Sintering is a critical process in metallurgy that transforms powdered metals into solid, durable components by heating them below their melting point. This process enhances the material's mechanical properties, such as strength and durability, by bonding powder grains through diffusion, reducing porosity, and achieving densification. The sintering process involves several stages, including heating, compacting, and cooling, which are carefully controlled to ensure the final product meets desired specifications. Understanding the sintering process is essential for optimizing material properties and avoiding defects such as warping or sagging.
Key Points Explained:
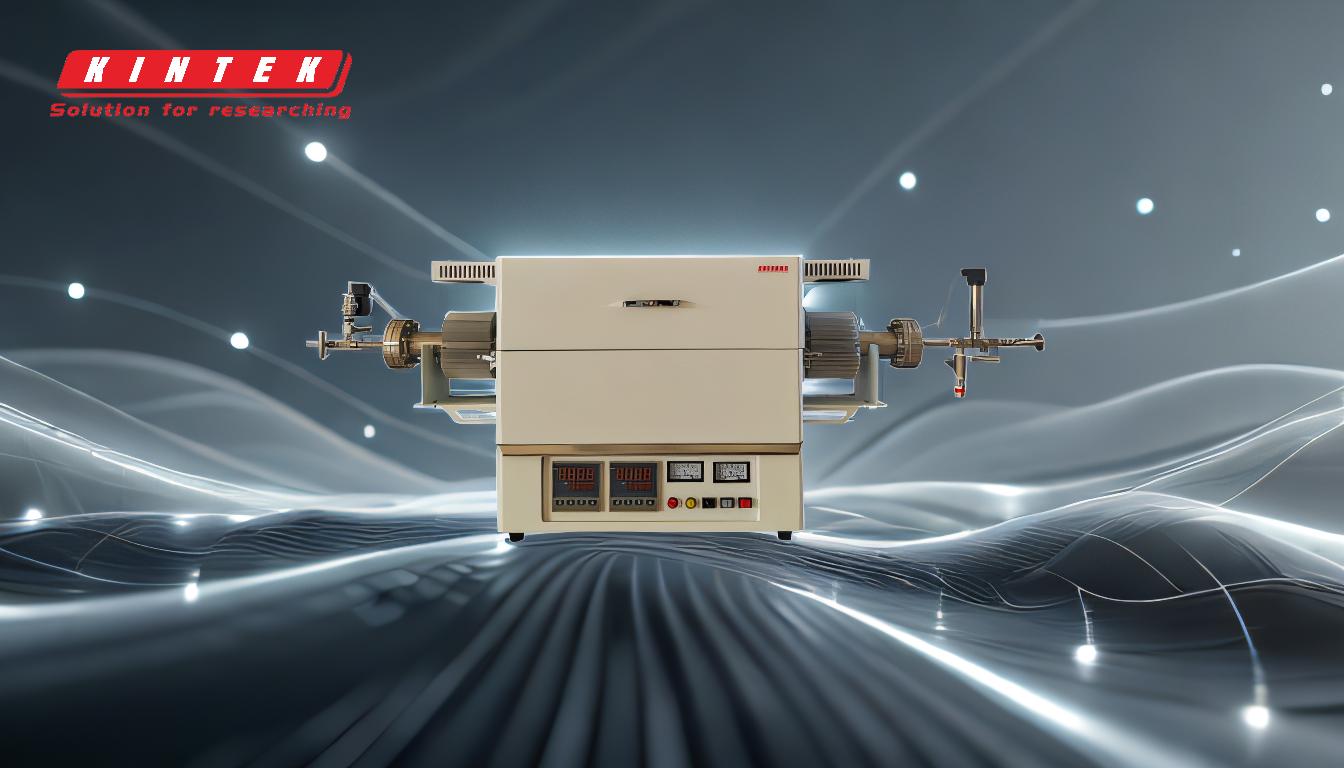
-
Microstructural Changes During Sintering:
- Sintering directly impacts the grain size, pore size, and grain boundary distribution in the material's microstructure. These changes are crucial for determining the material's mechanical properties, such as strength and durability. For example, reducing pore size and closing pores during sintering leads to densification, which improves the material's overall performance.
-
Stages of the Sintering Process:
- The sintering process involves multiple stages, including:
- Removing Lubricants: Lubricants added during blending are burned off to prevent contamination.
- Reducing Oxides: Oxides on the powder surfaces are reduced to enhance bonding.
- Bonding Particles: Powder grains bond through diffusion at high temperatures, forming a solid structure.
- Cooling: Controlled cooling rates are used to fine-tune the material's final properties, such as hardness and toughness.
- The sintering process involves multiple stages, including:
-
Role of Temperature and Atmosphere:
- Sintering is performed in a sintering furnace at temperatures below the melting point of the main metal. A controlled atmosphere (e.g., hydrogen or nitrogen) is used to prevent oxidation and ensure proper bonding. This environment allows the powder grains to diffuse and bond without melting, resulting in a strong, cohesive structure.
-
Densification and Shrinkage:
- During sintering, the pores in the "green compact" diminish or close up, leading to densification. This process also causes shrinkage, which gives the part its final dimensions. Proper control of sintering parameters ensures that the shrinkage is uniform and predictable, avoiding defects.
-
Material Blending and Preparation:
- Before sintering, powdered metals are blended with alloying elements and additives to achieve specific material properties. A solid lubricant is added to reduce friction during compaction. This step ensures a uniform mixture, which is critical for consistent sintering results.
-
Potential Defects and Challenges:
- Issues such as warping or sagging can occur during sintering due to gravity or uneven heating. These defects can compromise the final part's integrity. Proper design of the sintering process, including support structures and controlled heating rates, helps mitigate these risks.
-
Applications and Benefits:
- Sintering is widely used in industries such as automotive, aerospace, and electronics to produce complex, high-strength components. The process offers benefits such as cost efficiency, material versatility, and the ability to create near-net-shape parts with minimal waste.
By understanding these key points, manufacturers can optimize the sintering process to produce high-quality metal components with enhanced mechanical properties. Proper control of temperature, atmosphere, and cooling rates, along with careful preparation of the powder mixture, ensures successful sintering and minimizes defects.
Summary Table:
Key Aspect | Description |
---|---|
Microstructural Changes | Reduces pore size, closes pores, and improves grain boundary distribution. |
Stages of Sintering | Removes lubricants, reduces oxides, bonds particles, and controls cooling. |
Temperature & Atmosphere | Performed below melting point in controlled atmospheres (e.g., hydrogen, nitrogen). |
Densification & Shrinkage | Pores diminish, leading to densification and uniform shrinkage for final dimensions. |
Material Preparation | Powdered metals blended with additives and lubricants for uniformity. |
Potential Defects | Warping or sagging due to uneven heating; mitigated by proper process design. |
Applications | Used in automotive, aerospace, and electronics for high-strength components. |
Optimize your sintering process for superior metal components—contact our experts today!