A coreless induction furnace is a type of electric furnace used for melting metals and alloys, particularly in industries like metallurgy, ceramics, and electronics. It operates on the principle of electromagnetic induction, where an alternating current generates a magnetic field that induces eddy currents in the metal, causing it to heat up and melt. Unlike core-type induction furnaces, coreless furnaces do not have a magnetic core, making them more versatile and efficient for handling a wide range of materials. They are widely used for applications such as melting, alloying, and heat treatment of metals, as well as for high-temperature experiments and material testing.
Key Points Explained:
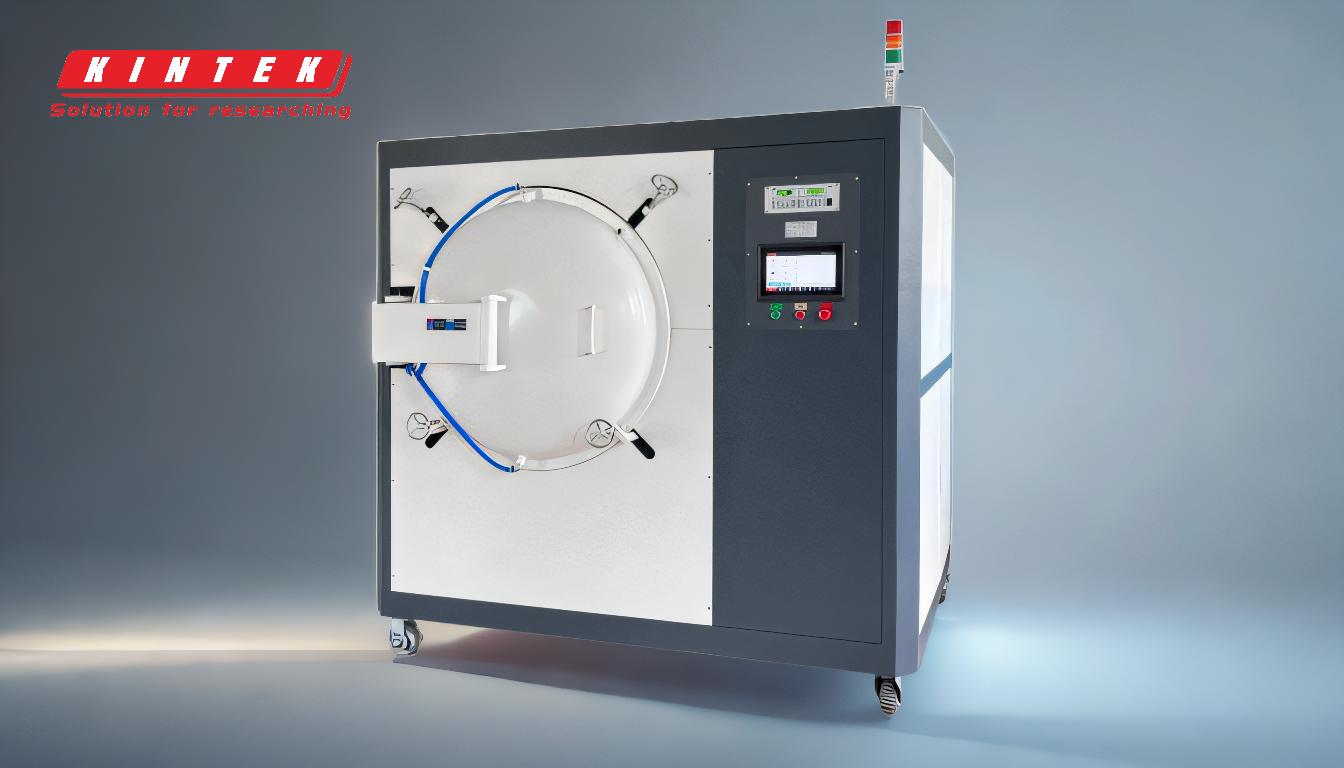
-
Principle of Operation:
- The coreless induction furnace works on electromagnetic induction. An alternating current passes through a coil, creating a magnetic field that induces eddy currents in the metal placed inside the furnace. These eddy currents generate heat due to the electrical resistance of the metal, leading to its melting.
-
Design and Structure:
- Unlike core-type induction furnaces, coreless furnaces do not have a magnetic core. This design allows for greater flexibility in handling different types of metals and alloys. The furnace typically consists of a refractory-lined crucible surrounded by an induction coil.
-
Applications:
- Coreless induction furnaces are used in a variety of industries, including:
- Metallurgy: For melting and alloying metals.
- Ceramics: For sintering and high-temperature processing.
- Electronics: For material testing and high-temperature experiments.
- Chemical Industry: For material treatment and synthesis.
- They are also used in universities and research institutes for experimental purposes.
- Coreless induction furnaces are used in a variety of industries, including:
-
Advantages:
- Versatility: Can handle a wide range of materials and alloys.
- Efficiency: High thermal efficiency due to direct heating of the metal.
- Control: Precise temperature control and uniform heating.
- Clean Operation: No combustion gases, making it environmentally friendly.
-
Comparison with Core-Type Induction Furnaces:
- Coreless furnaces are generally more suitable for smaller batches and a wider variety of materials, while core-type furnaces are better for large-scale, continuous operations.
-
Vacuum Induction Furnace:
- A specialized type of coreless induction furnace is the vacuum induction furnace, which operates under a vacuum or controlled atmosphere. This is particularly useful for melting reactive metals and alloys that would otherwise oxidize or react with atmospheric gases.
-
Maintenance and Safety:
- Regular maintenance of the refractory lining and induction coil is essential for optimal performance. Safety measures include proper insulation, cooling systems, and protective gear for operators.
By understanding these key points, a purchaser can make an informed decision about whether a coreless induction furnace is the right equipment for their specific needs, especially when considering factors like material type, batch size, and operational environment.
Summary Table:
Feature | Details |
---|---|
Principle of Operation | Electromagnetic induction heats metal via eddy currents. |
Design | No magnetic core; uses a refractory-lined crucible and induction coil. |
Applications | Metallurgy, ceramics, electronics, chemical industry, and research. |
Advantages | Versatile, efficient, precise temperature control, and environmentally clean. |
Ready to enhance your metal melting process? Contact us today to learn more about coreless induction furnaces!