Sintering is a complex process influenced by multiple factors that determine the quality, density, and mechanical properties of the final product. Key factors include temperature, heating rate, applied pressure, particle size, material composition, and the sintering atmosphere. Temperature and heating rate directly affect sintering kinetics and densification, while pressure aids in particle rearrangement and porosity reduction. Smaller particle sizes and homogeneous compositions enhance densification, and the sintering atmosphere (e.g., air, vacuum, or inert gases) plays a critical role in controlling oxidation and material properties. Understanding these factors is essential for optimizing the sintering process to achieve desired product characteristics.
Key Points Explained:
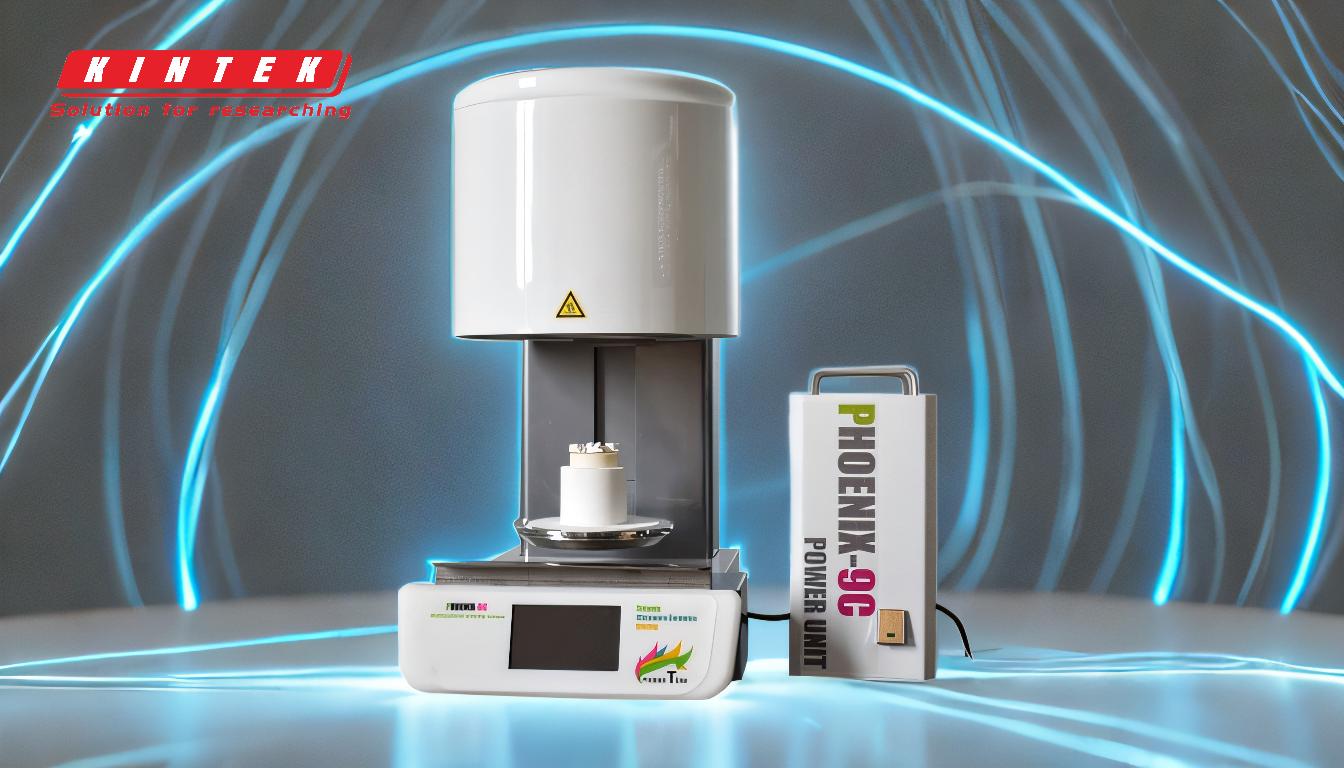
-
Temperature:
- Temperature is a primary factor in sintering, as it directly influences the kinetics of the process and the final material properties.
- Higher temperatures accelerate atomic diffusion, leading to better particle bonding and densification.
- However, excessively high temperatures can cause undesirable grain growth or material degradation, so temperature must be carefully controlled.
-
Heating Rate:
- The rate at which the material is heated affects the densification process.
- A controlled heating rate ensures uniform temperature distribution, preventing thermal stresses and defects.
- Rapid heating may lead to incomplete sintering or uneven densification, while slow heating can improve homogeneity.
-
Applied Pressure:
- Pressure enhances sintering by promoting particle rearrangement and reducing porosity.
- Higher pressures improve particle contact and density, but excessive pressure may cause deformation or cracking.
- Pressure-assisted sintering techniques, such as hot pressing or spark plasma sintering, are often used to achieve high-density materials.
-
Particle Size:
- Smaller particle sizes increase the surface area-to-volume ratio, enhancing sintering kinetics and densification.
- Fine powders sinter more effectively due to shorter diffusion paths and higher driving forces for particle bonding.
- However, very fine particles may agglomerate, requiring additional processing steps to ensure uniformity.
-
Material Composition:
- The composition of the material, including the presence of additives or impurities, significantly impacts sintering behavior.
- Homogeneous compositions promote uniform densification, while heterogeneous compositions may lead to uneven sintering or defects.
- The amount of liquid phase in the material must be carefully controlled, as excessive liquid can cause distortion or poor mechanical properties.
-
Sintering Atmosphere:
- The atmosphere in which sintering occurs (e.g., air, vacuum, argon, nitrogen) affects oxidation, contamination, and material properties.
- Inert atmospheres (e.g., argon or nitrogen) prevent oxidation and are ideal for reactive materials.
- Vacuum sintering reduces gas entrapment and improves density, while air sintering may be suitable for certain oxide materials.
-
Cooling Rate:
- The cooling rate after sintering influences the microstructure and mechanical properties of the material.
- Slow cooling allows for controlled grain growth and stress relief, while rapid cooling may result in residual stresses or phase transformations.
-
Process Techniques:
- The choice of sintering technique (e.g., conventional, hot pressing, spark plasma sintering) depends on the desired product properties and material characteristics.
- Techniques involving electrical currents or pressure can achieve higher densities and improved mechanical properties compared to conventional sintering.
By carefully controlling these factors, manufacturers can optimize the sintering process to produce materials with the desired density, strength, and performance characteristics. The interplay between these variables requires a thorough understanding of the material and process parameters to achieve consistent and high-quality results.
Summary Table:
Factor | Impact on Sintering | Key Considerations |
---|---|---|
Temperature | Influences kinetics, densification, and material properties | Avoid excessive temperatures to prevent grain growth or degradation |
Heating Rate | Affects uniformity and densification | Controlled heating prevents thermal stresses and defects |
Applied Pressure | Enhances particle rearrangement and reduces porosity | Excessive pressure may cause deformation or cracking |
Particle Size | Smaller particles improve densification and sintering kinetics | Fine powders may agglomerate, requiring additional processing |
Material Composition | Homogeneous compositions promote uniform densification | Impurities or additives can lead to defects or uneven sintering |
Sintering Atmosphere | Controls oxidation, contamination, and material properties | Inert atmospheres or vacuum reduce oxidation and improve density |
Cooling Rate | Influences microstructure and mechanical properties | Slow cooling reduces residual stresses and allows controlled grain growth |
Process Techniques | Determines final density and mechanical properties | Techniques like hot pressing or spark plasma sintering yield high-density materials |
Optimize your sintering process with expert guidance—contact us today to achieve superior material properties!