Sintering is a manufacturing process that involves compacting and forming a solid mass of material by applying heat and pressure without reaching the material's melting point. This process is crucial in industries like metallurgy, ceramics, and powder metallurgy, where it transforms powdered materials into dense, strong components. The sintering process typically occurs in three stages: shaping the powder blend, removing the bonding agent, and fusing the particles at high temperatures. Advanced sintering techniques, such as vacuum sintering or hot press sintering, further enhance the quality and performance of the final product by preventing oxidation and contamination. The process is widely used in applications ranging from steel production to the creation of advanced ceramics.
Key Points Explained:
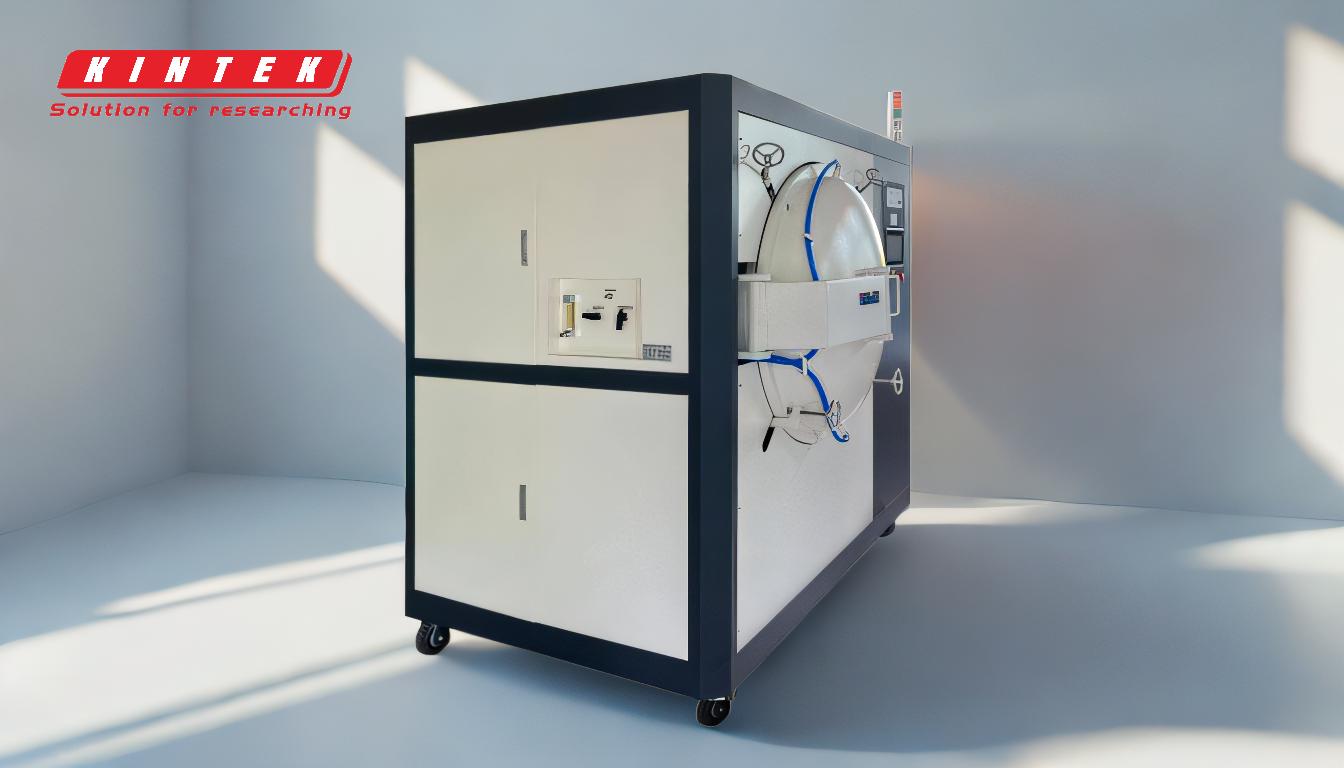
-
Definition and Purpose of Sintering:
- Sintering is a process that uses heat and pressure to compact powdered materials into a solid mass without melting the material. This reduces porosity and increases the material's strength and density.
- It is widely used in industries such as metallurgy, ceramics, and powder metallurgy to create components with precise shapes and properties.
-
Stages of the Sintering Process:
-
Stage 1: Shaping the Powder Blend:
- A primary powder blend is mixed with a bonding agent (e.g., water, wax, or polymer) and formed into the desired shape.
- The bonding agent holds the powder particles together during the initial stages.
-
Stage 2: Removal of the Bonding Agent:
- The shaped "green part" is heated, causing the bonding agent to evaporate or burn away.
- This step prepares the material for particle fusion.
-
Stage 3: Particle Fusion:
- The temperature is increased to a point where the primary particles begin to melt at their surfaces, fusing together.
- In some cases, an intermediate bonding agent (e.g., bronze) melts and binds the particles without altering the primary material.
-
Stage 1: Shaping the Powder Blend:
-
Types of Sintering Furnaces:
-
Vacuum Sintering Furnace:
- This furnace creates a vacuum environment to prevent oxidation and contamination, improving the quality of the sintered product.
- The process involves charging the material, evacuating air, heating, and cooling under controlled conditions. Learn more about sintering furnace.
-
Hot Press Sintering Furnace:
- Combines high temperature and pressure in a vacuum environment to fuse ceramic powders into solid materials.
- The furnace includes a body, heater, pressure system, and vacuum system for precise control.
-
Vacuum Sintering Furnace:
-
Applications of Sintering:
-
Steel Production:
- Sintering is used to create iron lumps from powdered iron ore and coke, which are then processed in blast furnaces to produce steel.
-
Ceramics and Advanced Materials:
- Sintering is essential for creating high-performance ceramics and components with complex shapes.
-
Steel Production:
-
Role of Water in Sintering:
- Water cools the sintered workpiece after treatment in its liquid state.
- As vapor, it combines with evaporated pressing agents and oils to form harmless by-products like CO or CO2, preventing the release of harmful hydrocarbons.
-
Finishing Stage:
- After sintering, parts may undergo additional treatments such as calibration to meet precise specifications.
- Calibration involves adjusting the piece using a calibration die to ensure it meets required tolerances and quality standards.
-
Advantages of Sintering:
- Produces components with high strength, density, and precision.
- Reduces material waste and energy consumption compared to traditional melting processes.
- Enables the creation of complex shapes and advanced materials.
By understanding these key points, equipment and consumable purchasers can make informed decisions about sintering processes and the appropriate furnaces or materials required for their specific applications.
Summary Table:
Key Aspect | Details |
---|---|
Definition | Process of compacting powdered materials using heat and pressure. |
Purpose | Reduces porosity, increases strength, and creates precise shapes. |
Stages | 1. Shaping the powder blend 2. Removing the bonding agent 3. Particle fusion |
Types of Sintering Furnaces | - Vacuum Sintering Furnace - Hot Press Sintering Furnace |
Applications | Steel production, ceramics, and advanced materials. |
Advantages | High strength, reduced waste, and ability to create complex shapes. |
Discover how sintering can benefit your industry—contact our experts today for tailored solutions!