Hydraulic systems running slow can be attributed to several factors, including fluid issues, mechanical problems, or system design flaws. Understanding the root cause is essential for effective troubleshooting and maintenance. Common reasons include low fluid levels, contaminated hydraulic fluid, worn-out components, improper system design, or external factors like temperature changes. Addressing these issues promptly ensures optimal system performance and longevity.
Key Points Explained:
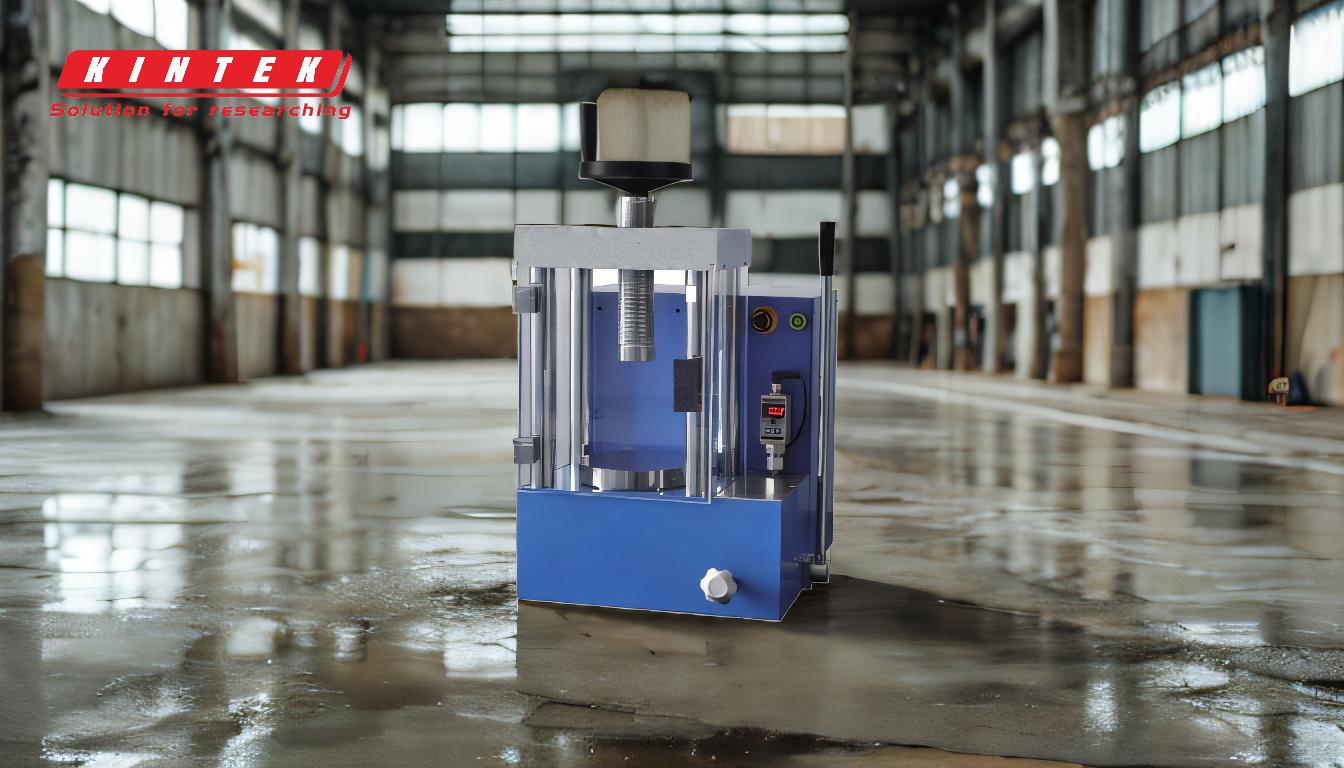
-
Low Hydraulic Fluid Levels
- Explanation: Insufficient hydraulic fluid reduces the system's ability to generate the necessary pressure to operate efficiently. This can lead to slower operation or even complete failure.
- Solution: Regularly check and maintain the fluid level according to the manufacturer's recommendations. Top up the fluid if necessary, and inspect for leaks that could cause fluid loss.
-
Contaminated Hydraulic Fluid
- Explanation: Dirt, debris, or water in the hydraulic fluid can clog valves, filters, and other components, reducing flow and pressure. Contamination can also cause wear and tear on internal parts.
- Solution: Use high-quality hydraulic fluid and replace it at recommended intervals. Install and maintain effective filtration systems to prevent contamination.
-
Worn-Out or Damaged Components
- Explanation: Over time, components like pumps, valves, cylinders, and seals can wear out or become damaged, leading to reduced efficiency and slower operation.
- Solution: Regularly inspect and replace worn-out parts. Use high-quality components that are compatible with the system's specifications.
-
Improper System Design or Sizing
- Explanation: If the hydraulic system is undersized or improperly designed for the application, it may not generate sufficient pressure or flow to operate at the desired speed.
- Solution: Ensure the system is correctly sized and designed for the intended application. Consult with hydraulic system experts if necessary.
-
Air in the Hydraulic System
- Explanation: Air trapped in the hydraulic fluid can cause spongy operation and reduce the system's efficiency, leading to slower performance.
- Solution: Bleed the system to remove air and ensure all connections are tight to prevent air ingress.
-
Temperature-Related Issues
- Explanation: Extreme temperatures can affect the viscosity of the hydraulic fluid, making it either too thick (cold) or too thin (hot), which impacts system performance.
- Solution: Use hydraulic fluid with the appropriate viscosity for the operating temperature range. Consider installing temperature control systems if necessary.
-
Incorrect Pressure Settings
- Explanation: If the pressure settings are too low, the system will not operate at its full capacity, resulting in slower performance.
- Solution: Adjust the pressure settings according to the manufacturer's specifications. Use a pressure gauge to ensure accuracy.
-
Restricted Flow Paths
- Explanation: Blockages or restrictions in the hydraulic lines, hoses, or fittings can reduce flow and pressure, causing the system to run slowly.
- Solution: Inspect and clean all flow paths regularly. Replace damaged or restricted components.
-
Inadequate Pump Performance
- Explanation: A failing or undersized hydraulic pump cannot deliver the required flow and pressure, leading to slower operation.
- Solution: Ensure the pump is properly sized for the system and replace it if it shows signs of wear or failure.
-
External Load or Resistance
- Explanation: Excessive external load or resistance can strain the hydraulic system, causing it to operate slower than intended.
- Solution: Ensure the system is not overloaded and that external components are functioning correctly. Adjust the load if necessary.
By addressing these key points systematically, you can diagnose and resolve the issue of a slow-running hydraulic system, ensuring it operates efficiently and reliably. Regular maintenance and proper system design are critical to preventing such problems in the future.
Summary Table:
Cause | Explanation | Solution |
---|---|---|
Low Hydraulic Fluid Levels | Insufficient fluid reduces pressure, causing slower operation or failure. | Regularly check and maintain fluid levels; inspect for leaks. |
Contaminated Hydraulic Fluid | Dirt or debris clogs components, reducing flow and pressure. | Use high-quality fluid, replace it regularly, and maintain filtration systems. |
Worn-Out or Damaged Components | Worn pumps, valves, or seals reduce efficiency and slow operation. | Inspect and replace worn parts; use high-quality, compatible components. |
Improper System Design | Undersized or poorly designed systems lack sufficient pressure or flow. | Ensure proper system sizing and design; consult experts if needed. |
Air in the Hydraulic System | Air in the fluid causes spongy operation and reduced efficiency. | Bleed the system to remove air; ensure tight connections. |
Temperature-Related Issues | Extreme temperatures affect fluid viscosity, impacting performance. | Use fluid with appropriate viscosity; consider temperature control systems. |
Incorrect Pressure Settings | Low pressure settings prevent the system from operating at full capacity. | Adjust pressure settings according to manufacturer specifications. |
Restricted Flow Paths | Blockages in lines or fittings reduce flow and pressure. | Inspect and clean flow paths; replace damaged components. |
Inadequate Pump Performance | A failing or undersized pump cannot deliver required flow and pressure. | Ensure proper pump sizing; replace worn or failing pumps. |
External Load or Resistance | Excessive load strains the system, slowing operation. | Ensure the system is not overloaded; adjust external components if necessary. |
Need help troubleshooting your hydraulic system? Contact our experts today for tailored solutions!