CVD stands for Chemical Vapor Deposition, a process used to deposit thin solid films onto a substrate by reacting gaseous chemicals. This method is widely used in various industries, including semiconductor manufacturing, optics, and surface coating. The process involves introducing gaseous reactants into a reaction chamber, where they decompose or react at elevated temperatures to form a solid film on the substrate. The substrate's temperature, gas flow rates, and chamber conditions are carefully controlled to ensure the desired film properties. CVD is valued for its ability to produce high-quality, uniform coatings with precise thickness and composition.
Key Points Explained:
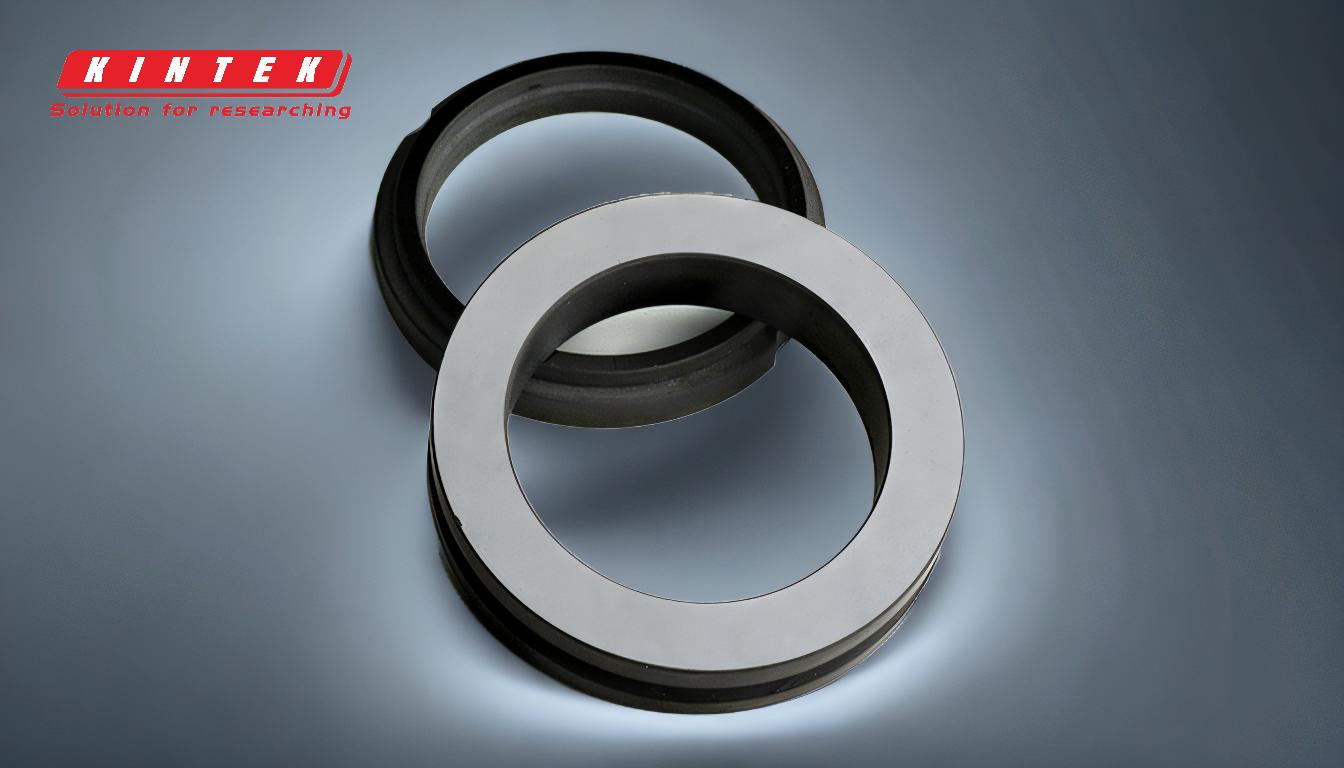
-
Definition of CVD:
- CVD stands for Chemical Vapor Deposition, a process where gaseous reactants are used to form a thin solid film on a substrate. This method is essential in industries requiring high-precision coatings, such as semiconductors and optics.
-
Process Overview:
- The CVD process involves several key steps:
- Gas Delivery: Gaseous reactants are introduced into a reaction chamber.
- Reaction: The gases react or decompose on the substrate surface, forming a solid film.
- Energy Supply: Heat is applied to facilitate the chemical reaction and control the substrate temperature.
- Exhaust: Unreacted gases and by-products are removed from the chamber.
- The CVD process involves several key steps:
-
Components of a CVD System:
- Gas Delivery System: Controls the flow of gases into the reaction chamber.
- Reaction Chamber: The environment where the chemical reaction occurs.
- Substrate Loading Mechanism: Holds and positions the substrate for coating.
- Energy Supplier: Provides the necessary heat or energy for the reaction.
- Vacuum System: Maintains a controlled environment, often under vacuum, to ensure proper deposition.
-
Importance of Substrate Temperature:
- The temperature of the substrate is critical in the CVD process. It affects the rate of the chemical reaction, the quality of the deposited film, and the adhesion of the film to the substrate. Precise temperature control is necessary to achieve the desired film properties.
-
Applications of CVD:
- CVD is used in various applications, including:
- Semiconductor Manufacturing: For depositing thin films of silicon, silicon nitride, and other materials.
- Optics: For creating anti-reflective coatings and other optical films.
- Surface Coating: For enhancing the durability and performance of materials.
- CVD is used in various applications, including:
-
Advantages of CVD:
- High-Quality Films: CVD produces films with excellent uniformity, purity, and adherence.
- Versatility: It can deposit a wide range of materials, including metals, ceramics, and polymers.
- Precision: Allows for precise control over film thickness and composition.
-
Challenges in CVD:
- Complexity: The process requires precise control of multiple parameters, including temperature, gas flow, and pressure.
- Cost: The equipment and energy requirements can be expensive.
- Safety: Handling reactive gases and high temperatures requires stringent safety measures.
In summary, CVD is a versatile and precise method for depositing thin films, essential in many high-tech industries. Its ability to produce high-quality, uniform coatings makes it a valuable process despite its complexity and cost.
Summary Table:
Aspect | Details |
---|---|
Definition | CVD stands for Chemical Vapor Deposition, a process for depositing thin films. |
Process Steps | Gas Delivery, Reaction, Energy Supply, Exhaust. |
Key Components | Gas Delivery System, Reaction Chamber, Substrate Loading, Energy Supplier. |
Applications | Semiconductor Manufacturing, Optics, Surface Coating. |
Advantages | High-quality films, versatility, precision. |
Challenges | Complexity, cost, safety requirements. |
Interested in leveraging CVD for your industry? Contact us today to learn more!