When selecting a good flux for brazing, it is essential to consider the type of base metals being joined, the filler metal used, and the specific brazing process. The flux must be compatible with the filler metal and base metals to ensure proper wetting, flow, and bonding. Additionally, the flux should effectively remove oxides, prevent re-oxidation during the brazing process, and be easy to clean after brazing. The choice of flux also depends on the brazing environment, such as whether it is conducted in a controlled atmosphere or an open flame. Proper flux selection is critical for achieving strong, durable, and defect-free brazed joints.
Key Points Explained:
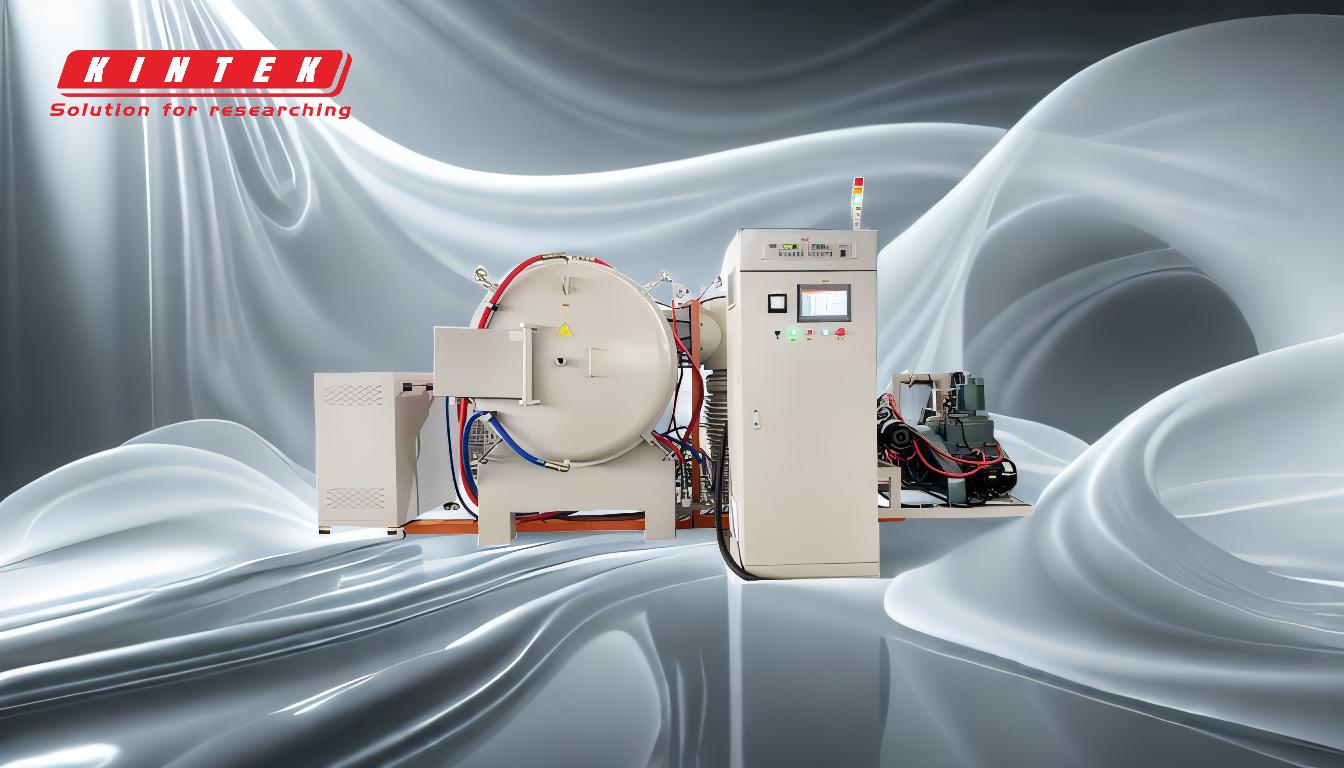
-
Compatibility with Base Metals and Filler Metal
- The flux must be chemically compatible with both the base metals and the filler metal. For example, fluxes for aluminum brazing differ significantly from those used for copper or stainless steel.
- The flux should promote wetting and flow of the filler metal, ensuring a strong bond between the base metals.
-
Oxide Removal and Prevention
- A good flux effectively removes oxides from the metal surfaces during the brazing process. Oxides can inhibit proper bonding, so their removal is critical.
- The flux should also prevent re-oxidation during heating, especially in environments where oxygen is present.
-
Temperature Range and Activity
- The flux must be active within the temperature range of the brazing process. For instance, fluxes designed for high-temperature brazing (e.g., with silver-based filler metals) differ from those used for lower-temperature applications.
- The flux should become active before the filler metal melts to ensure proper surface preparation.
-
Brazing Environment Considerations
- For brazing in a controlled atmosphere (e.g., vacuum or inert gas), fluxes may not be required, as the environment itself prevents oxidation.
- In open-air brazing, fluxes are essential to protect the joint area from oxidation and contamination.
-
Post-Brazing Cleanup
- A good flux should be easy to remove after brazing. Residues can cause corrosion or interfere with subsequent processes, so water-soluble or self-removing fluxes are often preferred.
- Some fluxes require specific cleaning agents or methods, so compatibility with post-braze cleaning processes is important.
-
Flux Forms and Application Methods
- Fluxes are available in various forms, including paste, powder, liquid, and pre-placed cores. The choice depends on the brazing method and application requirements.
- For example, flux-cored filler wires are convenient for automated brazing processes, while paste fluxes are suitable for manual applications.
-
Safety and Environmental Factors
- Some fluxes contain corrosive or hazardous chemicals, so handling and disposal must comply with safety regulations.
- Environmentally friendly fluxes are increasingly preferred to minimize health risks and environmental impact.
By carefully evaluating these factors, you can select a flux that ensures optimal brazing performance and high-quality joints.
Summary Table:
Factor | Key Considerations |
---|---|
Compatibility with Base Metals | Must be chemically compatible with base and filler metals for proper wetting and flow. |
Oxide Removal & Prevention | Removes oxides and prevents re-oxidation during brazing. |
Temperature Range | Must be active within the brazing temperature range. |
Brazing Environment | Controlled atmosphere may not require flux; open-air brazing does. |
Post-Brazing Cleanup | Should be easy to remove, with minimal residue. |
Flux Forms & Applications | Available as paste, powder, liquid, or pre-placed cores. |
Safety & Environmental Impact | Choose environmentally friendly fluxes to minimize risks. |
Need help selecting the right flux for your brazing project? Contact our experts today!