Furnace operators play a critical role in managing and maintaining the performance of industrial furnaces. Their responsibilities include monitoring and controlling temperature, heat delivery, and other operational variables to ensure efficient and safe furnace operation. They work closely with furnace controllers, which manage burner flames, air mixtures, and other parameters to optimize performance. Furnace operators also rely on inputs from thermocouples and sensors to make real-time adjustments and ensure the furnace operates within desired specifications. Additionally, they may oversee the integration of furnace controls with broader industrial systems and monitor specific variables like carbon dioxide, methane, or ammonia levels, depending on the furnace's application.
Key Points Explained:
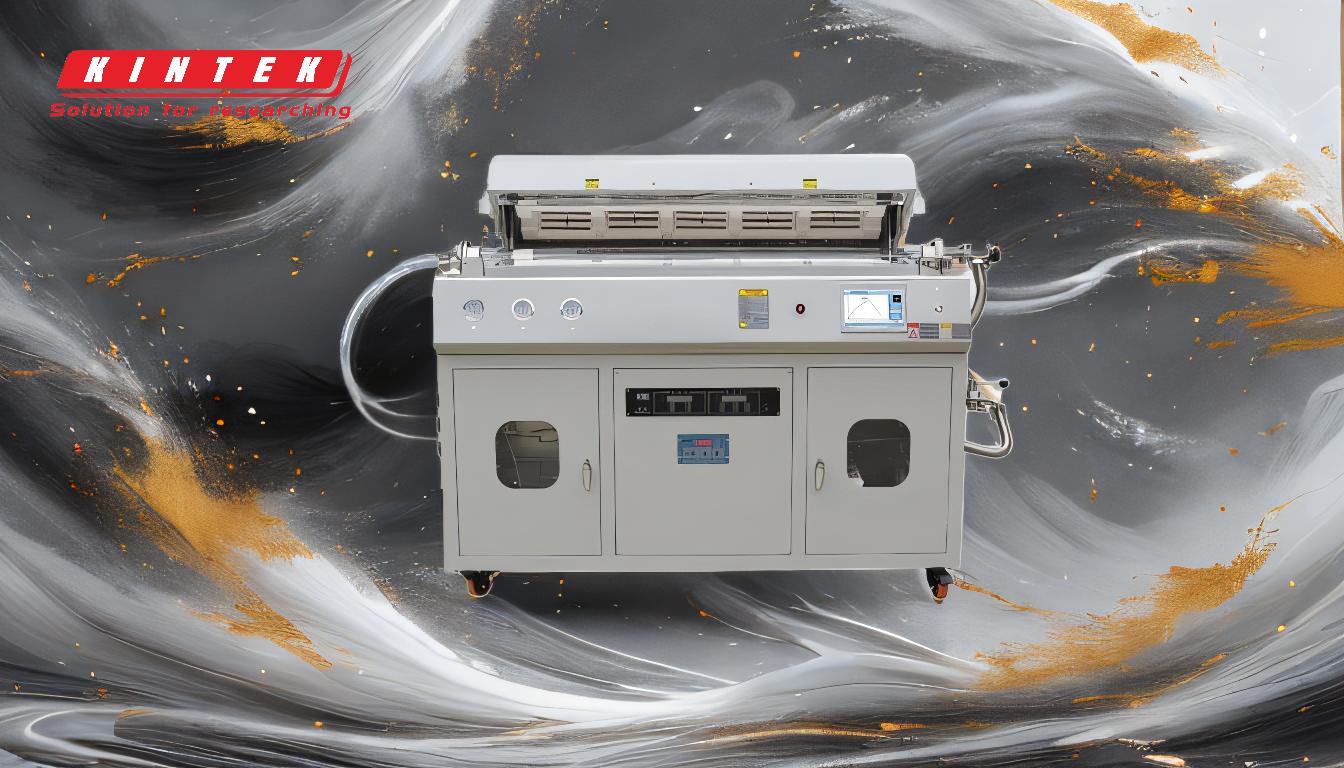
-
Temperature and Heat Delivery Control:
- Furnace operators are responsible for maintaining precise temperature levels within the furnace. This involves adjusting heat delivery systems, such as burners, to ensure consistent and accurate heating. They use controllers to manage these adjustments, ensuring the furnace operates efficiently and meets production requirements.
-
Burner Flame and Air Mixture Management:
- Operators monitor and control the burner flame and air mixture to optimize combustion efficiency. Proper air-to-fuel ratios are critical for achieving complete combustion, reducing emissions, and maximizing energy efficiency. Furnace controllers assist in maintaining these ratios by adjusting the air and fuel inputs based on real-time data.
-
Integration with Sensors and Control Systems:
- Furnace operators rely on inputs from thermocouples and sensors to monitor furnace conditions. These devices provide real-time data on temperature, pressure, and other variables, enabling operators to make informed adjustments. Additionally, furnace controllers can be integrated with broader industrial control systems, allowing for centralized monitoring and control.
-
Monitoring and Optimization of Performance:
- Operators continuously monitor furnace performance to identify and address inefficiencies or malfunctions. This includes analyzing data from sensors and controllers to ensure the furnace operates within specified parameters. They may also perform routine maintenance to prevent downtime and extend the furnace's lifespan.
-
Specialized Monitoring (Carbon Dioxide, Methane, Ammonia):
- Depending on the furnace's application, operators may need to monitor specific gases or chemicals. For example, some furnaces require precise control of carbon dioxide or methane levels, while others involve monitoring ammonia additions for specific processes. Operators use specialized controllers and sensors to manage these variables effectively.
-
Safety and Compliance:
- Furnace operators prioritize safety by ensuring the furnace operates within safe limits and complies with industry regulations. This includes monitoring for potential hazards, such as excessive temperatures or gas leaks, and taking corrective actions as needed. They also ensure that emissions meet environmental standards.
-
Troubleshooting and Problem-Solving:
- When issues arise, furnace operators must diagnose and resolve them quickly to minimize disruptions. This may involve identifying faulty sensors, adjusting control settings, or coordinating with maintenance teams for repairs. Their ability to troubleshoot effectively is critical for maintaining furnace uptime and productivity.
-
Documentation and Reporting:
- Operators maintain detailed records of furnace operations, including temperature logs, maintenance activities, and performance metrics. This documentation helps track trends, identify potential issues, and ensure compliance with operational and regulatory standards.
By mastering these responsibilities, furnace operators ensure the efficient, safe, and reliable operation of industrial furnaces, contributing to the overall success of manufacturing and production processes.
Summary Table:
Responsibility | Key Details |
---|---|
Temperature and Heat Delivery Control | Maintain precise temperature levels using burners and controllers. |
Burner Flame and Air Mixture Management | Optimize combustion efficiency with proper air-to-fuel ratios. |
Integration with Sensors and Control | Use thermocouples and sensors for real-time monitoring and adjustments. |
Monitoring and Optimization | Continuously analyze performance to prevent inefficiencies and malfunctions. |
Specialized Monitoring | Monitor gases like carbon dioxide, methane, or ammonia for specific processes. |
Safety and Compliance | Ensure safe operation and compliance with industry regulations. |
Troubleshooting and Problem-Solving | Diagnose and resolve issues quickly to minimize disruptions. |
Documentation and Reporting | Maintain detailed records for tracking trends and ensuring compliance. |
Need expert guidance on furnace operations? Contact us today to optimize your industrial furnace performance!