Hydraulic oil is designed to operate within specific temperature ranges, and when it gets too hot, several changes occur that can affect its performance and the overall hydraulic system. Elevated temperatures can lead to thermal degradation, oxidation, and a reduction in viscosity, which in turn can cause increased wear, reduced lubrication, and potential system failure. Understanding these effects is crucial for maintaining the efficiency and longevity of hydraulic systems.
Key Points Explained:
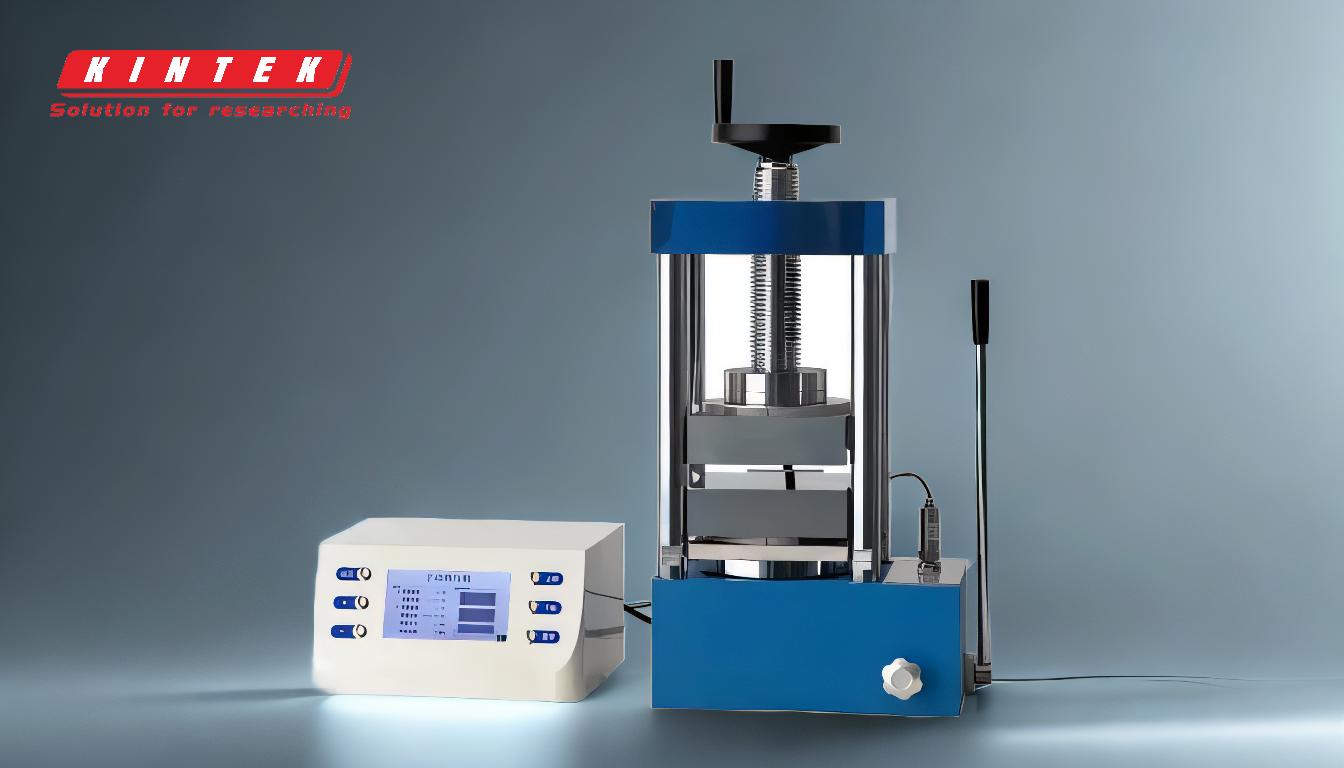
-
Thermal Degradation:
- Explanation: When hydraulic oil is exposed to high temperatures, it undergoes thermal degradation. This process breaks down the oil's molecular structure, leading to the formation of varnish, sludge, and other harmful by-products.
- Impact: These by-products can clog filters, valves, and other critical components, reducing the system's efficiency and potentially causing mechanical failure.
-
Oxidation:
- Explanation: Oxidation occurs when hydraulic oil reacts with oxygen at elevated temperatures. This reaction produces acids and other compounds that can corrode metal parts within the hydraulic system.
- Impact: The formation of acids can lead to increased wear and tear on components, reduced oil life, and the need for more frequent oil changes and maintenance.
-
Viscosity Reduction:
- Explanation: High temperatures cause the viscosity of hydraulic oil to decrease. Viscosity is a measure of the oil's resistance to flow, and it is crucial for maintaining proper lubrication and hydraulic pressure.
- Impact: Reduced viscosity can lead to inadequate lubrication, increased friction, and wear on moving parts. It can also result in a loss of hydraulic pressure, affecting the system's ability to perform its intended functions.
-
Formation of Air Bubbles:
- Explanation: When hydraulic oil gets too hot, it can release dissolved air, forming air bubbles. This phenomenon is known as cavitation.
- Impact: Air bubbles can cause erratic operation of hydraulic components, reduced system efficiency, and potential damage to pumps and valves due to the collapse of these bubbles under pressure.
-
Seal and Hose Damage:
- Explanation: High temperatures can cause the elastomers in seals and hoses to break down, leading to hardening, cracking, and eventual failure.
- Impact: Damaged seals and hoses can result in leaks, loss of hydraulic fluid, and contamination of the system, further exacerbating the issues caused by overheating.
-
Reduced Additive Effectiveness:
- Explanation: Hydraulic oils contain additives that enhance their performance, such as anti-wear agents, rust inhibitors, and antioxidants. High temperatures can degrade these additives, reducing their effectiveness.
- Impact: The loss of additive effectiveness can lead to increased wear, corrosion, and oxidation, further compromising the hydraulic system's performance and lifespan.
-
Increased Risk of Fire:
- Explanation: Extremely high temperatures can cause hydraulic oil to reach its flash point, making it more susceptible to ignition.
- Impact: This poses a significant safety risk, as it can lead to fires or explosions within the hydraulic system, endangering both equipment and personnel.
-
Preventive Measures:
- Explanation: To mitigate the effects of high temperatures on hydraulic oil, it is essential to implement preventive measures such as regular monitoring of oil temperature, using high-quality oils with appropriate viscosity and thermal stability, and ensuring proper system design and maintenance.
- Impact: These measures can help maintain optimal operating conditions, extend the life of the hydraulic oil, and prevent costly repairs and downtime.
In conclusion, understanding what happens to hydraulic oil when it gets hot is crucial for the proper maintenance and operation of hydraulic systems. By recognizing the signs of thermal degradation, oxidation, and viscosity reduction, and implementing preventive measures, you can ensure the longevity and efficiency of your hydraulic equipment.
Summary Table:
Effect | Explanation | Impact |
---|---|---|
Thermal Degradation | High temperatures break down oil molecules, forming varnish and sludge. | Clogs filters, reduces efficiency, and risks mechanical failure. |
Oxidation | Oil reacts with oxygen, producing acids that corrode metal parts. | Increases wear, reduces oil life, and requires frequent maintenance. |
Viscosity Reduction | Heat reduces oil's viscosity, affecting lubrication and hydraulic pressure. | Leads to inadequate lubrication, increased friction, and loss of system functionality. |
Formation of Air Bubbles | Heat releases dissolved air, causing cavitation. | Results in erratic operation, reduced efficiency, and potential pump damage. |
Seal and Hose Damage | High temperatures degrade elastomers, causing hardening and cracking. | Causes leaks, fluid loss, and system contamination. |
Reduced Additive Effectiveness | Heat degrades additives like anti-wear agents and antioxidants. | Increases wear, corrosion, and oxidation, compromising system performance. |
Increased Fire Risk | Extreme heat can cause oil to reach its flash point, making it flammable. | Poses safety risks, including fires or explosions. |
Preventive Measures | Monitor temperature, use high-quality oil, and maintain proper system design. | Extends oil life, prevents costly repairs, and ensures system efficiency. |
Ensure your hydraulic system runs smoothly—contact our experts today for tailored solutions!