Brazing in HVAC (Heating, Ventilation, and Air Conditioning) systems is a critical process for joining metal components, ensuring leak-proof and durable connections. The choice of gas used during brazing is essential to achieve high-quality joints, prevent oxidation, and maintain the integrity of the materials. The most commonly used gases for HVAC brazing are nitrogen and inert gases like argon. These gases act as shielding agents, protecting the metal surfaces from oxidation and contamination during the heating process. Nitrogen is particularly favored due to its cost-effectiveness and effectiveness in creating an oxygen-free environment, which is crucial for achieving strong and clean brazed joints.
Key Points Explained:
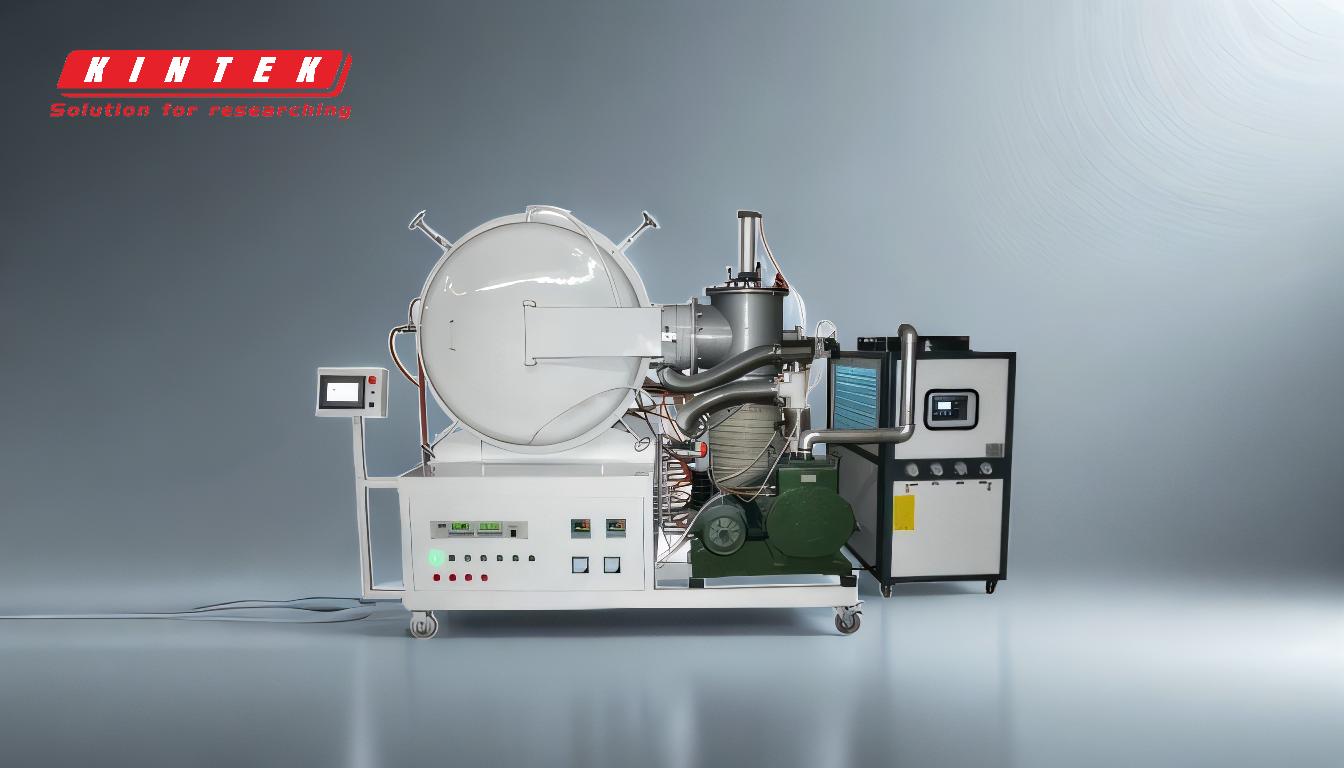
-
Purpose of Gas in HVAC Brazing:
- The primary purpose of using gas during HVAC brazing is to create an inert atmosphere that prevents oxidation of the metal surfaces. Oxidation can weaken the joint and lead to leaks or failures in the HVAC system.
- Gases like nitrogen and argon displace oxygen, ensuring that the metal remains clean and free from contaminants during the brazing process.
-
Nitrogen as the Preferred Gas:
- Nitrogen is the most commonly used gas for HVAC brazing due to its affordability and effectiveness. It is readily available and provides excellent shielding properties.
- When nitrogen is introduced into the HVAC system during brazing, it purges the system of oxygen, preventing the formation of oxides on the metal surfaces.
-
Inert Gases (Argon):
- In some cases, argon is used as an alternative to nitrogen, especially in applications where higher purity is required. Argon is an inert gas, meaning it does not react with the metal surfaces, ensuring a clean and oxidation-free environment.
- However, argon is more expensive than nitrogen, making it less commonly used in standard HVAC brazing applications.
-
Process of Using Gas in HVAC Brazing:
- During the brazing process, the gas is introduced into the HVAC system through a purge line. This ensures that the interior of the pipes and joints is filled with the inert gas, displacing any oxygen.
- The gas flow is maintained throughout the heating and cooling phases to ensure continuous protection against oxidation.
-
Benefits of Using Gas in HVAC Brazing:
- Improved Joint Quality: The use of gas ensures that the brazed joints are strong, leak-proof, and free from defects caused by oxidation.
- Longer System Lifespan: By preventing oxidation, the use of gas during brazing extends the lifespan of the HVAC system, reducing the need for repairs and maintenance.
- Enhanced Performance: Clean, oxidation-free joints contribute to the overall efficiency and performance of the HVAC system.
-
Safety Considerations:
- When using gases like nitrogen or argon, it is important to ensure proper ventilation in the workspace to prevent the accumulation of gas, which could pose a safety hazard.
- Proper handling and storage of gas cylinders are also essential to prevent accidents and ensure the safety of the technicians performing the brazing.
-
Cost Considerations:
- While nitrogen is more cost-effective than argon, the choice of gas may also depend on the specific requirements of the HVAC system and the brazing process.
- In some cases, the use of argon may be justified by the need for higher purity and better performance in critical applications.
In summary, nitrogen is the most commonly used gas for HVAC brazing due to its cost-effectiveness and ability to create an oxygen-free environment. Argon is used in more specialized applications where higher purity is required. The use of these gases ensures high-quality, durable, and leak-proof joints, contributing to the overall performance and longevity of HVAC systems.
Summary Table:
Gas Type | Key Benefits | Common Use Cases |
---|---|---|
Nitrogen | Cost-effective, creates oxygen-free environment, prevents oxidation | Standard HVAC brazing applications |
Argon | Higher purity, inert, ensures clean and oxidation-free environment | Specialized or critical HVAC brazing needs |
Need help choosing the right gas for your HVAC brazing process? Contact our experts today for personalized advice!