A burnout oven, also known as a burn-off oven, is a specialized piece of equipment used primarily in industrial and manufacturing settings to remove paint, powder coatings, or other residues from metal hardware, tools, or equipment. These ovens operate at high temperatures to thermally decompose coatings, leaving behind clean surfaces. They are particularly useful in industries like powder coating, where hooks, racks, and other equipment accumulate coatings during the process and require periodic cleaning. Burnout ovens are distinct from other types of ovens, such as lab ovens or furnaces, due to their specific application in cleaning and their ability to handle high-temperature processes.
Key Points Explained:
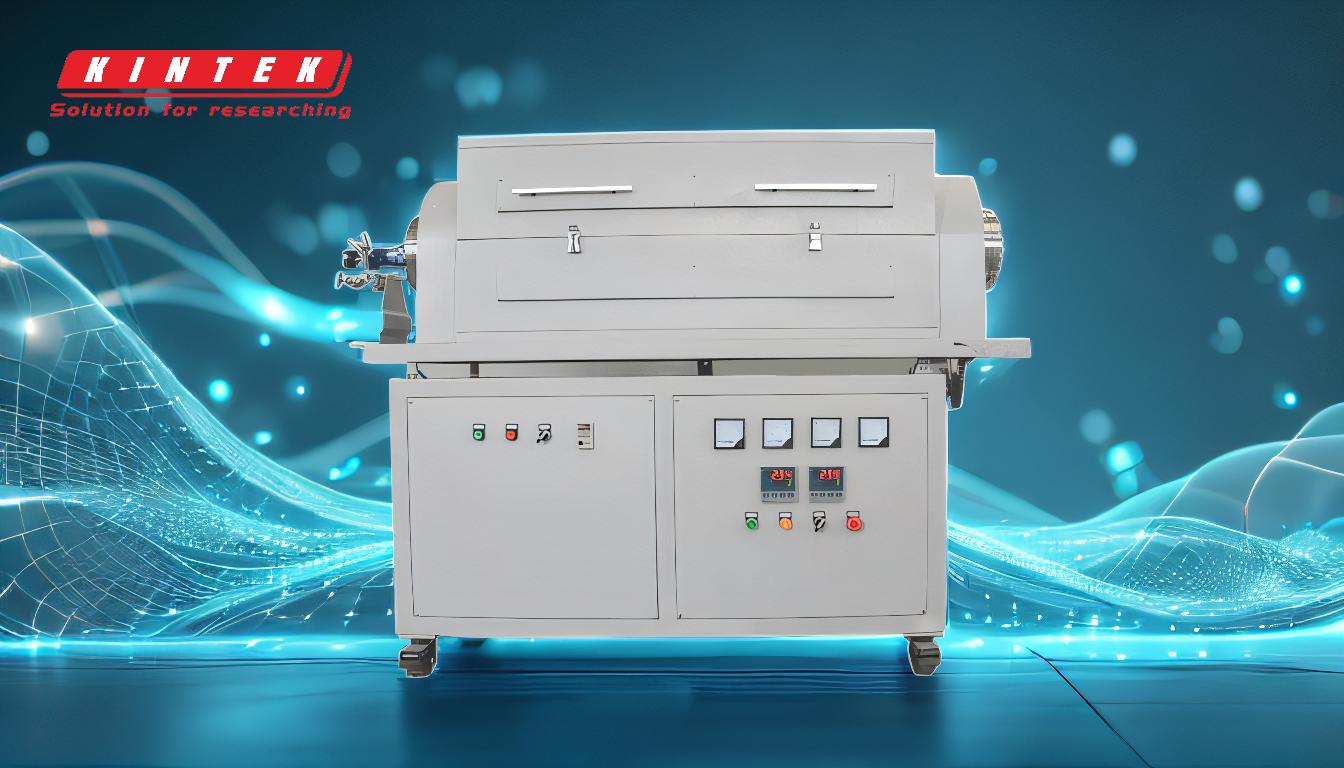
-
Definition and Purpose of a Burnout Oven:
- A burnout oven is designed to remove paint, powder coatings, or other residues from metal surfaces by exposing them to high temperatures. The heat causes the coatings to decompose, leaving the equipment clean and ready for reuse.
- These ovens are essential in industries like powder coating, where tools and racks become coated during the process and need regular cleaning to maintain efficiency.
-
Applications in Industrial Settings:
- Burnout ovens are particularly useful for cleaning hooks, racks, and other equipment used in powder coating lines. These items often accumulate layers of paint or powder coatings, which can interfere with the coating process if not removed.
- They are also used in other finishing industries where metal hardware or equipment requires periodic cleaning to remove coatings or residues.
-
How Burnout Ovens Work:
- Burnout ovens operate by heating the coated items to temperatures high enough to break down the paint or powder coatings. This process, known as thermal decomposition or pyrolysis, converts the coatings into gases and ash, which can be easily removed.
- The ovens are equipped with ventilation systems to safely expel fumes and volatile organic compounds (VOCs) generated during the process.
-
Comparison with Other Types of Ovens:
- Lab Ovens: These are used for lower-temperature applications like drying, sterilization, and testing. They rely on convection heating and are not designed for the high-temperature processes required in burnout applications.
- Lab Furnaces: These are used for higher-temperature applications, such as annealing or heat treatment, but are generally more expensive and not specifically designed for cleaning purposes.
- Burnout ovens are distinct in their focus on removing coatings and residues, making them a specialized tool in industrial cleaning processes.
-
Key Features of Burnout Ovens:
- High-Temperature Capability: Burnout ovens can reach temperatures sufficient to decompose coatings, typically ranging from 500°F to 1000°F (260°C to 538°C), depending on the material being removed.
- Ventilation Systems: To handle the fumes and VOCs generated during the burnout process, these ovens are equipped with vents or exhaust systems to ensure safe operation.
- Durability: Designed for industrial use, burnout ovens are built to withstand frequent high-temperature cycles and exposure to harsh chemicals.
-
Benefits of Using Burnout Ovens:
- Efficiency: Burnout ovens provide a quick and effective way to clean coated equipment, reducing downtime in production lines.
- Cost-Effectiveness: By extending the life of hooks, racks, and other equipment, burnout ovens help reduce replacement costs.
- Environmental Safety: Proper ventilation systems in burnout ovens ensure that harmful fumes are safely expelled, minimizing environmental and health risks.
-
Considerations for Purchasing a Burnout Oven:
- Temperature Range: Ensure the oven can reach the temperatures required for the specific coatings or residues you need to remove.
- Size and Capacity: Choose an oven that can accommodate the size and quantity of items you need to clean.
- Ventilation Requirements: Verify that the oven’s ventilation system meets safety and regulatory standards for your facility.
- Energy Efficiency: Look for models designed to minimize energy consumption, especially if the oven will be used frequently.
In summary, a burnout oven is a vital tool in industries that require the periodic cleaning of metal equipment coated with paint or powder. Its ability to efficiently remove residues at high temperatures, combined with safety features like ventilation systems, makes it an indispensable asset for maintaining production efficiency and equipment longevity.
Summary Table:
Feature | Description |
---|---|
Purpose | Removes paint, powder coatings, or residues from metal surfaces. |
Applications | Used in powder coating and finishing industries for cleaning hooks and racks. |
How It Works | Uses high temperatures (500°F–1000°F) to thermally decompose coatings. |
Key Features | High-temperature capability, ventilation systems, and industrial durability. |
Benefits | Improves efficiency, reduces costs, and ensures environmental safety. |
Considerations | Temperature range, size, ventilation, and energy efficiency. |
Ready to enhance your industrial cleaning process? Contact us today to find the perfect burnout oven for your needs!