Heat treatment processes rely on a variety of gases to achieve desired material properties, such as hardness, ductility, and resistance to wear and corrosion. These gases are chosen based on their chemical properties, reactivity, and the specific requirements of the heat treatment process. Commonly used gases include hydrogen, nitrogen, oxygen, helium, argon, carbon monoxide, carbon dioxide, ammonia, propane, methane, and butane. Each gas serves a unique purpose, such as preventing oxidation, enabling carburization, or providing an inert atmosphere. The choice of gas depends on factors like material type, temperature, and the desired outcome of the heat treatment process.
Key Points Explained:
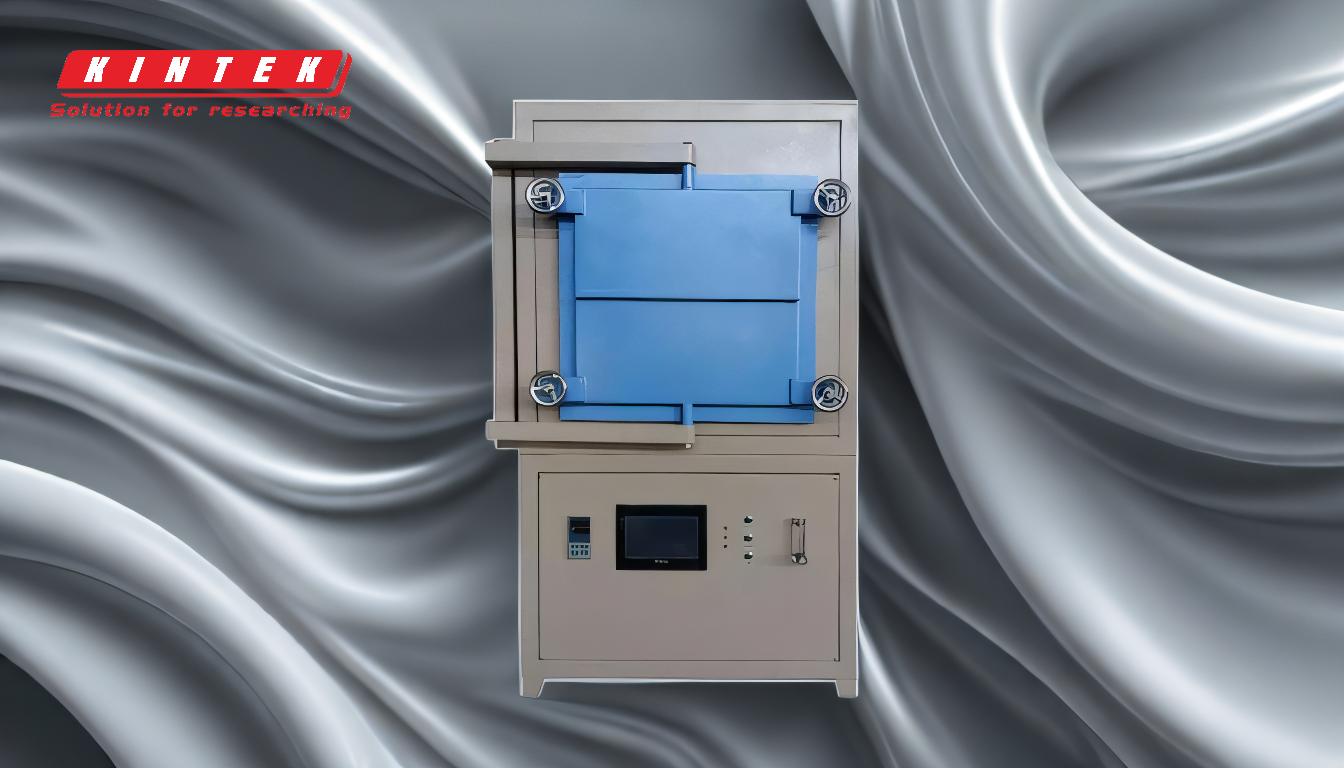
-
Hydrogen (H₂)
- Role: Hydrogen is often used as a reducing agent to prevent oxidation and remove oxides from metal surfaces.
- Applications: It is commonly used in annealing and sintering processes, particularly for stainless steels and other alloys.
- Considerations: Hydrogen is highly flammable and requires careful handling to ensure safety.
-
Nitrogen (N₂)
- Role: Nitrogen is an inert gas that provides a protective atmosphere, preventing oxidation and decarburization.
- Applications: It is widely used in annealing, neutral quenching, and brazing processes.
- Considerations: Nitrogen is cost-effective and readily available, making it a popular choice for many heat treatment applications.
-
Oxygen (O₂)
- Role: Oxygen is highly reactive and is used in controlled amounts for processes like decarburization and surface oxidation.
- Applications: It is used in specific heat treatment processes where surface modification is required.
- Considerations: Excessive oxygen can lead to unwanted oxidation and decarburization, so precise control is essential.
-
Helium (He)
- Role: Helium is an inert gas used to create a non-reactive atmosphere, particularly in high-temperature processes.
- Applications: It is used in processes like brazing and heat treatment of reactive metals.
- Considerations: Helium is expensive and less commonly used compared to nitrogen and argon.
-
Argon (Ar)
- Role: Argon is another inert gas that provides a protective atmosphere, preventing oxidation and other chemical reactions.
- Applications: It is used in annealing, sintering, and brazing, especially for materials that are highly reactive.
- Considerations: Argon is more expensive than nitrogen but is preferred for processes involving reactive metals.
-
Carbon Monoxide (CO)
- Role: Carbon monoxide is used in carburizing processes to introduce carbon into the surface of steel, increasing hardness.
- Applications: It is commonly used in case hardening and carburizing processes.
- Considerations: Carbon monoxide is toxic and requires careful handling and ventilation.
-
Carbon Dioxide (CO₂)
- Role: Carbon dioxide is used in controlled atmospheres to regulate carbon content and prevent oxidation.
- Applications: It is used in processes like annealing and tempering.
- Considerations: Carbon dioxide is less reactive than oxygen and is often used in combination with other gases.
-
Ammonia (NH₃)
- Role: Ammonia is used in nitriding processes to introduce nitrogen into the surface of metals, increasing hardness and wear resistance.
- Applications: It is primarily used in nitriding and nitrocarburizing processes.
- Considerations: Ammonia is toxic and requires careful handling and proper ventilation.
-
Propane (C₃H₈), Methane (CH₄), and Butane (C₄H₁₀)
- Role: These hydrocarbons are used as carbon sources in carburizing and carbonitriding processes.
- Applications: They are used to increase the carbon content of steel surfaces, enhancing hardness and wear resistance.
- Considerations: These gases are flammable and require careful control of the atmosphere to prevent explosions.
-
Water Vapor (H₂O)
- Role: Water vapor is used in controlled atmospheres to regulate oxidation and decarburization.
- Applications: It is used in processes like tempering and annealing.
- Considerations: The amount of water vapor must be carefully controlled to avoid excessive oxidation.
-
Acetylene (C₂H₂)
- Role: Acetylene is used in certain heat treatment processes for its high carbon content.
- Applications: It is used in specialized carburizing processes.
- Considerations: Acetylene is highly flammable and requires careful handling.
-
Gas Mixtures
- Role: Gas mixtures are often used to achieve specific atmospheric conditions, such as a balance between oxidation and reduction.
- Applications: Mixtures of nitrogen and hydrogen, or nitrogen and carbon dioxide, are commonly used in annealing and brazing.
- Considerations: The composition of the gas mixture must be carefully controlled to achieve the desired results.
In summary, the choice of gas or gas mixture in heat treatment depends on the specific requirements of the process, including the type of material being treated, the desired outcome, and safety considerations. Each gas has unique properties that make it suitable for particular applications, and understanding these properties is crucial for achieving optimal results in heat treatment processes.
Summary Table:
Gas | Role | Applications | Considerations |
---|---|---|---|
Hydrogen (H₂) | Reducing agent, prevents oxidation | Annealing, sintering | Highly flammable, handle carefully |
Nitrogen (N₂) | Inert gas, prevents oxidation | Annealing, neutral quenching, brazing | Cost-effective, widely available |
Oxygen (O₂) | Reactive, used for surface modification | Decarburization, surface oxidation | Requires precise control |
Helium (He) | Inert gas for high-temperature processes | Brazing, reactive metals | Expensive, less common |
Argon (Ar) | Inert gas, prevents oxidation | Annealing, sintering, brazing | More expensive than nitrogen |
Carbon Monoxide (CO) | Introduces carbon, increases hardness | Case hardening, carburizing | Toxic, requires ventilation |
Carbon Dioxide (CO₂) | Regulates carbon, prevents oxidation | Annealing, tempering | Less reactive, often mixed |
Ammonia (NH₃) | Introduces nitrogen, increases hardness | Nitriding, nitrocarburizing | Toxic, requires ventilation |
Propane, Methane, Butane | Carbon sources for carburizing | Carburizing, carbonitriding | Flammable, requires control |
Water Vapor (H₂O) | Regulates oxidation, decarburization | Tempering, annealing | Must be carefully controlled |
Acetylene (C₂H₂) | High carbon content for carburizing | Specialized carburizing | Highly flammable |
Gas Mixtures | Achieves specific atmospheric conditions | Annealing, brazing | Composition must be controlled |
Need help selecting the right gas for your heat treatment process? Contact our experts today for tailored solutions!