Brazing is a metal-joining process that involves heating a filler metal above its melting point and distributing it between two or more close-fitting parts by capillary action. The key distinction between brazing and other joining processes, such as soldering, lies in the temperature at which the process occurs. To be considered brazing, the temperature must exceed 450°C (842°F). This temperature threshold ensures that the filler metal melts and flows into the joint without melting the base metals, creating a strong and durable bond. The process is widely used in industries such as automotive, aerospace, and HVAC due to its ability to join dissimilar metals and produce high-strength joints.
Key Points Explained:
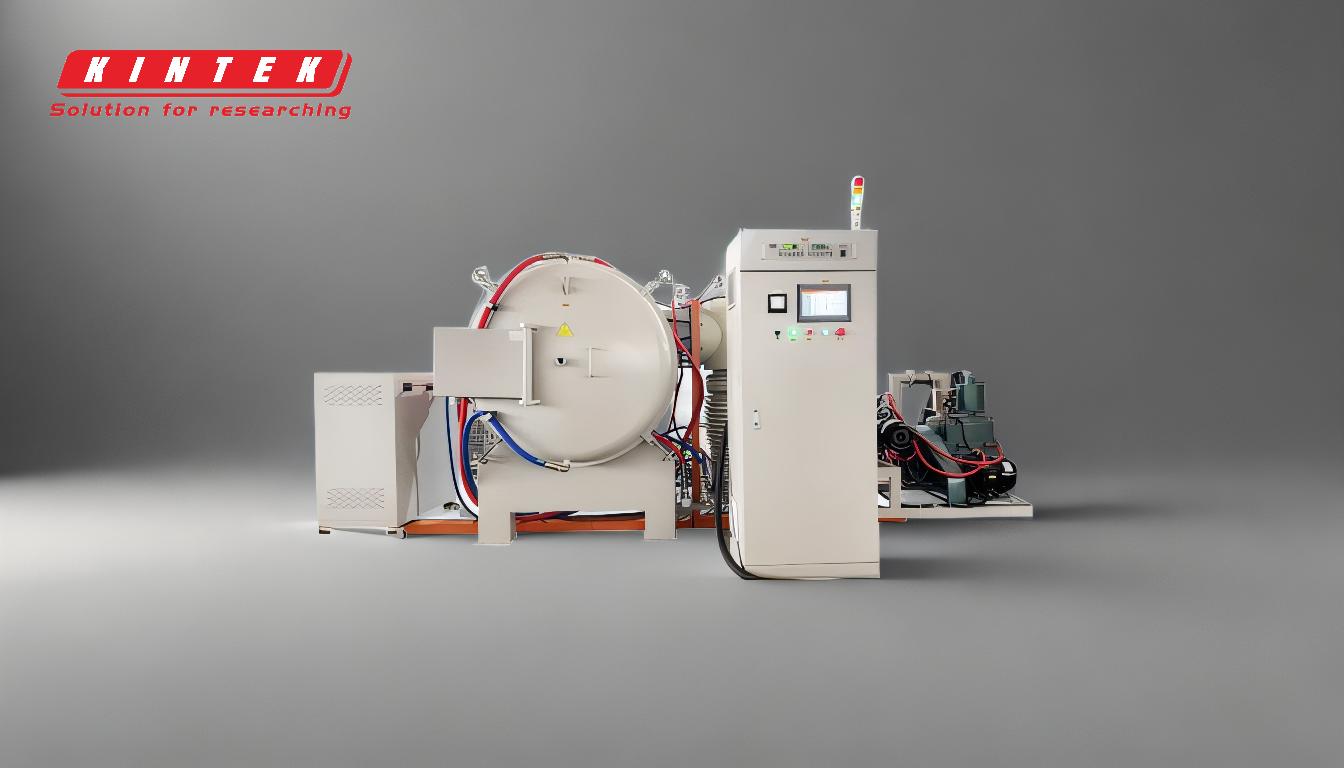
-
Definition of Brazing:
- Brazing is a metal-joining process where a filler metal is heated above its melting point and flows into the joint between two or more base metals by capillary action. Unlike welding, the base metals do not melt during brazing, which allows for the joining of dissimilar materials with minimal distortion.
-
Temperature Threshold for Brazing:
- The critical temperature that distinguishes brazing from other joining processes, such as soldering, is 450°C (842°F). Any metal-joining process occurring above this temperature is classified as brazing. Below this temperature, the process is typically referred to as soldering.
- This high-temperature requirement ensures that the filler metal melts and flows effectively into the joint, creating a strong bond without compromising the integrity of the base metals.
-
Importance of Temperature Control:
- Temperature control is crucial in brazing to ensure that the filler metal melts and flows properly while the base metals remain solid. Exceeding the melting point of the base metals can lead to structural weaknesses or deformation.
- Precise temperature management also helps in achieving consistent joint quality and preventing defects such as voids or incomplete bonding.
-
Applications of Brazing:
- Brazing is widely used in industries that require strong, durable, and leak-proof joints. Examples include:
- Automotive Industry: Joining components such as heat exchangers, radiators, and fuel systems.
- Aerospace Industry: Assembling critical components like turbine blades and structural elements.
- HVAC Systems: Creating reliable connections in refrigeration and air conditioning systems.
- The ability to join dissimilar metals makes brazing particularly valuable in applications where different materials must be combined for optimal performance.
- Brazing is widely used in industries that require strong, durable, and leak-proof joints. Examples include:
-
Advantages of Brazing:
- Strength: Brazed joints are typically stronger than soldered joints due to the higher temperatures and the metallurgical bonding that occurs.
- Versatility: Brazing can join a wide range of materials, including metals with different melting points.
- Aesthetic Appeal: The process produces clean, smooth joints with minimal distortion, making it ideal for applications where appearance is important.
- Durability: Brazed joints are resistant to vibration and thermal cycling, ensuring long-term reliability.
-
Comparison with Soldering:
- While both brazing and soldering involve the use of a filler metal to join materials, the key difference lies in the temperature. Soldering occurs at temperatures below 450°C (842°F), making it suitable for applications where lower heat is required, such as electronics assembly.
- Brazing, on the other hand, is preferred for applications requiring higher strength and durability, as the higher temperatures facilitate better metallurgical bonding.
-
Equipment and Consumables for Brazing:
- Brazing Torches: Used to apply heat to the joint area. These can be fueled by gases such as acetylene, propane, or natural gas.
- Filler Metals: Commonly used filler metals include silver, copper, and aluminum alloys, chosen based on the base metals and application requirements.
- Fluxes: Applied to the joint area to prevent oxidation and promote wetting of the filler metal.
- Furnaces: For large-scale or precision brazing, controlled-atmosphere furnaces are used to ensure consistent heating and cooling.
By understanding these key points, equipment and consumable purchasers can make informed decisions about the materials and tools needed for brazing applications, ensuring optimal results and cost-effectiveness.
Summary Table:
Key Aspect | Details |
---|---|
Temperature Threshold | Above 450°C (842°F) to be classified as brazing. |
Base Metals | Remain solid; only the filler metal melts. |
Applications | Automotive, aerospace, HVAC systems. |
Advantages | Strong joints, versatility, aesthetic appeal, and durability. |
Comparison to Soldering | Soldering occurs below 450°C; brazing offers higher strength and durability. |
Ready to optimize your brazing process? Contact our experts today for tailored solutions!