The acronym CVD stands for Chemical Vapor Deposition (or Chemical Vapour Deposition, depending on regional spelling preferences). It is a widely used process in materials science and engineering to create thin films or coatings on a substrate by depositing material from a chemical vapor. This method is particularly significant in the production of synthetic diamonds, semiconductor devices, and various electronic components. CVD involves exposing a substrate to volatile precursors, which react or decompose on the substrate surface to form the desired material. The process is conducted under controlled conditions of temperature and pressure, often in a vacuum chamber, to ensure precision and quality.
Key Points Explained:
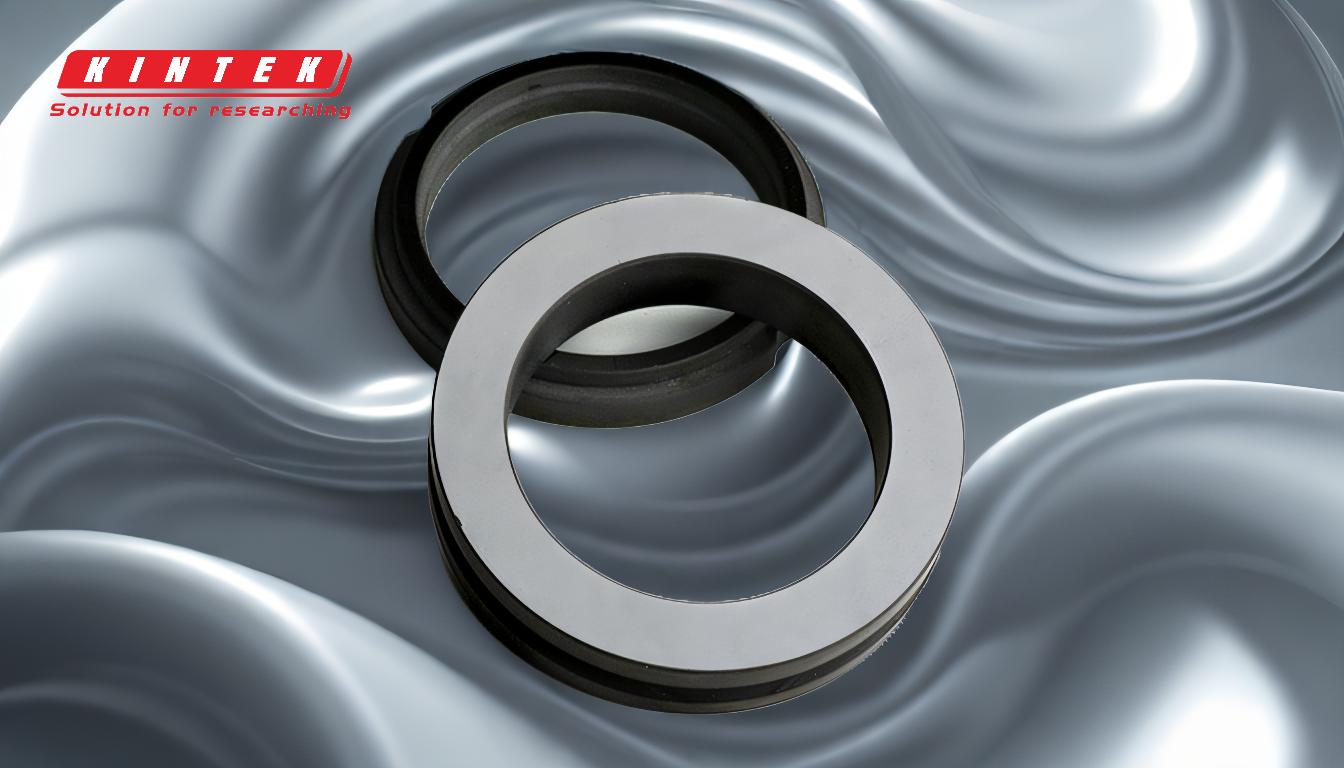
-
Definition of CVD:
- CVD stands for Chemical Vapor Deposition (or Chemical Vapour Deposition).
- It is a process used to deposit thin films or coatings onto a substrate by utilizing chemical reactions in a vapor phase.
-
Applications of CVD:
- Synthetic Diamond Production: CVD is a key method for growing diamonds in laboratory settings. It involves exposing hydrocarbon gases to moderate temperatures and pressures in a vacuum chamber, allowing carbon atoms to deposit and form diamond structures.
- Semiconductor Fabrication: CVD is critical in the production of electronic devices, where it is used to deposit thin films of materials like silicon, silicon dioxide, and other semiconductors onto substrates.
- Thin Film Coatings: The process is also used to create protective or functional coatings on various materials, enhancing their properties such as durability, conductivity, or resistance to corrosion.
-
Process Mechanism:
- Chemical Reactions: In CVD, volatile precursors (gases or vapors) are introduced into a reaction chamber. These precursors react or decompose on the surface of the substrate, forming a solid material that adheres to the substrate.
- Controlled Environment: The process typically occurs in a vacuum or low-pressure environment to ensure precise control over the deposition conditions, including temperature, pressure, and gas composition.
-
Advantages of CVD:
- High Purity: CVD allows for the deposition of high-purity materials, which is essential for applications like semiconductor manufacturing and synthetic diamond production.
- Uniformity: The process can produce highly uniform coatings, even on complex geometries, making it suitable for a wide range of industrial applications.
- Versatility: CVD can be used to deposit a variety of materials, including metals, ceramics, and polymers, making it a versatile technology.
-
Challenges and Considerations:
- Cost and Complexity: CVD equipment and processes can be expensive and require precise control, making it less accessible for smaller-scale applications.
- Safety: The use of volatile and sometimes hazardous chemicals necessitates strict safety protocols to protect operators and the environment.
-
Comparison with Other Deposition Methods:
- Physical Vapor Deposition (PVD): Unlike CVD, PVD involves the physical transfer of material (e.g., through sputtering or evaporation) rather than chemical reactions. PVD is often used for metallic coatings but may not achieve the same level of purity or uniformity as CVD.
- Atomic Layer Deposition (ALD): ALD is a more precise but slower process compared to CVD, often used for ultra-thin films in advanced semiconductor applications.
In summary, CVD is a fundamental technology in modern materials science, enabling the production of high-quality thin films and coatings for a wide range of applications, from synthetic diamonds to advanced electronics. Its ability to produce uniform, high-purity materials under controlled conditions makes it indispensable in many high-tech industries.
Summary Table:
Aspect | Details |
---|---|
Definition | CVD stands for Chemical Vapor Deposition, a process for depositing thin films. |
Applications | - Synthetic Diamond Production - Semiconductor Fabrication - Thin Film Coatings |
Process Mechanism | - Chemical reactions in a controlled environment - Precise temperature and pressure control |
Advantages | - High purity - Uniform coatings - Versatility in material deposition |
Challenges | - High cost and complexity - Requires strict safety protocols |
Comparison with PVD | PVD involves physical transfer, while CVD uses chemical reactions for deposition. |
Comparison with ALD | ALD is slower but more precise, ideal for ultra-thin films. |
Interested in leveraging CVD technology for your projects? Contact us today to learn more!