When the brazing temperature is reached, the flux undergoes several critical changes to facilitate the brazing process. It melts before the filler metal, ensuring that all surfaces are wetted and prepared for bonding. The primary role of the flux is to dissolve the oxide layer on the metal surfaces, enabling the filler metal to flow and form a strong joint through capillary action. After the brazing process, the flux cools and solidifies into a fine, adhesive layer that remains on the surface. In some cases, such as furnace brazing, the atmosphere itself can remove oxides, reducing the need for flux.
Key Points Explained:
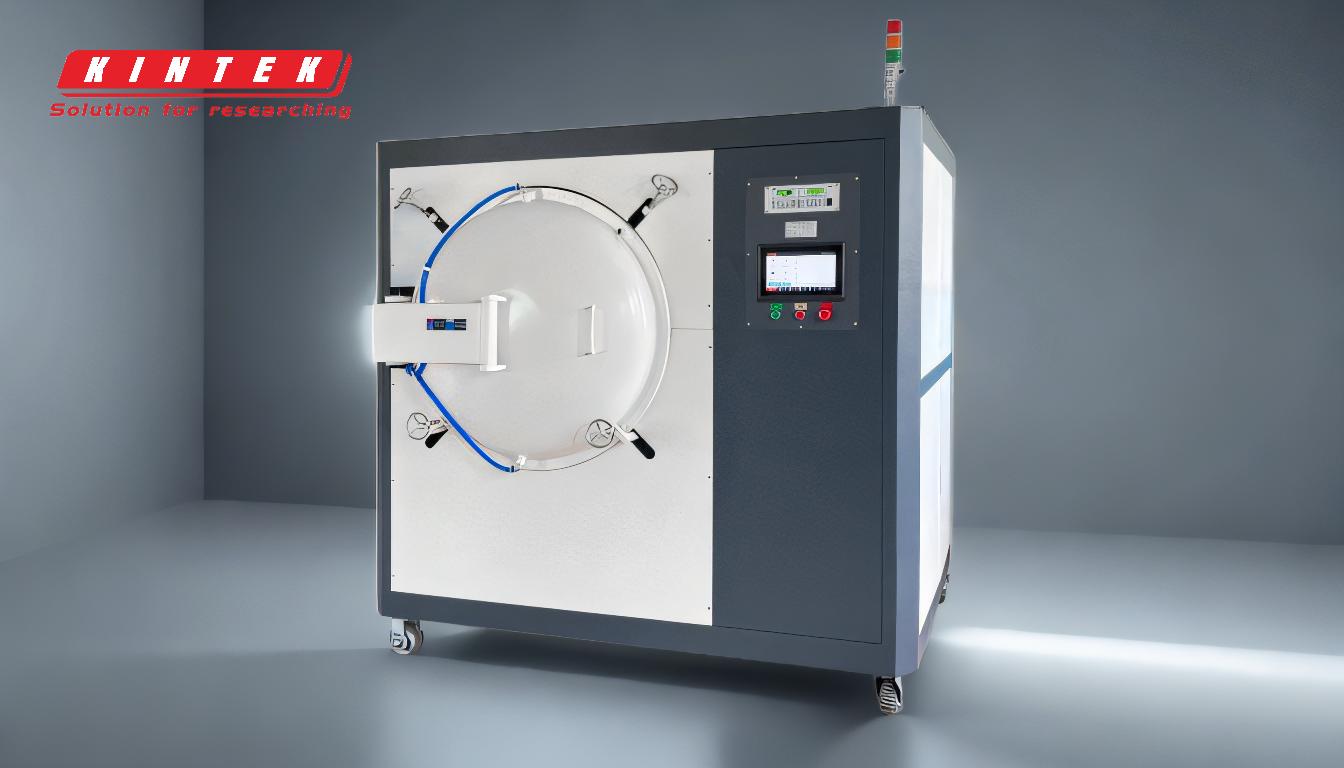
-
Melting of Flux Before Filler Metal:
- The flux melts at a lower temperature than the filler metal, ensuring that it can wet and prepare the surfaces before the filler metal flows. This step is crucial for creating a clean, oxide-free surface that allows the filler metal to bond effectively.
-
Dissolution of Oxide Layer:
- One of the primary functions of flux is to dissolve the oxide layer on the metal surfaces. Oxides can prevent the filler metal from wetting the surface and forming a strong bond. By removing these oxides, the flux ensures proper adhesion and joint formation.
-
Capillary Action and Joint Formation:
- Once the oxide layer is dissolved, the filler metal can flow into the gaps between the surfaces through capillary action. This process is essential for creating a strong, continuous joint. The flux aids in this by maintaining a clean surface and promoting the flow of the filler metal.
-
Cooling and Solidification of Flux:
- After the brazing process, the flux cools and solidifies into a fine, adhesive layer. This layer can provide additional protection to the joint and help maintain the integrity of the bond. However, in some applications, this residue may need to be removed to prevent contamination or corrosion.
-
Role of Atmosphere in Furnace Brazing:
- In furnace brazing, the atmosphere within the furnace can play a significant role in oxide removal. In such cases, the need for flux may be reduced or eliminated, as the controlled atmosphere can effectively remove oxides and prepare the surfaces for bonding.
Understanding these key points helps in selecting the appropriate flux and brazing conditions to achieve optimal results. Whether using flux or relying on a controlled atmosphere, the goal is to ensure clean, oxide-free surfaces that allow the filler metal to form strong, durable joints.
Summary Table:
Key Stage | Description |
---|---|
Melting of Flux | Flux melts before filler metal, preparing surfaces for bonding. |
Dissolution of Oxide Layer | Flux dissolves oxides, ensuring clean surfaces for filler metal adhesion. |
Capillary Action | Filler metal flows into gaps, forming strong joints with flux assistance. |
Cooling and Solidification | Flux solidifies into an adhesive layer, protecting the joint. |
Role of Atmosphere in Brazing | Controlled atmosphere in furnace brazing can reduce or eliminate flux need. |
Need expert advice on brazing processes? Contact us today for tailored solutions!