Electroplating sensing films presents a significant challenge due to the inherent variability in the electroplating process. This variability arises primarily from the uneven distribution of the electric field within the plating bath, which is influenced by factors such as bath geometry and the placement of anodes and cathodes. Such unevenness can lead to inconsistent film thickness, affecting the performance and reliability of the sensing films. Addressing this issue requires careful optimization of the electroplating setup and process parameters to ensure uniform deposition across the substrate.
Key Points Explained:
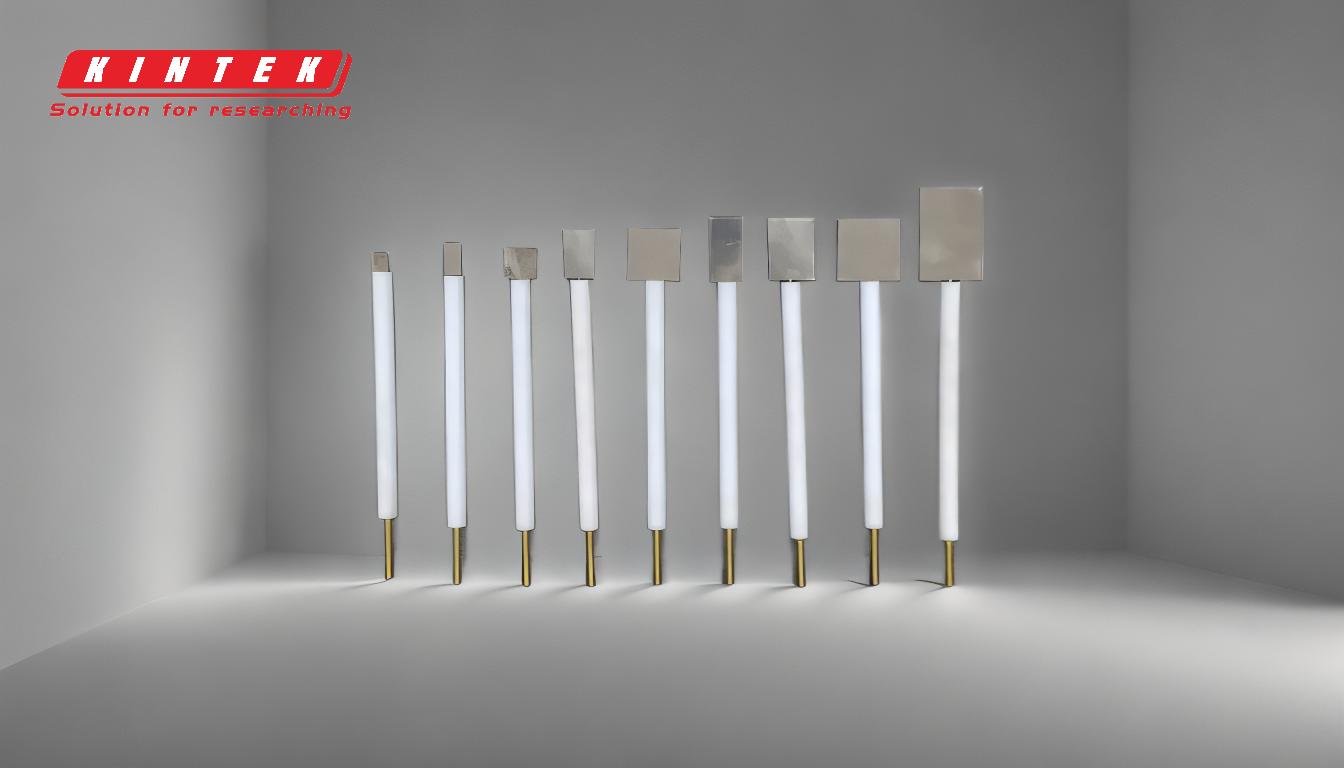
-
Inherent Variability in Electroplating Process:
- The electroplating process is inherently variable, which can lead to inconsistencies in the deposition of sensing films.
- This variability is a significant challenge because it directly impacts the quality and performance of the final product.
-
Uneven Distribution of Electric Field:
- The electric field within the plating bath is crucial for the deposition process.
- Uneven distribution of this field can occur due to the geometry of the bath or the placement of anodes and cathodes.
- This unevenness results in areas where the deposition is either thicker or thinner than desired.
-
Impact on Film Thickness:
- Areas of thicker deposition can lead to excessive material buildup, which may affect the functionality of the sensing film.
- Conversely, areas of thinner deposition may not provide adequate coverage, leading to potential performance issues or failure of the sensing film.
-
Influence of Bath Geometry:
- The shape and size of the plating bath can significantly influence the distribution of the electric field.
- Complex geometries or large bath sizes can exacerbate the unevenness, making it more challenging to achieve uniform deposition.
-
Placement of Anodes and Cathodes:
- The positioning of anodes and cathodes within the bath plays a critical role in the uniformity of the electric field.
- Poor placement can lead to localized areas of high or low current density, further contributing to uneven deposition.
-
Optimization Strategies:
- To mitigate these challenges, careful optimization of the electroplating setup is necessary.
- This includes adjusting the bath geometry, optimizing the placement of anodes and cathodes, and fine-tuning process parameters such as current density and plating time.
- Advanced techniques like pulse electroplating or the use of additives in the plating solution can also help achieve more uniform deposition.
-
Importance for Sensing Films:
- For sensing films, uniformity in thickness is critical to ensure consistent performance and reliability.
- Any variability in thickness can lead to inconsistencies in the sensor's response, affecting its accuracy and sensitivity.
-
Broader Implications:
- Addressing the challenges associated with electroplating sensing films not only improves the quality of the films but also enhances the overall performance of the sensors.
- This is particularly important in applications where precision and reliability are paramount, such as in medical devices, environmental monitoring, and industrial automation.
By understanding and addressing these key points, manufacturers can improve the electroplating process for sensing films, leading to more reliable and high-performing sensors.
Summary Table:
Key Challenges | Impact | Solutions |
---|---|---|
Inherent variability in process | Inconsistent film thickness, affecting performance and reliability | Optimize bath geometry and anode/cathode placement |
Uneven electric field distribution | Thicker or thinner deposition areas, leading to functional issues | Adjust current density, plating time, and use pulse electroplating techniques |
Complex bath geometry | Exacerbates uneven deposition, making uniform coverage harder to achieve | Simplify bath design or use advanced plating solutions |
Poor anode/cathode placement | Localized high/low current density areas, causing uneven deposition | Optimize placement for uniform electric field distribution |
Importance of uniform thickness | Ensures consistent sensor response, accuracy, and reliability | Fine-tune process parameters and use additives for better control |
Struggling with electroplating challenges? Contact our experts today to optimize your process and achieve reliable sensing films!