A physical vapor deposition (PVD) apparatus is a sophisticated system used to deposit thin films of material onto a substrate through the process of vaporizing a solid or liquid source material in a vacuum environment. The vaporized material condenses onto the substrate, forming a thin, uniform coating. PVD is widely used in industries such as semiconductors, optics, and tool coatings due to its ability to produce high-quality, durable films. The process involves several key components, including a vacuum chamber, a target material, an energy source to vaporize the target, and a substrate holder. The method is divided into different categories based on how the solid material is converted into vapor, such as sputtering, evaporation, or ion plating.
Key Points Explained:
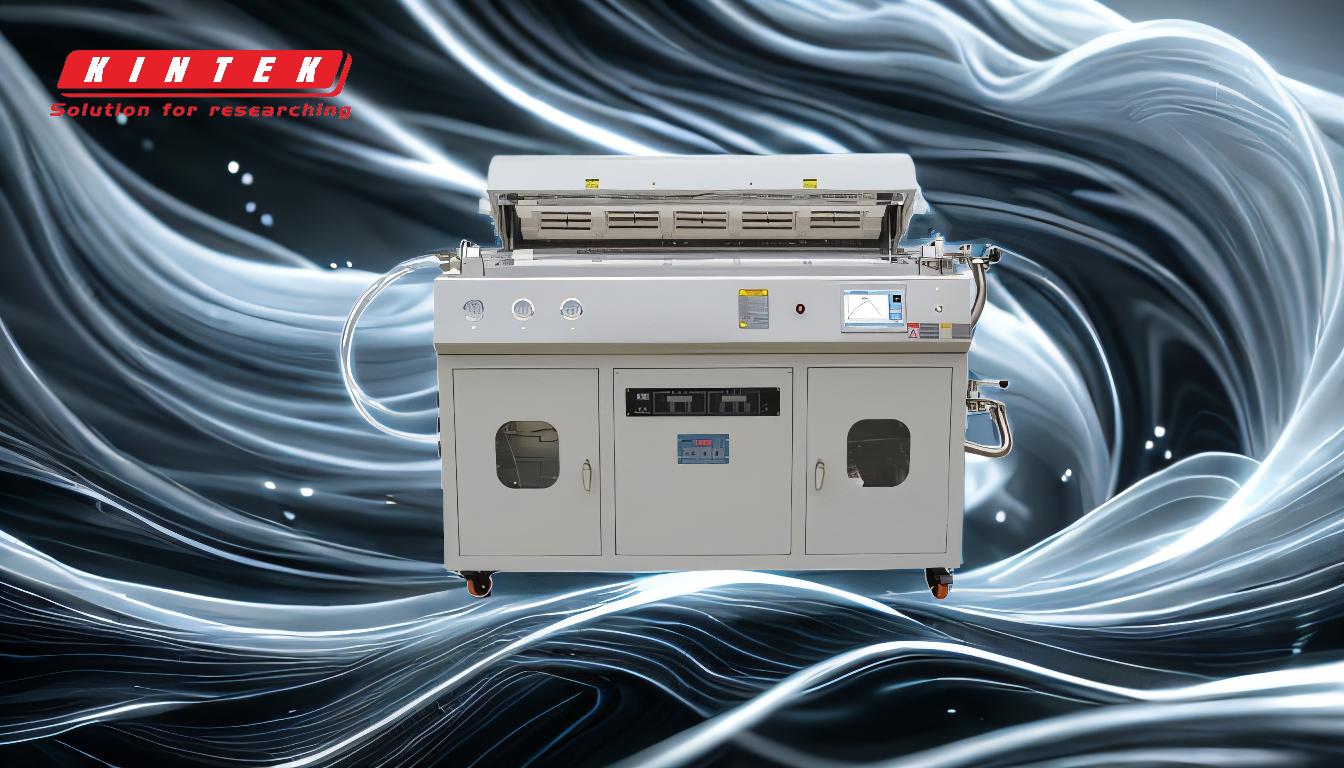
-
What is Physical Vapor Deposition (PVD)?
- PVD is a process where a solid or liquid source material is vaporized in a vacuum environment. The vaporized material then condenses onto a substrate, forming a thin film. This method is used to create coatings that are only a few atoms thick, making it ideal for applications requiring precision and durability, such as semiconductor manufacturing, optical coatings, and tool coatings.
-
Key Components of a PVD Apparatus:
- Vacuum Chamber: The process occurs in a vacuum to ensure that the vaporized atoms or molecules reach the substrate without colliding with residual gas molecules, which could otherwise disrupt the deposition process.
- Target Material: This is the solid or liquid material that is vaporized. It serves as the source of the coating material.
- Energy Source: An energy source, such as a high-power laser, electron beam, or plasma, is used to vaporize the target material. The choice of energy source depends on the specific PVD technique being used.
- Substrate Holder: The substrate, or the object to be coated, is placed on a holder within the vacuum chamber. The holder may rotate or move to ensure even coating.
- Control Systems: These systems monitor and regulate parameters such as pressure, temperature, and deposition rate to ensure consistent and high-quality results.
-
Categories of PVD Methods:
- Sputtering: In this method, the target material is bombarded with high-energy ions, causing atoms to be ejected from the target and deposited onto the substrate. Sputtering is commonly used for depositing metals and alloys.
- Evaporation: The target material is heated until it evaporates, and the vapor condenses onto the substrate. This method is often used for depositing metals and some ceramics.
- Ion Plating: This technique combines evaporation with ion bombardment. The substrate is bombarded with ions during deposition, which improves the adhesion and density of the coating.
-
Advantages of PVD:
- High-Quality Coatings: PVD produces thin films with excellent uniformity, adhesion, and durability.
- Versatility: A wide range of materials, including metals, ceramics, and composites, can be deposited using PVD.
- Environmentally Friendly: PVD is a clean process that produces minimal waste compared to other coating methods.
-
Applications of PVD:
- Semiconductors: PVD is used to deposit thin films of conductive and insulating materials in semiconductor devices.
- Optics: PVD is used to create anti-reflective, reflective, and protective coatings on lenses and mirrors.
- Tool Coatings: PVD coatings are applied to cutting tools to improve their wear resistance and lifespan.
-
Comparison with Chemical Vapor Deposition (CVD):
- While PVD involves the physical vaporization of a material, CVD relies on chemical reactions to deposit a thin film. In CVD, a precursor gas is introduced into a chamber, where it reacts or decomposes to form a solid film on the substrate. CVD typically requires higher temperatures than PVD and is often used for depositing materials that are difficult to vaporize physically, such as silicon dioxide or silicon nitride.
In summary, a physical vapor deposition apparatus is a critical tool in modern manufacturing and materials science, enabling the creation of high-performance coatings with precise control over thickness and composition. Its versatility and ability to produce high-quality films make it indispensable in industries ranging from electronics to aerospace.
Summary Table:
Aspect | Details |
---|---|
Process | Vaporizes solid/liquid material in a vacuum to deposit thin films on a substrate. |
Key Components | Vacuum chamber, target material, energy source, substrate holder, control systems. |
PVD Methods | Sputtering, evaporation, ion plating. |
Advantages | High-quality coatings, versatility, environmentally friendly. |
Applications | Semiconductors, optics, tool coatings. |
Comparison with CVD | PVD uses physical vaporization, while CVD relies on chemical reactions. |
Enhance your manufacturing process with advanced PVD technology—contact our experts today!