Temperature control is a critical process in various industrial and scientific applications, ensuring that the temperature of a space or substance is maintained at a desired level. It involves measuring or detecting temperature changes and adjusting heat energy flow to achieve the desired temperature. This process is essential for optimizing chemical reactions, maintaining equipment efficiency, and ensuring safety. Temperature control systems often use thermocouples or infrared instruments for measurement and employ automated systems for precise regulation. Proper calibration and maintenance are necessary to ensure accuracy, as electronic components can degrade over time, leading to potential inaccuracies.
Key Points Explained:
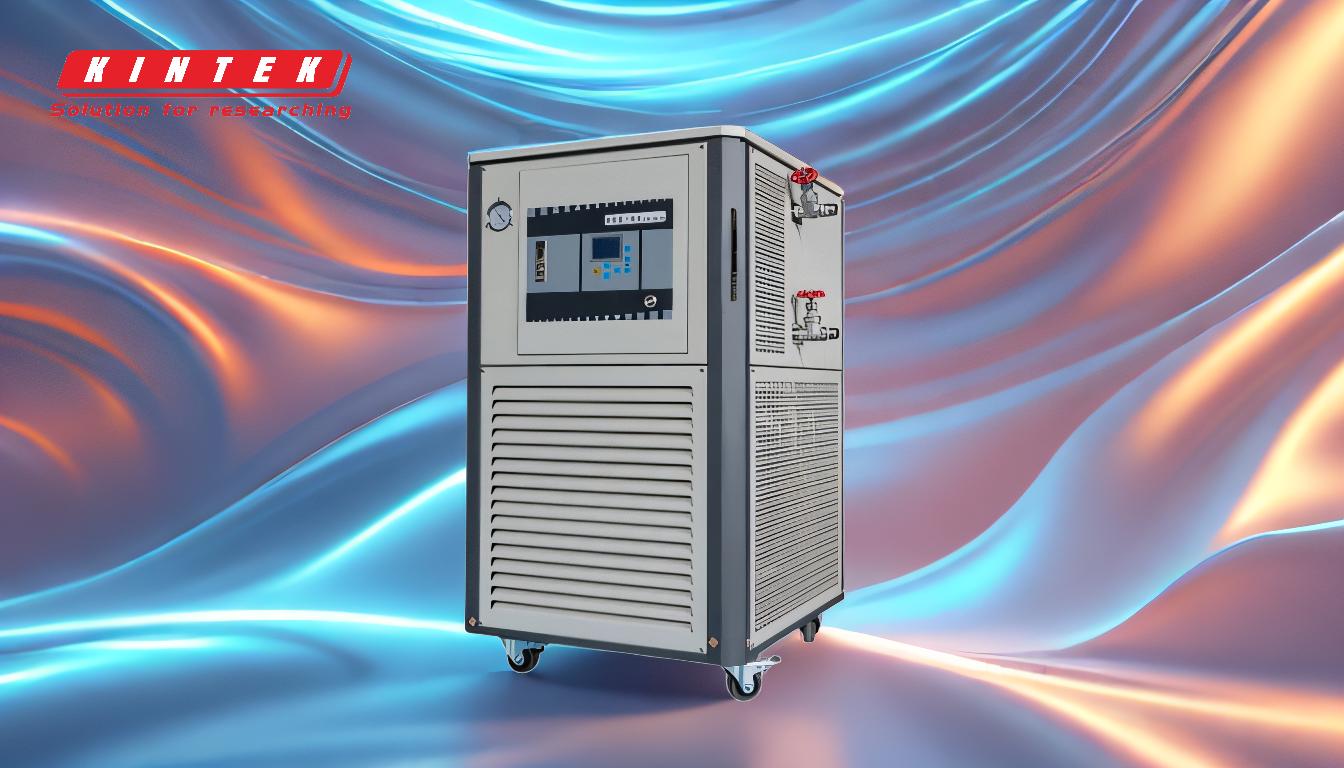
-
Definition and Purpose of Temperature Control:
- Temperature control is the process of maintaining a desired temperature in a space or substance by measuring temperature changes and adjusting heat energy flow.
- It is crucial for optimizing chemical reactions, ensuring equipment efficiency, and maintaining safety in various applications.
-
Measurement Instruments:
- Thermocouples: Used for temperatures below 1700°C. They generate a millivolt signal that is converted into a temperature reading by electronic temperature controllers.
- Infrared Instruments: Used for automatic control of temperatures above 1700°C. These instruments provide non-contact temperature measurement and are suitable for high-temperature applications.
-
Automated Temperature Control Systems:
- Modern systems include automated controls that allow for fast and easy temperature regulation.
- These systems use computer logic and hardware to heat and cool according to a programmed heating cycle, ensuring precise temperature management.
-
High and Low-Temperature Conversion:
- Temperature control systems support automatic conversion between high and low temperatures, providing flexibility in various applications.
- This feature is particularly useful in processes that require different temperature ranges at different stages.
-
Real-Time Monitoring:
- Temperature control systems provide real-time monitoring of furnace conditions, allowing for immediate adjustments if necessary.
- This ensures that the desired temperature is maintained consistently, preventing deviations that could affect the process or product quality.
-
Calibration and Maintenance:
- Proper calibration of temperature control systems is essential for accurate temperature measurement and control.
- Electronic components can degrade over time, leading to potential inaccuracies. Regular maintenance and servicing are required to ensure the system's reliability and accuracy.
-
Importance in Chemical Reactions:
- Temperature regulation is crucial for ensuring that chemical reactions proceed efficiently.
- Automated temperature control systems help optimize reaction rates by maintaining the ideal temperature for the reaction, leading to better yields and product quality.
By understanding these key points, equipment and consumable purchasers can make informed decisions about the temperature control systems they need, ensuring that they select the right tools for their specific applications. Proper selection, calibration, and maintenance of these systems are essential for achieving optimal performance and reliability.
Summary Table:
Key Aspect | Details |
---|---|
Definition | Maintaining desired temperature by measuring changes and adjusting heat flow. |
Purpose | Optimizes reactions, ensures equipment efficiency, and maintains safety. |
Measurement Instruments | Thermocouples (below 1700°C) and infrared instruments (above 1700°C). |
Automated Systems | Fast, precise regulation using computer logic and hardware. |
High/Low-Temperature Conversion | Automatic switching for flexible application needs. |
Real-Time Monitoring | Ensures consistent temperature and prevents deviations. |
Calibration & Maintenance | Essential for accuracy and system reliability. |
Need a reliable temperature control system for your lab or industry? Contact us today to find the perfect solution!