A heat treatment furnace is a specialized heating chamber designed to hold and heat steel or other materials to specific temperatures for the purpose of altering their physical and mechanical properties. These furnaces are essential in industries such as manufacturing, automotive, aerospace, and metallurgy, where precise control over material properties is required. Heat treatment furnaces come in various types, including roller hearth, pusher, box, pot/pit, conveyor belt, and integral-quench furnaces, each suited for specific applications. Modern furnaces, such as vacuum resistance furnaces, use advanced technologies like computer-controlled heating and gas environments to ensure uniformity, repeatability, and high-quality results. The primary goal of these furnaces is to regulate heat supply and maintain specific temperatures to achieve desired material characteristics, such as hardness, ductility, and strength.
Key Points Explained:
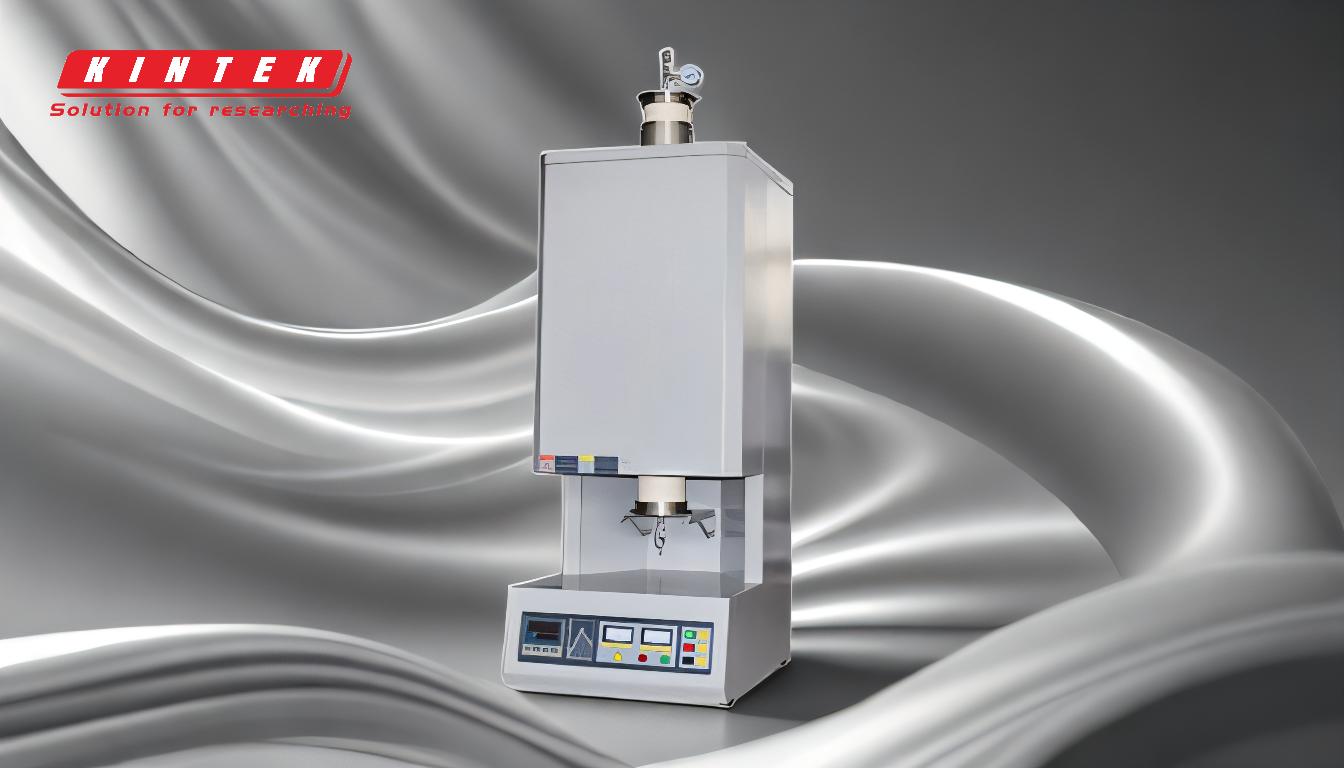
-
Definition and Purpose of Heat Treatment Furnaces:
- Heat treatment furnaces are heating chambers designed to hold and heat materials, primarily steel, to specific temperatures.
- Their primary purpose is to alter the physical and mechanical properties of materials, such as hardness, strength, and ductility, through controlled heating and cooling processes.
- These furnaces are critical in industries where material performance is paramount, such as automotive, aerospace, and manufacturing.
-
Types of Heat Treatment Furnaces:
- Roller Hearth Furnaces: Used for continuous processing of materials, ideal for annealing and other heat treatment processes.
- Pusher Furnaces: Suitable for batch processing, where materials are pushed through the furnace in a controlled manner.
- Box Furnaces: Versatile and used for a wide range of heat treatment processes, including annealing, tempering, and hardening.
- Pot/Pit Furnaces: Typically used for smaller batches or specialized treatments, often involving molten salt or other media.
- Conveyor Belt Furnaces: Designed for continuous processing, often used in high-volume production environments.
- Integral-Quench Furnaces: Combine heating and quenching processes in a single unit, ensuring rapid cooling for hardening applications.
-
Advanced Heat Treatment Furnaces:
- Vacuum Heat Treatment Furnaces: These furnaces use a vacuum environment, often filled with inert gases like argon, to prevent oxidation and ensure uniform heating. They can reach temperatures up to 2400°F and are computer-controlled for precision.
- Vacuum Resistance Furnaces: Modern versions are endothermic, with no furnace groove, and the entire shell serves as the vacuum container. They come in vertical, horizontal, single-chamber, and three-chamber configurations.
-
Key Features and Technologies:
- Temperature Control: Heat treatment furnaces are equipped with advanced temperature regulation systems to maintain specific temperatures during the heating and cooling phases.
- Computer Control: Modern furnaces use computer-controlled systems to ensure uniformity, repeatability, and precision in the heat treatment process.
- Gas Environments: In vacuum furnaces, oxygen is removed and replaced with inert gases like argon to prevent oxidation and achieve high-quality results.
- Soak Time: The duration materials are held at a specific temperature (soak time) is carefully controlled based on the material and desired properties.
-
Applications and Industries:
- Manufacturing: Used to enhance the properties of steel and other metals for use in machinery, tools, and components.
- Automotive: Critical for producing durable and high-performance parts, such as engine components and transmission gears.
- Aerospace: Ensures materials can withstand extreme conditions, such as high temperatures and stress, in aircraft and spacecraft components.
- Metallurgy: Used in the production of alloys and specialized metals with specific mechanical properties.
-
Benefits of Heat Treatment Furnaces:
- Reproducibility: Ensures consistent material properties across batches, which is crucial for quality control.
- Customization: Allows for precise control over the heat treatment process to achieve specific material characteristics.
- Efficiency: Modern furnaces are designed to minimize energy consumption while maximizing performance.
- Quality Improvement: Enhances material properties, such as hardness, strength, and resistance to wear and tear.
In summary, heat treatment furnaces are indispensable tools in modern manufacturing and metallurgy, offering precise control over material properties through advanced heating and cooling processes. Their versatility, combined with advanced technologies, makes them essential for producing high-quality, durable, and reliable components across various industries.
Summary Table:
Aspect | Details |
---|---|
Purpose | Alters physical and mechanical properties of materials like steel. |
Key Types | Roller hearth, pusher, box, pot/pit, conveyor belt, integral-quench furnaces. |
Advanced Types | Vacuum heat treatment and vacuum resistance furnaces. |
Key Features | Precise temperature control, computer-controlled systems, gas environments. |
Applications | Manufacturing, automotive, aerospace, metallurgy. |
Benefits | Reproducibility, customization, efficiency, quality improvement. |
Need a heat treatment furnace tailored to your needs? Contact our experts today!