A furnace for firing pottery is commonly referred to as a kiln. Kilns are specialized furnaces designed to achieve the high temperatures necessary for firing clay and other ceramic materials. They come in various types, including electric, gas, and wood-fired kilns, each suited for different applications and scales of production. Kilns are essential in pottery for transforming raw clay into durable, finished ceramic pieces through processes like bisque firing and glaze firing. The choice of kiln depends on factors such as the volume of production, desired temperature range, and specific requirements of the pottery being created.
Key Points Explained:
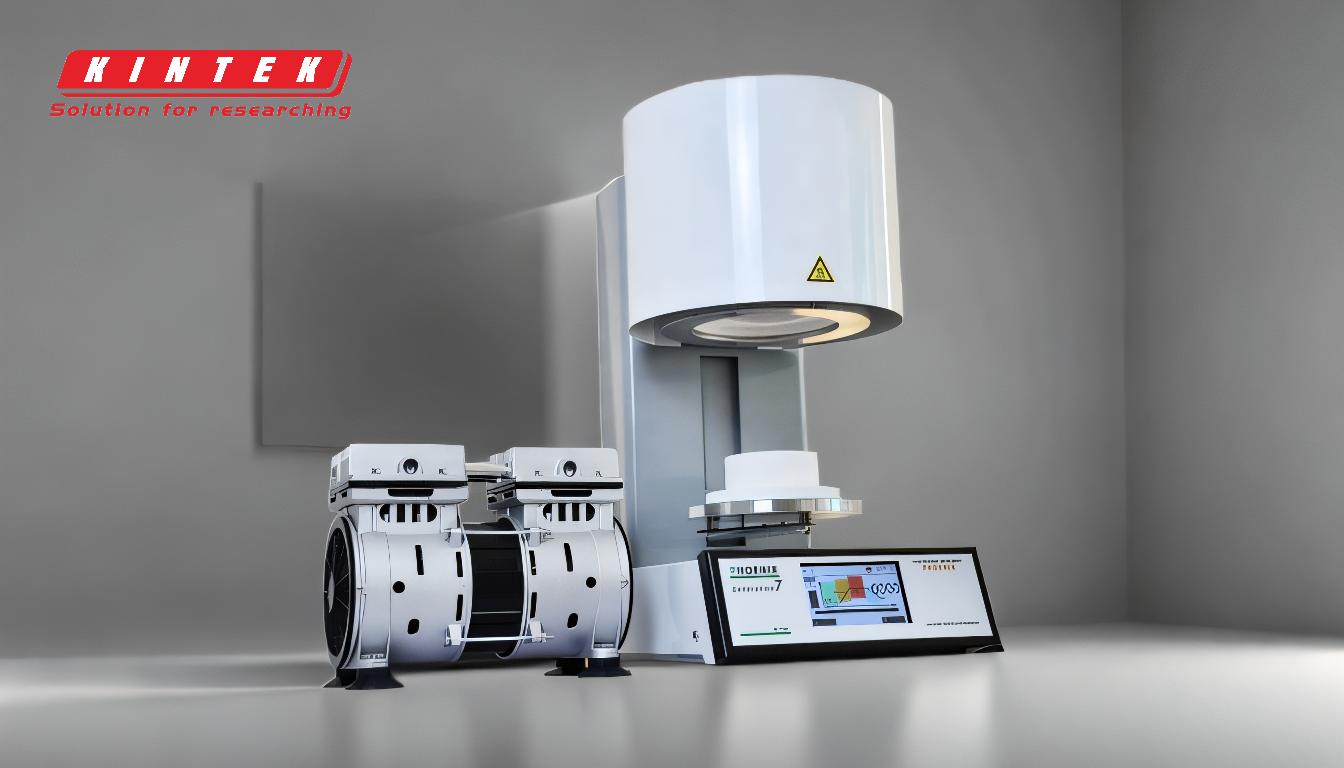
-
Definition of a Kiln:
- A kiln is a type of furnace specifically designed for firing pottery and ceramics. It provides controlled high-temperature environments necessary to harden clay and fix glazes.
- Unlike general-purpose furnaces, kilns are tailored to meet the unique needs of ceramic artists and manufacturers.
-
Types of Kilns:
- Electric Kilns: These are popular for their ease of use and precise temperature control. They are ideal for small to medium-scale pottery production and are commonly used in studios and educational settings.
- Gas Kilns: Known for their ability to reach high temperatures quickly, gas kilns are often used for larger-scale production and for achieving specific atmospheric effects in the firing process.
- Wood-Fired Kilns: These traditional kilns use wood as fuel and are valued for the unique textures and colors they impart to pottery. They are often used by artists seeking a more organic aesthetic.
- Raku Kilns: Designed for the raku firing technique, these kilns are smaller and used for rapid heating and cooling, resulting in distinctive crackled glazes and metallic finishes.
-
Functions of a Kiln:
- Bisque Firing: The first firing process that hardens the clay and prepares it for glazing.
- Glaze Firing: The second firing process that melts the glaze onto the pottery, creating a smooth, glass-like surface.
- Reduction Firing: A specialized process in gas or wood-fired kilns that alters the atmosphere inside the kiln to achieve specific color effects.
-
Key Features to Consider When Choosing a Kiln:
- Temperature Range: Different types of pottery require different firing temperatures. Ensure the kiln can reach the necessary heat for your specific needs.
- Size and Capacity: Consider the volume of pottery you plan to produce. Larger kilns are better for high-volume production, while smaller kilns are suitable for individual artists.
- Energy Source: Electric kilns are convenient and clean, while gas and wood-fired kilns offer unique aesthetic benefits but require more maintenance.
- Control Systems: Modern kilns often come with digital controllers for precise temperature management, which is crucial for consistent results.
-
Comparison to Industrial Furnaces:
- While kilns are specialized for pottery, industrial furnaces like Rotary Drum Furnaces, Roller Hearth Kilns, and Pusher Slab Kilns are designed for sintering industrial products. These furnaces are typically used in manufacturing settings and are not suitable for artistic pottery.
- Batch furnaces, mentioned in the reference, are used for low-volume sintering, which is somewhat analogous to small-scale pottery kilns, but the materials and processes differ significantly.
-
Importance of Kilns in Pottery:
- Kilns are indispensable in pottery as they enable the transformation of fragile clay into durable ceramic pieces.
- The firing process also allows for creative expression through glazing and surface treatments, making kilns a cornerstone of ceramic art and production.
By understanding the different types of kilns and their functions, pottery enthusiasts and professionals can make informed decisions about the best equipment for their needs. Whether you are a hobbyist or a commercial producer, selecting the right kiln is crucial for achieving the desired results in your pottery projects.
Summary Table:
Feature | Description |
---|---|
Types of Kilns | Electric, Gas, Wood-Fired, Raku |
Functions | Bisque Firing, Glaze Firing, Reduction Firing |
Key Considerations | Temperature Range, Size/Capacity, Energy Source, Control Systems |
Applications | Small-scale studios, Educational settings, Large-scale production, Artistic use |
Ready to elevate your pottery projects? Contact us today to find the perfect kiln for your needs!