Hydraulic oil is a critical component in hydraulic systems, and failing to change it can lead to several detrimental effects on the system's performance and longevity. Over time, hydraulic oil degrades due to contamination, oxidation, and thermal breakdown, which can compromise the efficiency and reliability of the system. Regular maintenance, including oil changes, is essential to prevent issues such as increased wear and tear, reduced efficiency, overheating, and potential system failure. Neglecting to change hydraulic oil can result in costly repairs, downtime, and even safety hazards. Understanding the consequences of not changing hydraulic oil highlights the importance of adhering to maintenance schedules and ensuring the system operates optimally.
Key Points Explained:
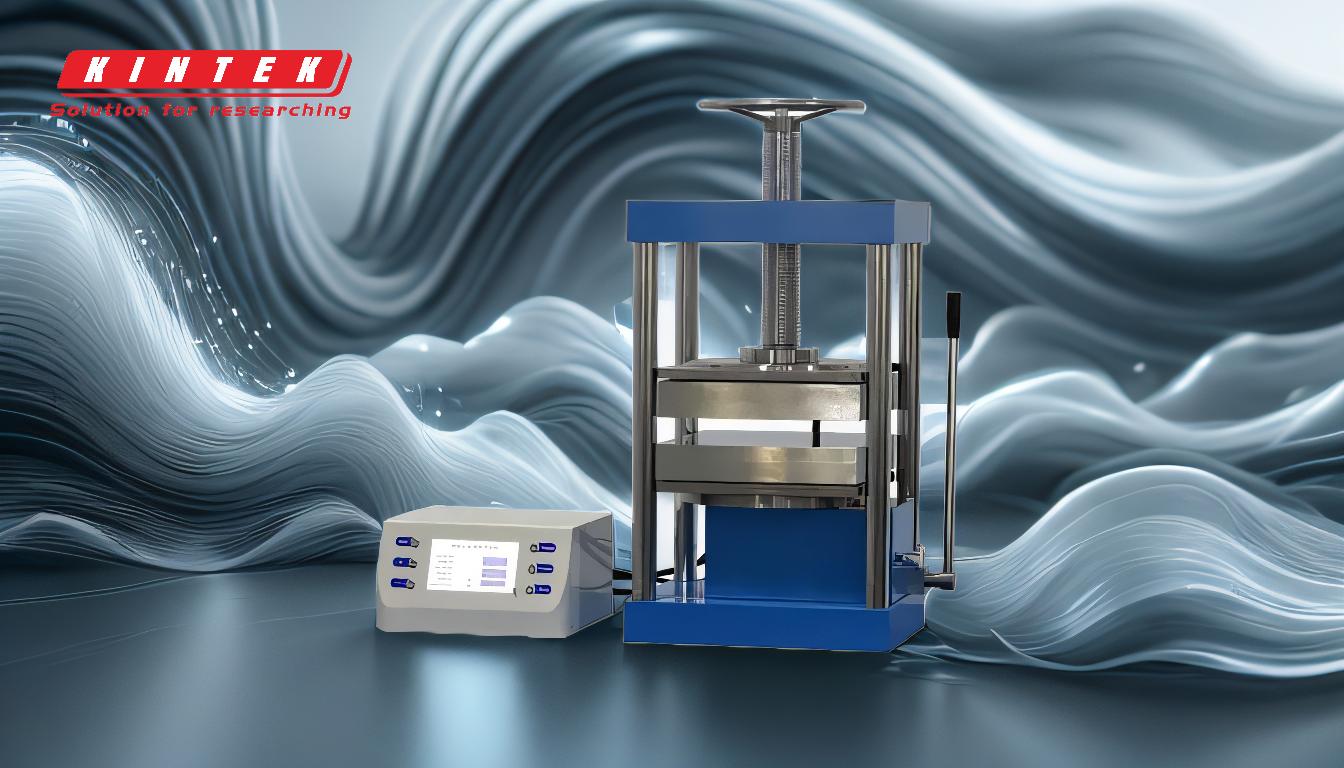
-
Degradation of Hydraulic Oil Over Time
- Hydraulic oil naturally degrades due to factors like contamination, oxidation, and thermal breakdown. Contaminants such as dirt, water, and metal particles can enter the system, leading to sludge formation and increased friction. Oxidation occurs when the oil reacts with oxygen, forming acids and varnish that can damage components. Thermal breakdown happens when the oil is exposed to high temperatures, reducing its viscosity and lubricating properties.
- Over time, these processes reduce the oil's ability to lubricate, cool, and protect the system, leading to inefficiencies and potential damage.
-
Increased Wear and Tear on Components
- Degraded hydraulic oil loses its lubricating properties, causing increased friction between moving parts. This friction accelerates wear on components such as pumps, valves, and cylinders, leading to premature failure.
- Contaminants in the oil can also act as abrasives, further damaging internal surfaces and seals. This wear and tear not only reduces the lifespan of components but also increases the likelihood of leaks and system malfunctions.
-
Reduced System Efficiency
- As hydraulic oil degrades, its viscosity changes, making it less effective at transferring power within the system. This results in reduced efficiency, as the system requires more energy to perform the same tasks.
- Additionally, sludge and varnish buildup can clog filters and restrict fluid flow, further diminishing the system's performance. Reduced efficiency can lead to higher operating costs and decreased productivity.
-
Overheating and Thermal Stress
- Hydraulic oil plays a crucial role in dissipating heat generated during system operation. When the oil degrades, its ability to absorb and transfer heat diminishes, leading to overheating.
- Overheating can cause thermal stress on components, resulting in warping, cracking, or failure. It also accelerates the degradation of the oil itself, creating a vicious cycle that further compromises system performance.
-
Potential for System Failure
- If hydraulic oil is not changed regularly, the cumulative effects of degradation, wear, and overheating can lead to catastrophic system failure. Components may seize, leaks may develop, or the system may stop functioning altogether.
- System failure can result in costly repairs, extended downtime, and potential safety hazards, particularly in industrial or heavy equipment applications.
-
Cost Implications of Neglecting Oil Changes
- While changing hydraulic oil incurs a cost, neglecting to do so can lead to far greater expenses. Premature component replacement, increased energy consumption, and downtime due to system failure can significantly impact operational budgets.
- Regular oil changes are a cost-effective preventive measure that helps avoid these larger expenses and ensures the system operates efficiently and reliably.
-
Importance of Adhering to Maintenance Schedules
- Following the manufacturer's recommended maintenance schedule for hydraulic oil changes is essential for maintaining system performance and longevity. Regular oil analysis can also help monitor the condition of the oil and identify potential issues before they become critical.
- Proper maintenance practices, including oil changes, are key to preventing the problems associated with degraded hydraulic oil and ensuring the system operates at peak efficiency.
In conclusion, failing to change hydraulic oil can have severe consequences for hydraulic systems, including increased wear, reduced efficiency, overheating, and potential system failure. Regular maintenance and oil changes are essential to prevent these issues and ensure the system operates reliably and efficiently. By adhering to maintenance schedules and monitoring the condition of the hydraulic oil, operators can avoid costly repairs, downtime, and safety hazards, ultimately extending the lifespan of the system.
Summary Table:
Consequence | Description |
---|---|
Degradation of Oil | Oil loses lubricating properties due to contamination, oxidation, and heat. |
Increased Wear and Tear | Accelerated friction damages components like pumps, valves, and seals. |
Reduced System Efficiency | Degraded oil increases energy consumption and reduces power transfer efficiency. |
Overheating | Poor heat dissipation leads to thermal stress and component damage. |
System Failure | Cumulative damage can cause catastrophic failure, downtime, and safety hazards. |
Cost Implications | Neglecting oil changes leads to higher repair and operational costs. |
Ensure your hydraulic system runs smoothly—contact our experts today for maintenance advice!