When proper clearance is not maintained between joints during brazing, the capillary action necessary for effective filler metal distribution is compromised. This can lead to incomplete or weak joints, reducing the overall strength and reliability of the brazed connection. The ideal clearance for most brazing applications is typically less than 0.1mm to ensure optimal capillary flow and joint integrity. If the gap is too wide, the filler metal may not flow properly, resulting in voids or weak spots. Conversely, if the gap is too narrow, the filler metal may not penetrate adequately, also leading to weak joints. Proper joint design, including maintaining the correct clearance, is essential for achieving strong and durable brazed connections.
Key Points Explained:
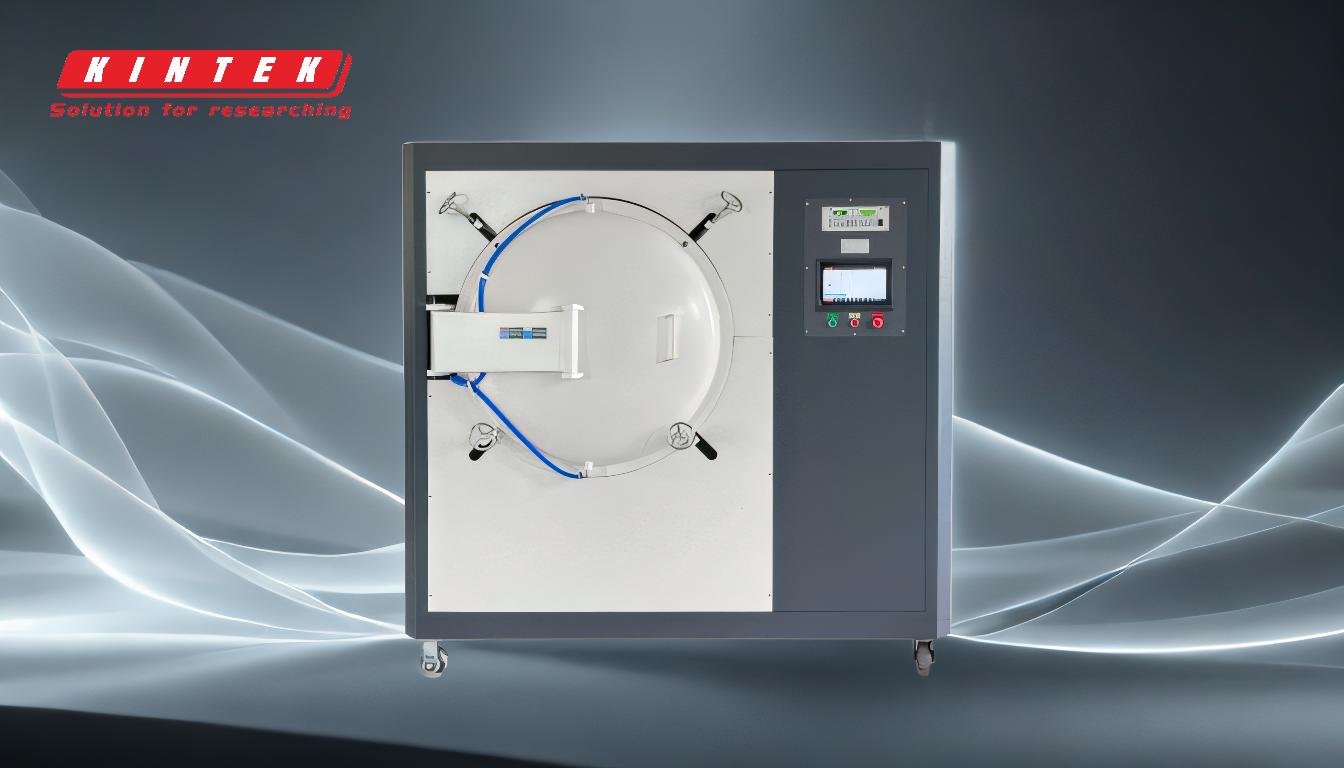
-
Capillary Action in Brazing:
- Brazing relies heavily on capillary action to draw the molten filler metal into the joint. This process requires a specific gap size, usually less than 0.1mm, to ensure the filler metal flows evenly and completely fills the joint.
- If the clearance is not maintained within this range, the capillary action is disrupted, leading to poor filler metal distribution.
-
Impact of Excessive Clearance:
- Incomplete Filling: When the gap between joints is too wide, the filler metal may not be drawn into the joint effectively, resulting in incomplete filling. This creates voids or weak spots within the joint.
- Reduced Joint Strength: Incomplete filling compromises the mechanical strength of the joint, making it more susceptible to failure under stress or load.
-
Impact of Insufficient Clearance:
- Inadequate Penetration: If the gap is too narrow, the filler metal may not penetrate the joint adequately. This can also lead to weak spots and a lack of bonding between the surfaces.
- Increased Risk of Cracking: Insufficient clearance can cause stress concentrations at the joint, increasing the risk of cracking during or after the brazing process.
-
Importance of Joint Design:
- Self-Supporting Joints: Ideally, joints should be designed to be self-supporting or self-jigging. This minimizes the need for external fixtures, which can be expensive and may introduce additional variables that affect the brazing process.
- Consistent Clearance: Proper joint design ensures consistent clearance throughout the joint, which is critical for achieving uniform filler metal distribution and strong, reliable connections.
-
Practical Considerations for Equipment and Consumable Purchasers:
- Material Selection: Ensure that the materials being brazed are compatible with the filler metal and that their thermal expansion coefficients are considered to maintain proper clearance during heating and cooling.
- Quality Control: Implement rigorous quality control measures to verify that joint clearances are within the specified range before brazing. This may include using precision measuring tools and fixtures.
- Training and Expertise: Invest in training for operators to understand the importance of maintaining proper clearance and to develop the skills needed to achieve consistent results.
By understanding and addressing these key points, equipment and consumable purchasers can ensure that the brazing process produces strong, reliable joints that meet the required performance standards.
Summary Table:
Aspect | Impact of Improper Clearance |
---|---|
Capillary Action | Disrupted filler metal flow, leading to incomplete or weak joints. |
Excessive Clearance | Incomplete filling, voids, and reduced joint strength. |
Insufficient Clearance | Inadequate penetration, weak spots, and increased risk of cracking. |
Joint Design | Self-supporting joints and consistent clearance ensure uniform filler distribution and strength. |
Practical Considerations | Material compatibility, quality control, and operator training are key to success. |
Achieve flawless brazing results—contact our experts today for guidance on joint design and clearance optimization!