Heat treatment is a critical process used to strengthen the structure of metals by altering their mechanical and physical properties. Common methods include annealing, quenching, tempering, case hardening, carburizing, precipitation hardening, and normalizing. These processes work by manipulating the microstructure of the metal, influencing properties such as hardness, strength, ductility, and toughness. Each method has a unique approach, such as controlled heating and cooling rates, to achieve desired outcomes. For example, quenching rapidly cools the metal to increase hardness, while tempering reduces brittleness. Understanding these methods helps in selecting the appropriate treatment to enhance the metal's performance for specific applications.
Key Points Explained:
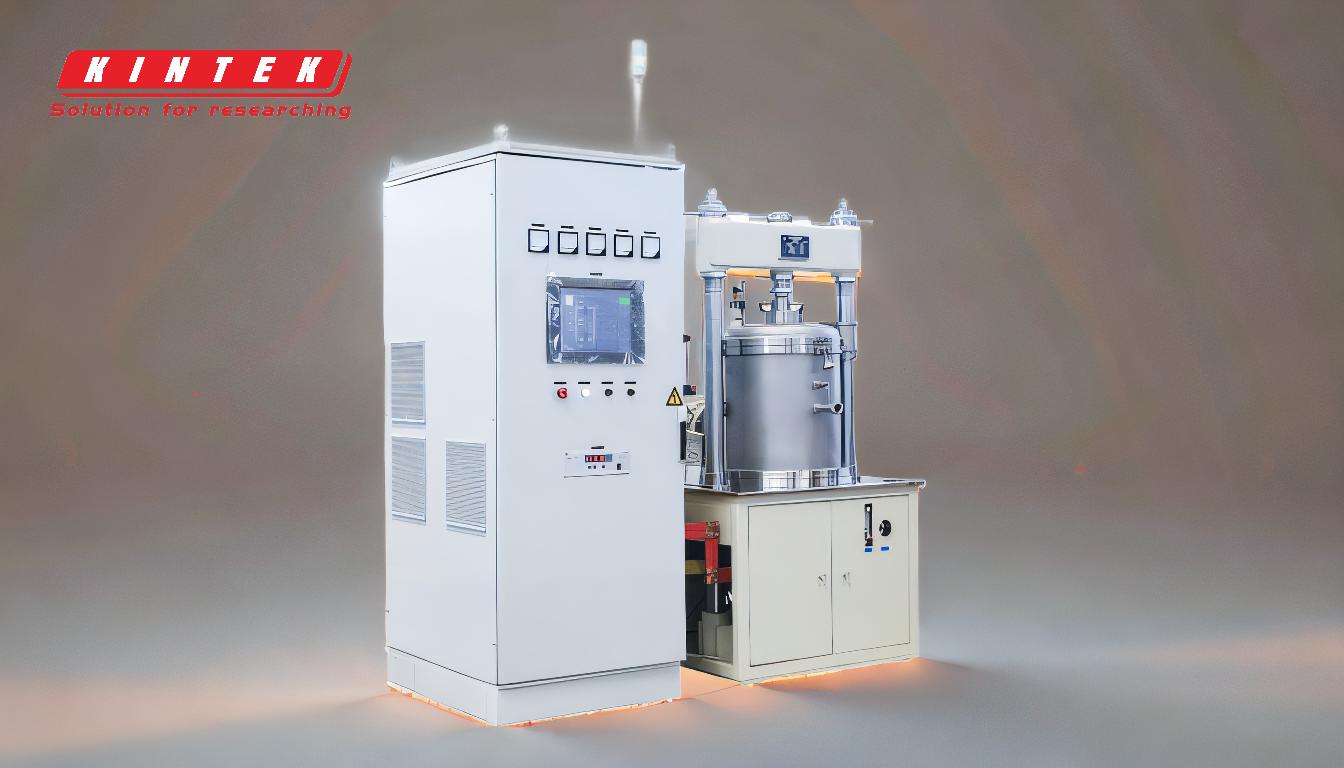
-
Annealing
- Process: Heating the metal to a specific temperature, holding it there for a period, and then slowly cooling it.
- Purpose: Improves ductility, reduces hardness, and relieves internal stresses.
- Application: Often used to make metals more workable for subsequent manufacturing processes like machining or forming.
-
Quenching
- Process: Rapidly cooling the metal by immersing it in a liquid (e.g., water, oil, or brine) after heating it to a high temperature.
- Purpose: Increases hardness and strength by creating a martensitic structure.
- Application: Commonly used for steels to achieve high surface hardness, though it may increase brittleness.
-
Tempering
- Process: Reheating the quenched metal to a lower temperature and then cooling it.
- Purpose: Reduces brittleness caused by quenching while maintaining hardness and strength.
- Application: Used after quenching to balance hardness and toughness, making the metal more suitable for structural applications.
-
Case Hardening
- Process: Adding carbon or nitrogen to the surface of the metal through processes like carburizing or nitriding, followed by quenching.
- Purpose: Creates a hard, wear-resistant surface while maintaining a tough, ductile core.
- Application: Ideal for components like gears and bearings that require a hard surface to resist wear.
-
Carburizing
- Process: Heating the metal in the presence of a carbon-rich environment to diffuse carbon into the surface.
- Purpose: Increases surface hardness and wear resistance.
- Application: Commonly used for low-carbon steels to enhance their surface properties.
-
Precipitation Hardening
- Process: Heating the metal to dissolve alloying elements, followed by controlled cooling to form fine precipitates.
- Purpose: Increases strength and hardness without significantly reducing ductility.
- Application: Often used for aluminum, nickel, and stainless steel alloys in aerospace and automotive industries.
-
Normalizing
- Process: Heating the metal to a temperature above its critical range, holding it, and then cooling it in air.
- Purpose: Refines the grain structure, improves mechanical properties, and relieves internal stresses.
- Application: Used to prepare metals for further processing or to achieve a uniform microstructure.
-
Martensitic Transformation
- Process: Rapid cooling (quenching) to transform austenite into martensite, a hard and brittle phase.
- Purpose: Achieves high hardness and strength.
- Application: Used in steels where high wear resistance is required, such as in cutting tools.
By understanding these heat treatment methods, manufacturers can tailor the properties of metals to meet specific performance requirements, ensuring optimal functionality in their intended applications.
Summary Table:
Method | Process | Purpose | Application |
---|---|---|---|
Annealing | Heating and slow cooling to improve ductility and reduce hardness. | Relieves stress, improves workability. | Prepares metals for machining or forming. |
Quenching | Rapid cooling in liquid to increase hardness and strength. | Creates a martensitic structure for high hardness. | Used for steels requiring high surface hardness. |
Tempering | Reheating quenched metal to reduce brittleness while maintaining hardness. | Balances hardness and toughness. | Ideal for structural applications. |
Case Hardening | Adding carbon/nitrogen to the surface, followed by quenching. | Creates a hard surface with a tough core. | Used for gears, bearings, and wear-resistant components. |
Carburizing | Heating in a carbon-rich environment to diffuse carbon into the surface. | Increases surface hardness and wear resistance. | Enhances properties of low-carbon steels. |
Precipitation Hardening | Heating to dissolve alloying elements, then controlled cooling. | Increases strength and hardness without reducing ductility. | Common in aerospace and automotive industries. |
Normalizing | Heating above critical range, then air cooling. | Refines grain structure and relieves internal stresses. | Prepares metals for further processing or uniform microstructure. |
Martensitic Transformation | Rapid cooling to form a hard, brittle martensite phase. | Achieves high hardness and strength. | Used in cutting tools and wear-resistant steels. |
Need help selecting the right heat treatment for your metals? Contact our experts today for tailored solutions!