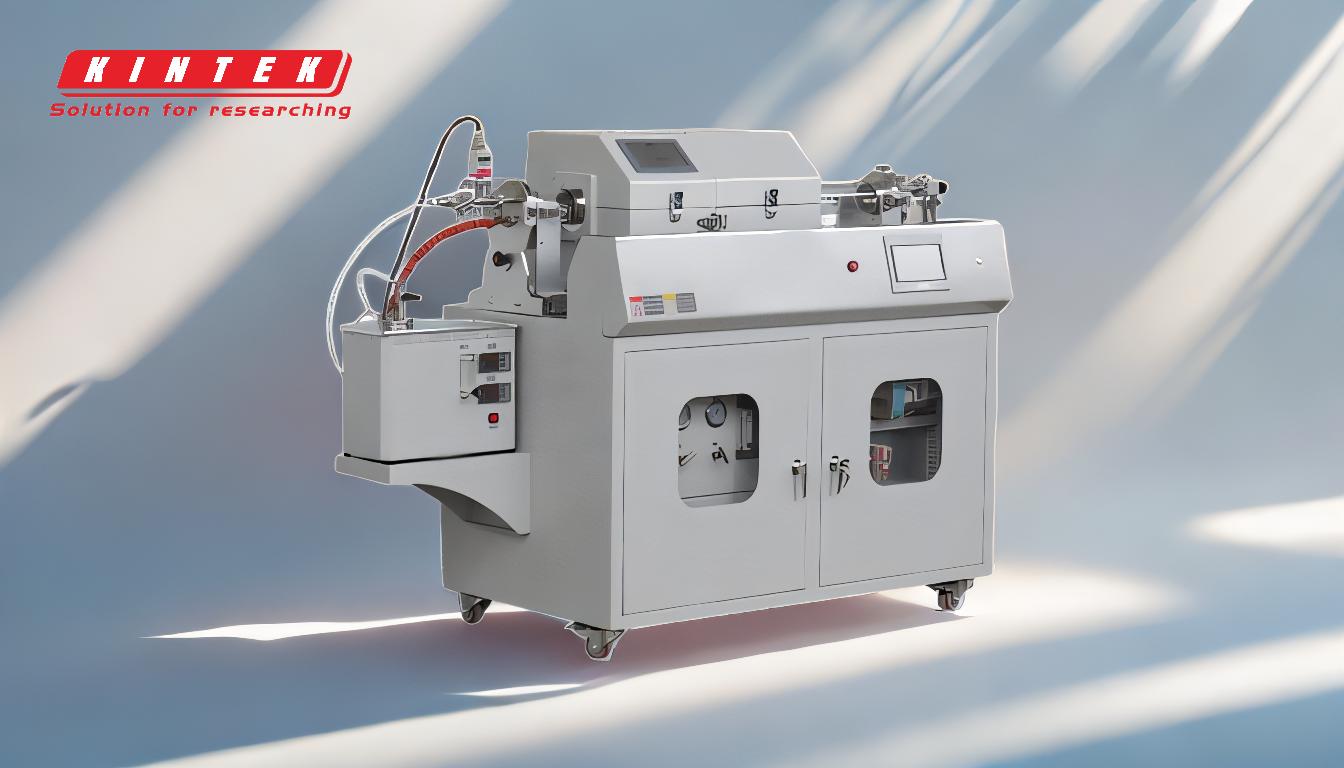
-
Substrates for PVD Coatings:
- Metals and Alloys: PVD coatings are commonly applied to metals such as steel, aluminum, titanium, and their alloys. These coatings improve properties like hardness, wear resistance, and corrosion resistance, making them ideal for automotive parts, aerospace components, and industrial tools.
- Plastics: PVD coatings can be applied to plastics like ABS, polycarbonate, and PC-ABS. This is particularly useful in consumer electronics, automotive interiors, and decorative applications where a metallic finish is desired without the weight of metal.
- Glass and Ceramics: These substrates benefit from PVD coatings in applications requiring enhanced optical properties, such as anti-reflective coatings for lenses or mirrors, and in semiconductor manufacturing where chemical resistance is crucial.
-
Applications in Various Industries:
- Aerospace and Automotive: PVD coatings are used to enhance the durability and performance of components like engine parts, pistons, and turbine blades. They also improve the lifespan of cutting tools and molds used in material processing.
- Medical and Surgical: Medical implants, surgical tools, and biomedical instruments often receive PVD coatings to improve biocompatibility, reduce wear, and resist corrosion. Titanium coatings, for example, are commonly used in medical implants.
- Electronics: PVD coatings are used in the electronics industry to apply thin films of gold, silver, or other conductive materials, replacing traditional plating methods. These coatings are essential in creating components for semiconductors, sensors, and optical devices.
- Consumer Goods: PVD coatings are widely used in products like jewelry, eyeglass frames, kitchen fixtures, and sporting goods. They provide a durable, aesthetically pleasing finish that resists tarnishing and wear.
-
Functional Benefits of PVD Coatings:
- Enhanced Durability: PVD coatings significantly increase the lifespan of products by improving hardness and wear resistance. Studies have shown that PVD-coated components can last up to ten times longer than uncoated ones.
- Corrosion and Oxidation Resistance: These coatings protect substrates from environmental factors, making them suitable for harsh conditions, such as marine hardware or outdoor automotive components.
- Electrical and Optical Performance: PVD coatings are used to enhance electrical conductivity in electronics and improve optical properties in lenses, mirrors, and window tints.
-
Environmental Advantages:
- Greener Alternative to Chrome Plating: PVD coatings are more environmentally friendly than traditional chrome plating, as they do not produce toxic substances like hexavalent chromium. This makes them a preferred choice in industries looking to reduce their environmental footprint.
- Longevity and Sustainability: By extending the lifespan of products, PVD coatings contribute to sustainability by reducing the need for frequent replacements and minimizing waste.
-
Versatility in Deposition Materials:
- PVD coatings can be applied using a variety of materials, including metals (e.g., titanium, gold, silver), ceramics (e.g., titanium nitride, chromium nitride), and even organic compounds. This flexibility allows for tailored solutions to meet specific application requirements, such as high-temperature resistance or biocompatibility.
In summary, PVD coatings are highly versatile and can be applied to a wide range of substrates, including metals, plastics, glass, and ceramics. They offer significant functional benefits, such as enhanced durability, corrosion resistance, and improved electrical and optical properties. These coatings are used across various industries, from aerospace and automotive to medical and consumer goods, and provide an environmentally friendly alternative to traditional plating methods.
Summary Table:
Aspect | Details |
---|---|
Substrates | Metals, alloys, plastics, glass, ceramics |
Applications | Aerospace, automotive, medical, electronics, consumer goods |
Functional Benefits | Enhanced durability, corrosion resistance, electrical/optical performance |
Environmental Benefits | Greener alternative to chrome plating, reduced waste |
Materials Used | Metals (titanium, gold), ceramics (titanium nitride), organic compounds |
Unlock the potential of PVD coatings for your industry—contact our experts today!